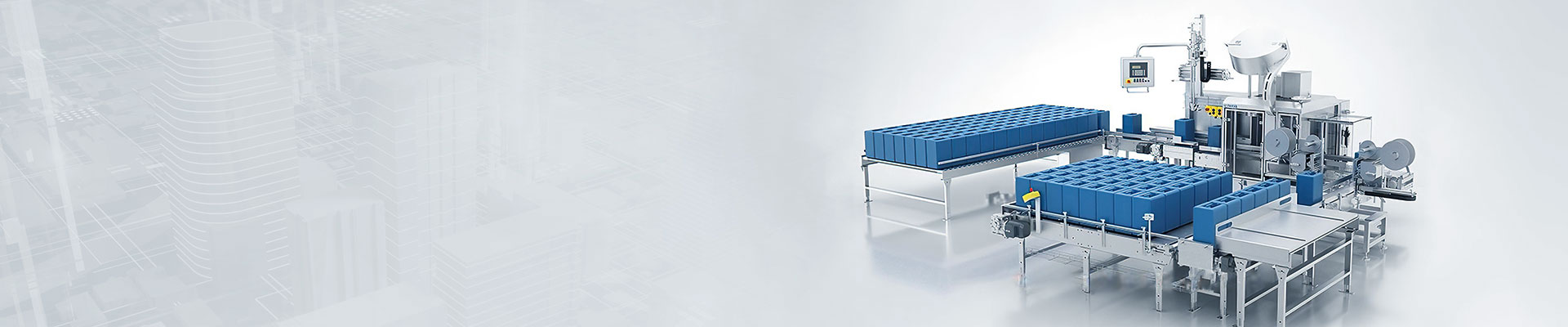
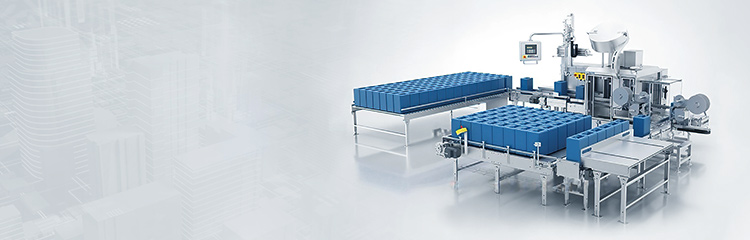
Ink filling machine adopts automatic liquid quantitative filling, high-precision electronic scale measurement method and automatic quantitative filling control of barrel raw material filling electrical operation, using high-precision weighing sensor, a new generation of electronic scale digital fixed value control system and imported PLC controller, weighing terminal, start, stop, cleaning, manual feed switch and button.

Automatic Filling machine adopts automatic liquid quantitative filling, high-precision Electronic scale measurement method and automatic quantitative filling control of barrel raw material filling electrical operation, using high-precision weighing sensor, a new generation of electronic scale digital fixed value control system and imported PLC controller, weighing terminal, start, stop, cleaning, manual feed switch and button. At the same time, it adopts the intelligent multi-function panel, the man-machine operation interface is simple and applicable, easy to modify, and realizes the complete man-machine dialogue state, which can be communicated and set quickly through the RS-422/485 interface. The hardware configuration and external wiring part includes one input and output module that can expand the analog quantity. It has a programmable controller with networking communication function and switching output, which can use the basic control unit of PLC to design its start and stop.
Automatic filling machine adopts the most widely used PID regulation in industrial control for actual flow control, according to the weight deviation, the use of proportion, integral, differential calculation of the control amount, through the frequency converter to adjust the motor speed to adjust the quantity, so that it is equal to the set value, complete the automatic filling process. The computer is connected with the weighing instrument through serial communication, which can collect and process the data in real time, input and save the data on the production line. The filling and packaging barrels are completed in sequence: barrel loading, barrel feeding, feeding, filling, barrel discharging, capping, sealing, stacking and other 9 steps. In normal operation, when the interlock switch is closed, the air pressure condition, the liquid level condition and other external signals are satisfied and normal, the start switch is in automatic operation mode after pressing, and each station on the filling line should be scanned according to the program programmed by the weighing instrument. It can communicate with the control host through RS485 network. RS485 distributed control system network can be easily formed by using multiple modules. Each network can be connected to a maximum of 255 modules in series, and the network can be connected to the control computer through RS232/RS485 conversion.