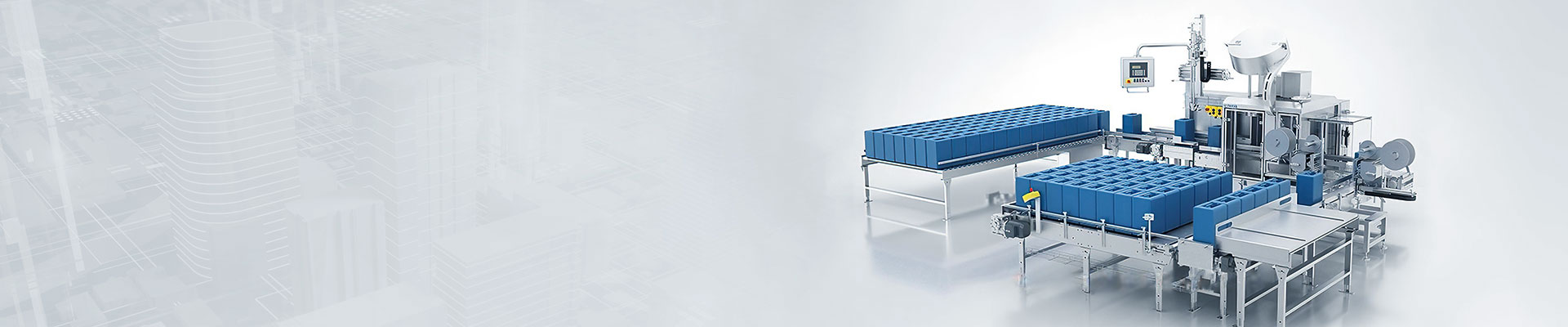
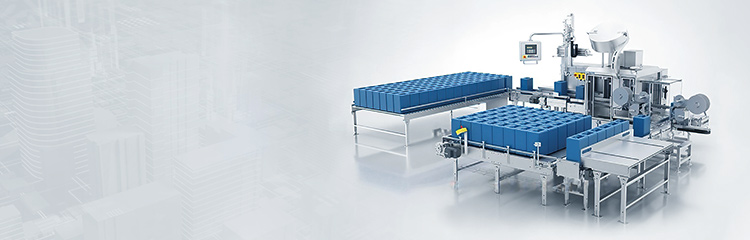
The weighing and distributing machine transforms into 4~20mA current as the input signal for system display and control through the weight transmitter. The current weight of the raw material barrel is taken as the starting weight setting value, and is set as the target dosing value through the display instrument or DCS system. When the weighing module detects that the weight in the canned barrel rises up to a certain value, at this time, the output current is basically in a linear relationship with the weight value, and in order to ensure the accuracy of each point, the liquid level signal of the filling barrel is taken as the control signal of the feeding valve for automatic adjustment of the liquid level parameters. In order to ensure the accuracy of each point, the liquid level signal of the filling barrel is used as the control signal of the feeding valve for the automatic adjustment of the liquid level parameter, so that the whole automatic filling machine realizes the automatic adjustment function of the continuous production process.

Automatic Filling machines are compatible with servo motor or cylinder driven pistons, multi-head filling is controlled by an automatic PLC and bottles are automatically stopped to control the filling head. Since piston filling is based entirely on traditional weighing and metering technology, these machines are easy to operate and relatively low cost for most end-use industries. Through the use of advanced load cells, control systems and filling mechanisms, it is possible to achieve fully automated operation, reducing the need for manual intervention. Raw materials are automatically acquired and conveyed to the filling as required by the production line, avoiding the tedious process of manual handling. At the same time, the automatic control system is able to monitor the parameters of the filling process and adjust the operation in real time to ensure that each package meets the expected standards.
The liquid dispensing metering used in the weighing and dispensing machine is determined by the time and flow rate per unit time, which is controlled and determined by the programmable logic controller (PLC), and the operation status is monitored through the human-machine interface-touch screen, and the operation parameters can be modified on-line. The filling machine is transformed into 4~20mA current as the input signal for system display and control through weight transmitter, the current weight of raw material barrel is used as the starting weight setting value, and is set as the target dosing value through the display instrument or DCS distribution system, when the weighing module detects that the weight in the canned barrel has risen to a certain value, at this time, the output current is basically in a linear relationship with the weight value, in order to ensure the accuracy of each point, the liquid level of the filling barrel is set at a certain value. In order to ensure the accuracy of each point, the liquid level signal of the filling barrel is used as the control signal of the feeding valve for the automatic adjustment of the liquid level parameter, so that the whole automatic filling machine realizes the automatic adjustment function of the continuous production process.
Basic parameters:
Maximum weighing capacity: 30kg
Minimum Sensitivity: 0.1kg
Filling error: ±0.1-0.2kg
Filling speed: 20L about 1500-1800 barrels/hour
Control mode: 2-speed control
Filling method: Insertion, liquid level up
Gun head line: Teflon gun head, valve + Teflon hose
Structure material: host SUS304 stainless steel, conveying palletizing carbon steel anticorrosion paint.
Weighing platform size: 400 × 800mm (304 stainless steel power raceway)
Empty barrel raceway: 400mm × 2500mm (304 stainless steel power raceway) with another 1200mm slope without power roller
Heavy drum raceway: 400mm×2500mm (304 stainless steel power raceway, 2 sets)
Separate barrel device: for 20L barrels, carbon steel anticorrosive paint structure, 304 stainless steel raceway.
Palletizing equipment: pan-transfer type, suitable for pallets 1200×1200×140mm, including supplying pallets, palletizing, and lower pallet conveying.
Pipe pressure: 0.2-0.6MPa (related to material properties).
Material interface: DN40 flange connector 4, according to the user to provide interface standards
Air Connection: User supplied 12mm air hose connector for quick coupling connection
Power supply: AC220/50Hz (user-supplied to one side of the machine)
Using air source: 0.4-0.8Mpa (provided by the user to the side of the machine)
Use temperature: -10℃-50℃
Base condition: Horizontal solid concrete floor, concrete thickness should be more than 10cm.
Optional models: standard, explosion-proof filling scale