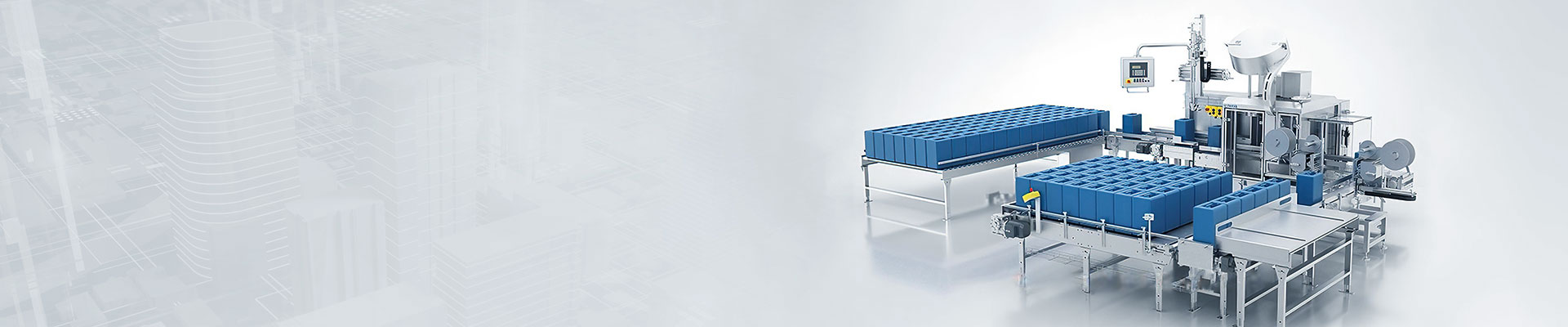
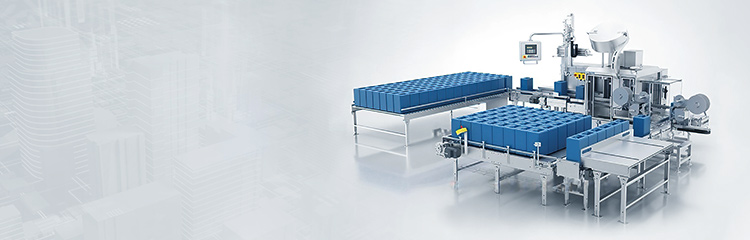
Weighing and mixing machine contains weighing instrument, weighing module, frequency converter and field control box. And leave the communication interface with the upper computer. The material is conveyed into the mixer. The weight signal is sent to the weighing instrument. Weighing instrument will load the weight signal through the operation and processing of the material weight, respectively, in the weighing instrument display. Weighing instrument and frequency converter control the screw conveyor speed to form a closed loop control. The built-in intelligent software regulator of the weighing instrument can set high, medium and low feeding to ensure the accuracy of dosage. The output of three sets of signals is used to control the frequency converter, which in turn controls the feeding speed of the screw feeder, thus achieving the purpose of accurate dosage. The weighing meter can set the feeding quantity manually or set the proportion through the two-way communication between computer and meter.

Weighing and mixing machine contains weighing instrument, weighing module, etc., frequency converter and field control box. And leave the communication interface with the upper computer. The material is conveyed into the mixer. The weight signal is sent to the weighing instrument. Weighing instrument will load the weight signal through the operation and processing of the material weight, respectively, in the weighing instrument display. Weighing instrument and frequency converter control the screw conveyor speed to form a closed loop control. The built-in intelligent software regulator of the weighing instrument can set high, medium and low feeding to ensure the accuracy of dosage. The output of three sets of signals is used to control the frequency converter, which in turn controls the feeding speed of the screw Feeder, thus achieving the purpose of accurate dosage. The weighing meter can set the feeding quantity manually or set the proportion through the two-way communication between computer and meter.
Conveying system occupies a large proportion in the fully automatic blending system: it includes the conveying of raw materials from the bag opening station to the excessive silo above the dosage scale, the conveying of finished products from the blending machine to the finished product silo, and the conveying of finished products from the finished product silo to the extruder. There are two main forms of application: screw conveying and pneumatic conveying, and pneumatic conveying can be selected according to the actual site of the dilute phase positive pressure. Sparse phase negative pressure. Dense phase positive pressure and so on several ways.
Screw conveyor is composed of motor, reducer and screw body. Simple structure, reliable work, but the cost is higher when the conveying distance is longer; the core part of the conveying system is a storage type pneumatic sending pump (referred to as warehouse pump); warehouse pump consists of a warehouse body, butterfly valves, exhaust valves, feeding port, gas piping and other components. For the dense phase pneumatic conveying system in the main equipment. When the compressed air into the sender of the inlet valve, and then from the inlet valve to the cone inside the protruding air nozzle, so that the gas generates eddy current. With the increase of pressure inside the sender, the material to be sent into the vortex flow, in order to achieve the purpose of smooth material transportation. Low speed and high concentration conveying can be realized by using low air pressure. High concentration conveying.
The feeding system has the advantages of low noise, long conveying distance, low energy consumption, and low wear and tear of the pipeline with large conveying capacity. And because of its high working pressure (0.15 ~ 0.3MPa), so it will not form a blockage in the pipeline, and because in the pipeline every certain distance to increase a set of boosting device so that the material in the pipeline was bolted (i.e., a section of the mutually spaced column of air and material columns) forward movement, so it is impossible to material segregation and delamination of the phenomenon, especially suitable for mixed material conveying, and the use of boosting devices can also effectively reduce the speed of material forward. The use of boosting device can also effectively reduce the forward speed of materials.
Roots fan is responsible for providing the low-pressure air needed for conveying materials, in order to ensure the stability of air pressure, the upper part of Roots fan is specially equipped with a certain volume of air storage packages, the rotary feeder is a dosing device, which ensures continuous and uniform dosing, as the rotary feeder is used in conjunction with the Roots fan.