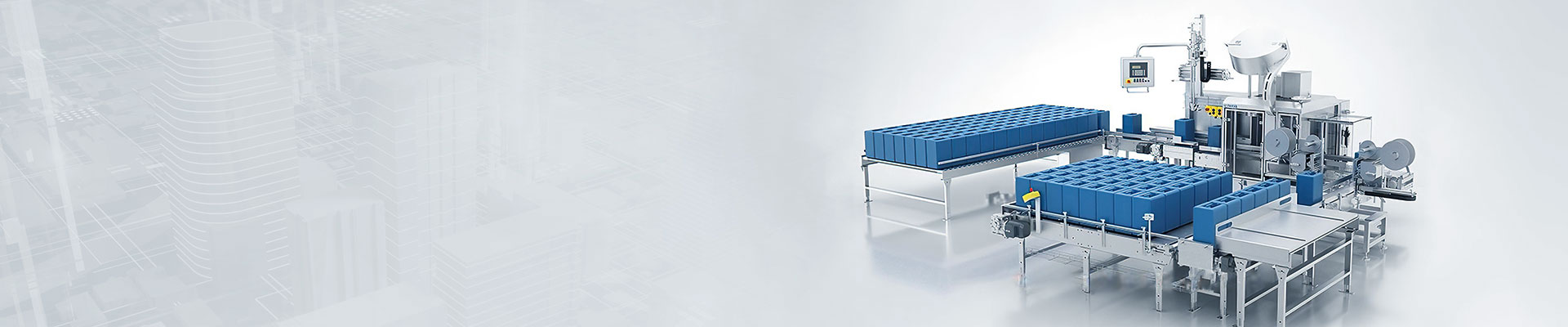
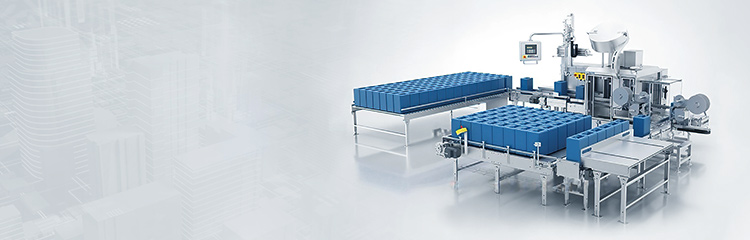
The automated filling machine adopts RS232 interface to connect the touch screen and PLC through communication cable, the remote touch screen (HMIA) and local touch screen (HMIB) are connected through Ethernet, both of them can display the instrument data and equipment status, and both of them can control the automatic filling machine. The upper computer completes the configuration and debugging of the weighing system, the online correction of the detection parameters and the setting of the control parameters, and also realizes the collection of the production data, the generation and printing of the report, the alarm of the abnormal signals and the network release of the information of the production site and other functions.

Automatic Filling machine based on industrial control computer and RS485 field bus to achieve the signal acquisition, processing, control and output, constitutes a cost-effective Weighing system; the use of local area network to achieve the field monitoring computer and management computer communication; weighing software using modular approach using VC + + compilation. The actual operation shows that the system is reliable, easy to maintain and use, friendly man-machine interface, and has good control effect.
Liquid filling machine mainly through the Electronic scale to realize the automatic control of the whole system, mainly to complete the automatic feeding, discharging, transportation, material filling and other functions. The Filling system adopts the industrial control machine filling centralized control mode, which is linked by a host and multiple slaves through the network, and the host will give the control task to each slave to complete. Filling machine through the pressure weighing module to pick up the weight, and will pick up the weight of the signal amplification, filtering, into the A/D converter for analog to digital conversion, and then sent to the microcontroller for signal analysis, processing, and the results of the RS232C communication serial port output to the industrial control, and at the same time, according to the results of the signal to make the appropriate response and perform the corresponding operation.
Basic parameters:
Maximum weighing capacity: 30kg
Minimum Sensitivity: 0.1kg
Filling error: ±0.1-0.2kg
Filling speed: 20L about 1500-1800 barrels/hour
Control mode: 2-speed control
Filling method: insertion type, liquid level up
Gun head line: Teflon gun head, valve + Teflon hose
Structure material: host SUS304 stainless steel, conveying palletizing carbon steel anticorrosion paint.
Weighing platform size: 400 × 800mm (304 stainless steel power raceway)
Empty barrel raceway: 400mm × 2500mm (304 stainless steel power raceway) with another 1200mm slope without power roller
Heavy drum raceway: 400mm×2500mm (304 stainless steel power raceway, 2 sets)
Separate barrel device: for 20L barrels, carbon steel anticorrosive paint structure, 304 stainless steel raceway.
Palletizing equipment: pan-transfer type, suitable for pallets 1200×1200×140mm, including supplying pallets, palletizing, and lower pallet conveying.
Pipe pressure: 0.2-0.6MPa (related to material properties).
Material interface: DN40 flange connector 4, according to the user to provide interface standards
Air Connection: User supplied 12mm air hose connector for quick coupling connection
Power supply: AC220/50Hz (user-supplied to one side of the machine)
Using air source: 0.4-0.8Mpa (provided by the user to the side of the machine)
Use temperature: -10℃-50℃
Base condition: Horizontal solid concrete floor, concrete thickness should be more than 10cm.
Optional models: standard, explosion-proof filling scale