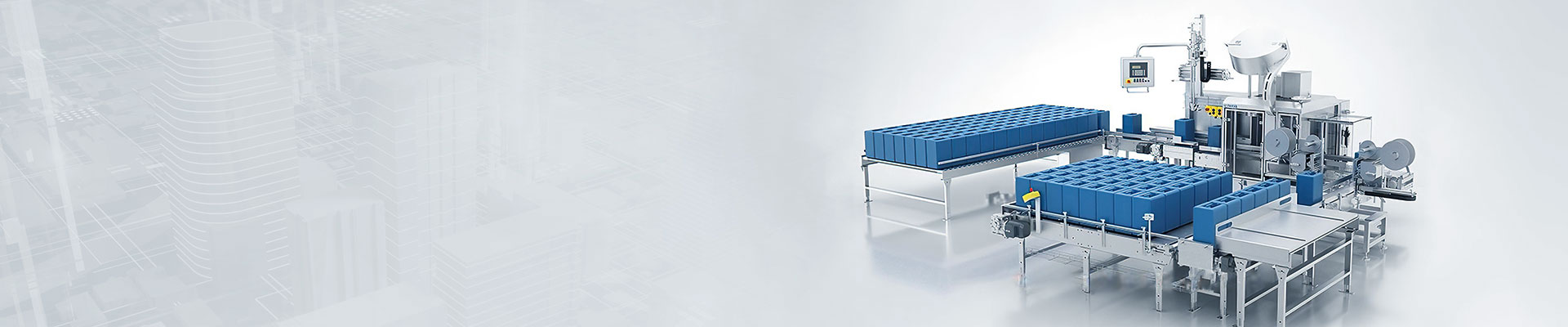
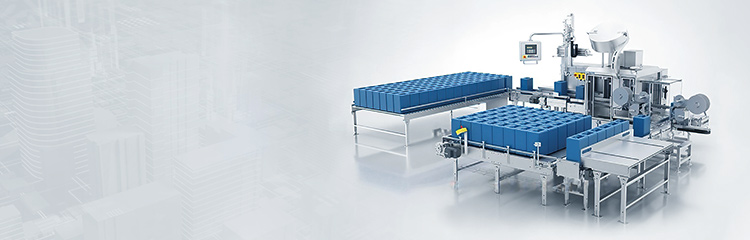
There are three types of automated mixing systems, namely, single tube center tube, multi-flow tube, and wall mounted. The wall mounted type is more commonly used, compared to the other two types of wall mounted granular material mixing and homogenizing silo mixing tube is closely connected to the silo wall, the central part does not need to be supported by a bracket and will not be deformed by stress, in addition to the granular material by gravity, the middle part of the fall speed is generally fast, wall mounted flow tube can greatly improve this problem. This feeding system is suitable for granular materials with good fluidity, for high mixing requirements, it is necessary to integrate the airflow type to the bottom of the silo 1/4 of the material back to the top of the material layer, so as to ensure that the quality of the entire silo product quality uniformity, and can also be connected to a number of blending silos to achieve uniformity of the entire product line.

Feeding system process is a number of raw materials in accordance with a certain ratio were through the corresponding feeding equipment, the raw materials will be conveyed to the measuring scale, measured and sent to the raw mill, through the raw mill grinding into raw materials, out of the mill mixture into the powder selector, selected fine powder into the carbon black production of subsequent operations, the coarse powder back to the raw mill to continue to powder. It is suitable for feeding powder and other materials, with stable operation, even feeding, low noise, easy installation and commissioning, simple control, and can be controlled by frequency converter to realize variable speed feeding. The spiral Feeder's screw is of variable pitch and diameter, and the crushing knife is added at the outlet, which can ensure that the materials are evenly added to the hopper.
Adopting photoelectric isolation switch quantity to control the start and stop of the frequency converter, using analog voltage signal to set the frequency of the frequency converter, the microcontroller adjusts the size of the frequency converter output frequency by changing the size of the analog voltage signal to change the rotational speed of the drive motor of the screw conveyor, so as to achieve the purpose of adjusting the feeding quantity.
The feeding system control program is responsible for the weighing and batching control when the screw feeder is feeding. Since the operation of the screw feeder is completely controlled by the frequency converter, and the dosage needs to obtain the raw material weight information from the weighing module to accurately control the weighing process, the program should call the frequency converter control program, the dosage algorithm subroutine, and the A/D interrupt processing. According to the raw material dosage algorithm to prepare the algorithm subroutine, run the program to generate the discharge flag bit, when the initial value of 0, that is, fast feeding; discharge flag position of 1, transfer to slow feeding. The frequency converter control program completes the variable speed control of the screw feeder.
Automatic mixing system is generally divided into three structures, respectively, single tube center tube type, multi-flow tube type, wall type. The walled type is more commonly used, compared with the other two ways walled granular material mixing and homogenization silo mixing pipe is closely connected to the silo wall, the central part does not need to be supported by brackets and will not be deformed, in addition to the granular material by gravity, generally the middle part of the falling speed, walled flow tube can greatly improve this problem. This feeding system is suitable for granular materials with good fluidity, for high mixing requirements, it is necessary to integrate the airflow type to the bottom of the silo 1/4 material back to the top of the material layer, so as to ensure that the quality of the entire silo product quality uniformity, can also be connected to a number of blending silo to achieve product uniformity of the entire line.