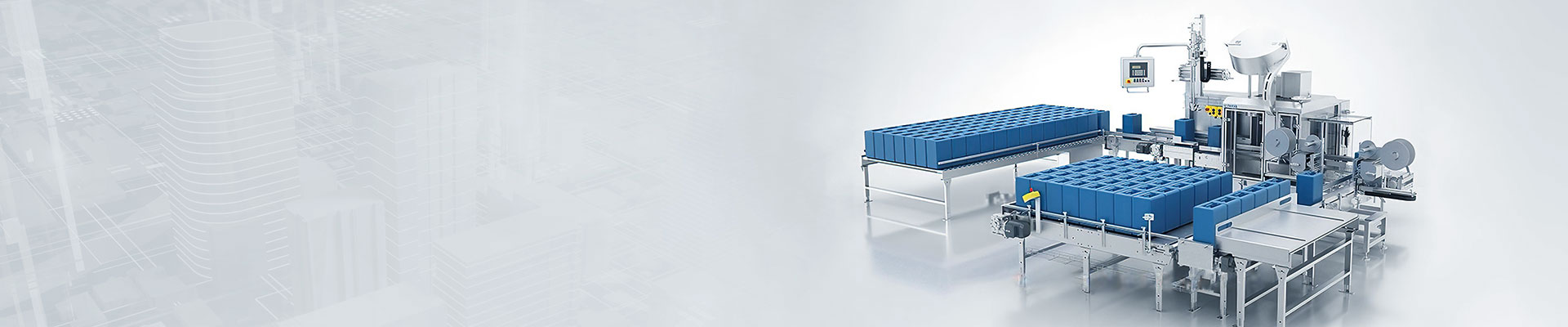
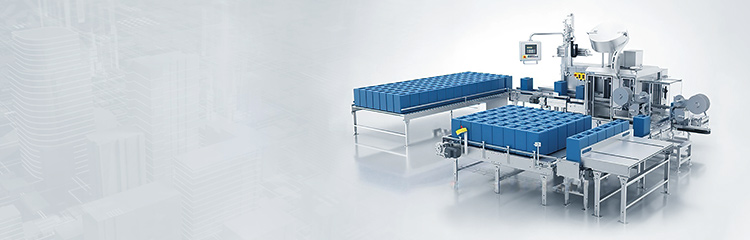
Quantitative filling machine using photoelectric imaging system to collect the image of the controlled target, by computer or special image processing module for digital processing, filling head down control motor to reach the weight to stop, the weight reaches the issued signal, the solenoid valve stops moving, the filling valve filling is complete, the filling nozzle rises, to complete the filling process.

Liquid Filling machine metering control system for Siemens S7-200PLC, mainly responsible for data reading and display, and give the relevant operating instructions and parameter settings. For example, when the detection unit found unqualified bottles will be immediately after the departure of the PLC counting, in order to accurately calculate the detection of the tail end of the machine the location of the second bottle, and send out the command to reject, so as to control the rejection mechanism will be pushed into the bypass by the second product.
The populated system consists of FASH and SDRAM, FLASH is mainly used for storing the system program code, the system reads the system program from FLASH every time power is supplied.SDRAM is a synchronous dynamic randomized memory with 3.3V operating voltage and 64-bit bandwidth, SDRAM locks the CPU and RAM together by the same clock, so that the RAM and the CPU can share clock cycles at the same time.SDRAM is based on a dual memory structure containing two interleaved memory arrays, when the CPU accesses data from one memory body or array, the other one is ready for data reading and writing. SDRAM is based on a dual memory structure, containing two interleaved storage arrays, when the CPU accesses data from one memory or array, the other is ready for data reading and writing, through the close switching of the two storage arrays, the reading efficiency has been improved exponentially Display unit mainly consists of LCD, LCD controller (S3C2400) touch screen, LCD is able to The LCD can display the image processing structure in real time, and the touch screen is mainly responsible for the control of the PLC system.I/0 unit is mainly used for the input and output control of the system, and the system controls the action of the aliasing mechanism through the output and input of the I/0 digital quantity.
Technical Parameters
Weight range: 10~60kg
Material interface: DN40 material
Inlet pressure: <0.6MPa
Filling speed: 5~8 buckets (200L)/minute (through diameter 1.5", material flow rate guaranteed 280L/min)
Filling accuracy: 0.2 grade
Spray gun structure: the material in contact with the material part of the material is 316, 316L stainless steel, the rest of the material is 304 stainless steel, carbon steel, etc.
Gas source: Pressure 0.5±0.1Mp, consumption 10m3/h, quick connector 8㎜ gas pipe
Power supply: 220(-15%~+10%) VAC, 50Hz