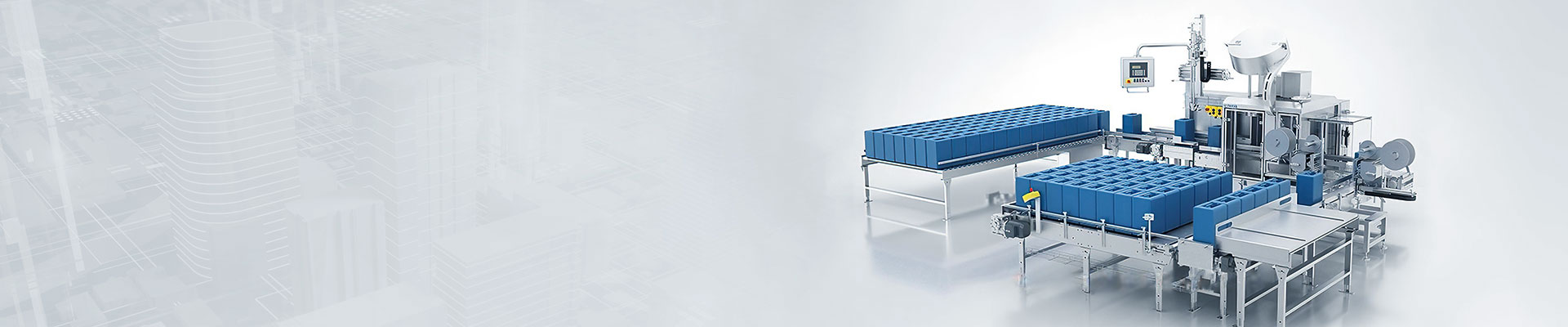
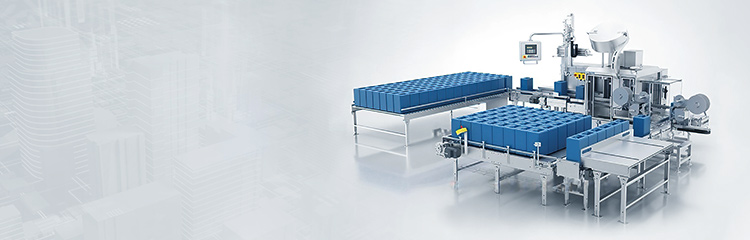
The automatic filling machine is mainly composed of filling management, metering and delivery control modules. The central control and management system is connected to the industrial Ethernet to obtain the filling request from the filling system in the workshop, optimize the scheduling, and send the filling instruction to the metering and transfer control system. After receiving the instruction, it opens the corresponding pipeline valves and uses centrifugal pumps and manipulators to carry out transmission and gripping, and automatically transports the product to the corresponding position for control.

Automatic Filling machine frequency control is the application of frequency conversion technology and microelectronics technology, by changing the motor operating power supply frequency mode to control the AC motor power control equipment. Utilizing the respective functions of frequency conversion control, it is designed to realize multi-step speed regulation. By the photoelectric switch and the internal timer to check the actual speed of the motor speed, and this speed as a feedback signal to control the motor speed, and then realize the filling conveyor speed automatic control. The purpose of automatic control is to make it consistent with the speed of the filling machine and save the filling time.
Liquid filling machine according to the bottle flow through the filling frequency control to adjust the speed of the conveyor belt, according to the bottle flow to choose a multi-stage speed control, to achieve the speed of the conveyor belt and weighing and filling machine speed is well matched. Filling frequency control motor rotation drives the belt drive, and then the bottle to be filled is transmitted to the weighing and filling machine, to achieve the coordination of the bottle flow speed and filling speed, thus improving work efficiency.
Filling machine start after pressing the motor positive switch, the motor began to rotate, drive the belt drive, to be filled bottles in the belt drive under the action of photoelectric sensors, weighing sensors for bottle counting sent to the filling machine for data processing, the processing of the bottle speed and memory inside the set value to compare, the output control signals to the filling machine frequency conversion control multi-stage speed control control terminal, frequency control to accept the control signals transmitted by the internal processing of the output voltage of a specific frequency to achieve the motor metering filling machine frequency conversion speed control. The frequency conversion control accepts the control signal transmitted by the internal processing, the output of a specific frequency voltage to realize the measurement of the motor filling machine frequency conversion speed control.
Technical Parameters
Weight range: 15~50kg
Material interface: DN40 material
Inlet pressure: <0.5MPa
Filling speed: 1~2 barrels (200L)/minute (through diameter 1.5", material flow rate guaranteed 280L/min)
Filling precision: 0.2 grade
Spray gun structure: the material in contact with the material part of the material is 316, 316L stainless steel, the rest of the material is 304 stainless steel, carbon steel, etc.
Gas source: pressure 0.5±0.1Mpa, consumption 10m3/h, quick connector 8㎜ gas pipe
Power supply: 220(-15%~+10%) VAC, 50Hz