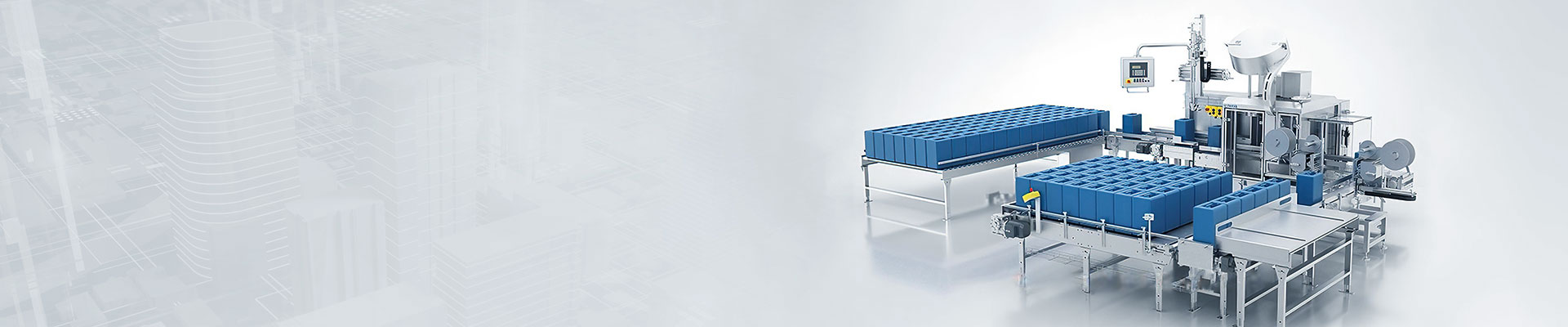
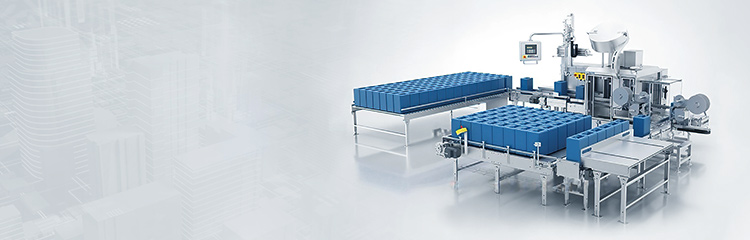
Weighing system is the process of automatically adding two or more kinds of materials into the mixing tank according to a certain weight ratio, and automatically discharging after mixing to meet the predetermined requirements. The batching system does not need the main console, only weighing module, terminal box, weighing control instrument, PLC wiring cabinet, touch screen, the main hardware is composed of two computers, high-performance microweighing controller, human-machine interface, high-speed and high-precision weighing unit and internationally famous low-voltage electrical appliances, combined with independent research and development of professional control software to achieve automatic control of production.

The feeding system adopts PID adjustment, measurement deviation combined with frequency conversion speed control, the main material and auxiliary materials are mixed in a certain proportion to complete the measurement of the reactor transport. PLC is mainly responsible for real-time control of conveying equipment and weighing process, and complete the system fault detection, display and alarm, while the inverter output signal to adjust the speed of the role. In this feeding system, a reactor bin containing various raw materials is mounted on a bracket. The back of the silo is equipped with a cylinder and a solenoid valve, the silo is driven by the cylinder, and when the solenoid valve receives the PLC instruction, it is opened and the silo is pushed out from the support, and the workers can take materials from the silo. On the one hand, PLC communicates with the host computer to receive instructions, on the other hand, it sends instructions to each solenoid valve to control the entry and exit of each bunker. The upper computer PC plays the super computing and processing power of the computer and the massive storage capacity. According to the requirements of the administrator, it makes a daily work plan and generates the standard weight and weighing order of each weighing component. The workers' errors in calculation were avoided. After the weighing procedure begins, the worker takes the material and weighs it on an Electronic scale. When the weight is not qualified, the computer starts the warning thread, then the next component bin cannot be opened, and the computer will only open the next bin when the weight is qualified. At this time, the computer will save the qualified weight data. This process ensures the stability of the production process, while eliminating the need for workers to find the next ingredient and improving production efficiency.
The batching software part is a visual computer operating system designed and developed for the monitoring and automatic batching of batching sections. It has the function of recipe library management. The intelligent report software provides a large amount of data information for production management, such as the list of batching results, the list of raw material consumption, the list of production capacity, and the record of recipe use results. It can produce statistics and printing functions such as daily, monthly and annual reports according to time and formula. At the same time, two user-defined report components are provided, one is the crystal report for secondary design; The other is to seamlessly embed the data into EXCEL reports. In addition, the system can interact with other management systems to meet the requirements of deep data analysis. The upper host will store the accumulated amount, ratio, start and stop time of each route in each run for easy query. The batching software part can automatically complete the system batching process, and the computer screen displays the Batching system in real time (workflow, software operation is simple, the picture is realistic. At the same time, it has the following features: the upper computer software sets the running password and password modification protection of important parameters, and the user realizes hierarchical management, and can arbitrarily define the rights of personnel.