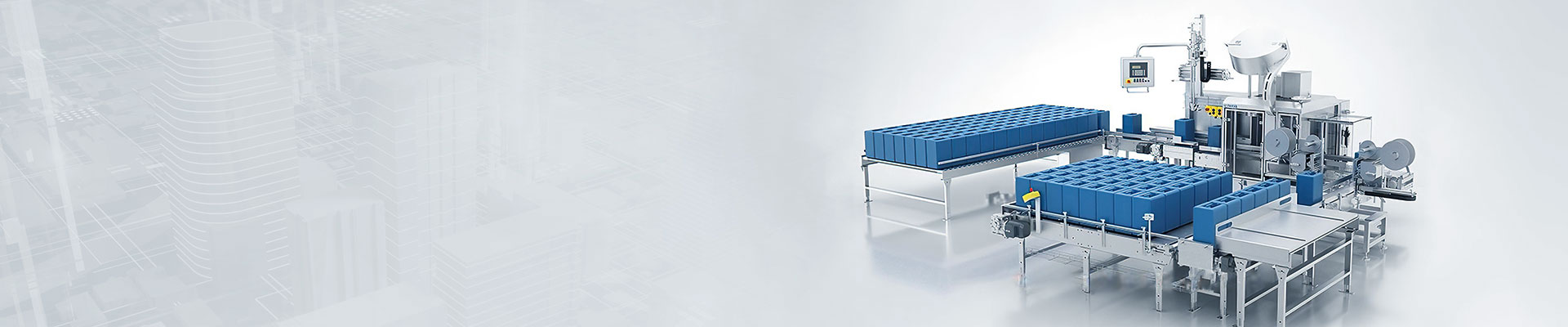
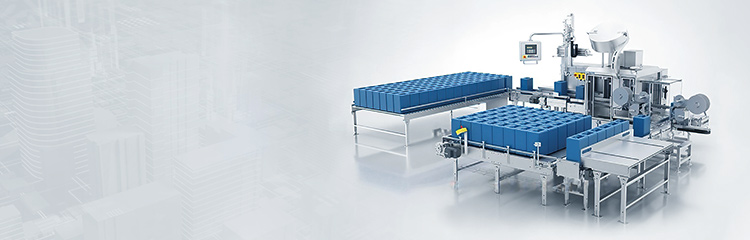
The automatic feeding system (e.g. dosing container with weighing device) reads the weight value at regular intervals, and the difference between the two weights is used to calculate the reduction per time unit (instantaneous flow rate). The weighing controller compares the actual measured value with the preset flow rate value, and at the same time controls the rotational speed of the auger feeder to regulate the feeding volume. When the weight of the material in the hopper reaches the minimum set value, the charging valve will be opened automatically to carry out the periodic charging operation. In order to ensure the correctness of the weighing results, an appropriate filter can be selected to filter the weighing signals during the measurement process.

The feeding system is to add two or more materials to the dosing tank automatically and quantitatively according to a certain weight ratio, and the stirring motor will be turned on and off after a specified time. When the mixing motor is closed, the material is ready to be sent out to the material tank under the drive of magnetic pump, and the weight generated by the weighing module and weighing instrument, the weight signal generated by the weighing instrument is amplified by the amplification module and then collected by PLC and computer, when the predetermined weight is reached, PLC drives to close the pneumatic valve, and the dosing process is completed once. After mixing to meet the predetermined requirements of the process of automatic discharge.
At the beginning of each dosage cycle, the difference between the previously set dosage amount and the actual dosage amount is sought as the compensation value of the set dosage amount in this cycle, in order to eliminate the cumulative error of the dosage amount of each scale; the whole automatic feeding system consists of the junction box of the weighing module, weighing instrument, junction cabinet, PLC control cabinet, and the main hardware consists of two computers, high-performance microcomputer controllers, human-computer interfaces, high-speed and high-precision weighing units and internationally renowned low-voltage electrical components. The main hardware consists of two computers, high-performance microcomputer controller, human-machine interface, high-speed and high-precision weighing unit and international famous low-voltage electrical components, combined with self-developed professional control software to realize the automation control of the production of chemical liquids; set up the "automatic" and "manual" two modes of work, the "manual" work is to complete a certain control link, such as a separate "add material", a separate "mixing" and a separate "discharge", allowing the "pause/continue" key to pause and allow the suspension of parameters to modify the state;" Automatic" work is to complete a complete cycle control cycle, including feeding, mixing, discharging and other links, "automatic" operation only allows "pause/continue" key is valid, the "manual" key is invalid, and can not modify the parameters; with an immediate stop function