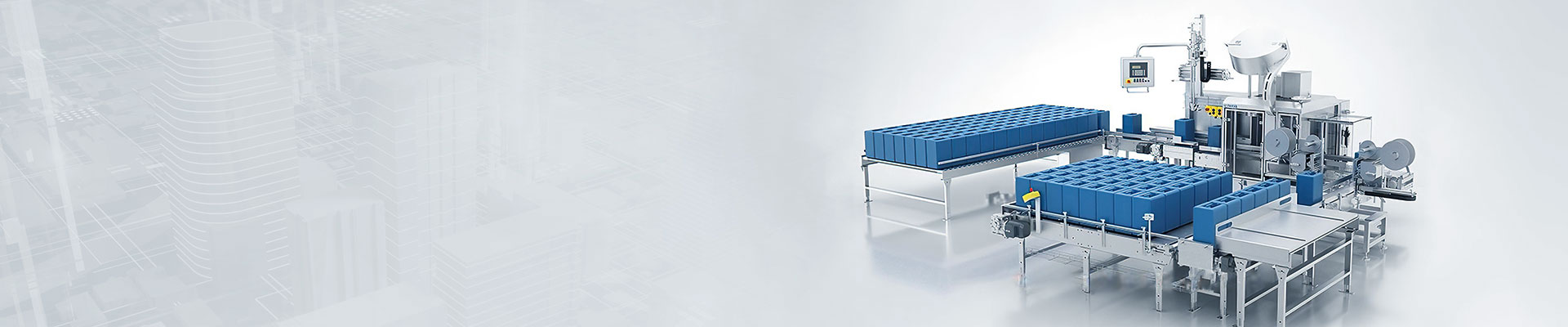
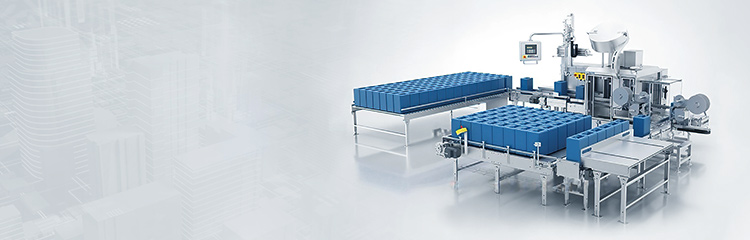
The mixture dosing system integrates weighing, display and complete dosing control. Provide fast and slow feeding speed to ensure the accuracy of dosing. It provides printing function of formula, actual weight of ingredients and accumulated value of blanking to facilitate the management and statistics of production data.

The mixing system adopts continuous ratio mixing technology, the flow meter is set by the proportional regulator, and the flow rate of the two monomer materials is controlled by the regulating valve. The materials are fully mixed by the static mixer, and adjusted in time through online laboratory analysis. The mixing monomer in the batching buffer tank is continuously circulated through the circulating mixing pump, and the mixing injector in the buffer tank is continuously mixed to ensure that the mixing monomer is uniform and the ratio is stable.
The heat of polymerization of acrylonitrile is higher than that of styrene. The reaction temperature drops. The polymerization rate decreased and the polymerization conversion rate increased gradually with the increase of time. The reaction temperature has great influence on the polymerization rate. The temperature of the reactor is controlled in the following ways: increase the reflux condenser, let part of the vaporized material enter the reflux condenser and then return to the reactor, and the material vaporizes to liquify and release latent heat, which is carried away by the cooling medium; The sensible heat of the material is used to absorb the reaction heat, the feed is pre-cooled to 3℃, and the reaction temperature is controlled at 155~C. The absorption reaction heat is installed in the reaction kettle, and the low temperature heat medium is passed into the reactor to remove the reaction heat.
According to the different boiling points of styrene and acrylonitrile monomer and the characteristics of low pressure vaporization, the acrylonitrile monomer with low boiling point was removed in a first-stage devolatilizer. At the same time, the lower temperature and vacuum of the first-stage devolatiler can reduce the gas phase of the reactor into the devolatiler, and avoid the fluctuation of the operating parameters and product quality of the devolatiler. Styrene monomer with higher boiling point and solvent ethylbenzene were removed in a secondary devolatilizer. The devolatilized gas enters the condenser for condensation, collection, and recycling. The advantages of two-stage devolatilization: The first-stage devolatilization device removes acrylonitrile at low temperature, and the yellowness of the product is small; The two-stage devolatilizer has high temperature and vacuum degree, reducing the content of product residues; Two-stage devolatilization, condensate reuse. Low material consumption. Through the two-stage devolatilization, the residual monomer of the product is below 1100ppm and the yellowness of the product is low.