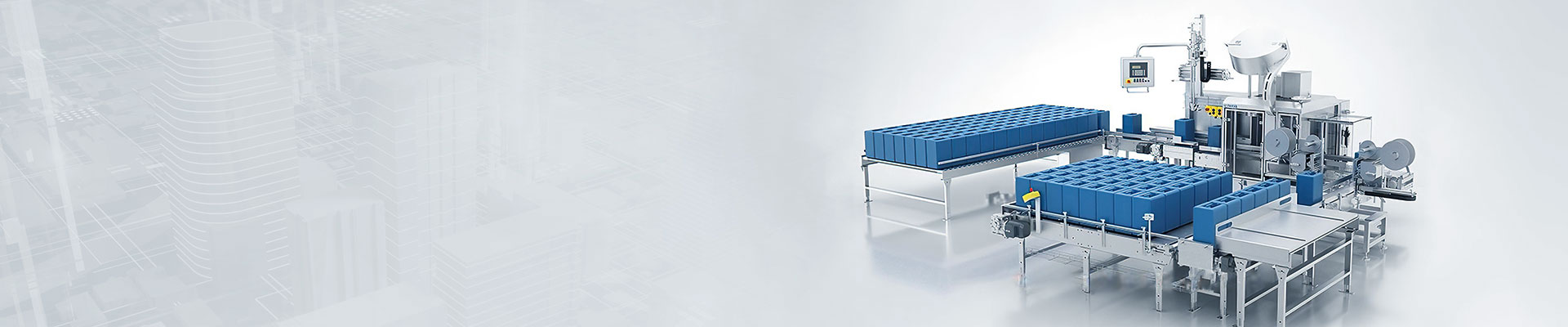
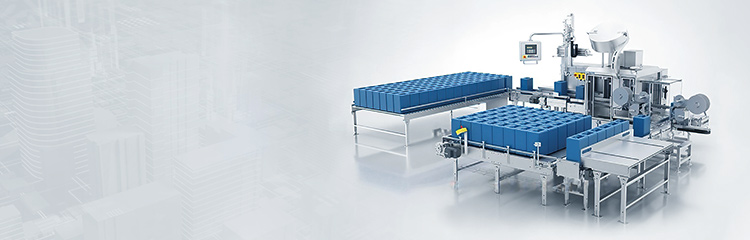
The process of weighing system is mainly the batching metering and feeding process. In batching metering process, firstly, the time of discharging from the material feeder to the metering tank is controlled according to the weighing requirements, so as to control the amount of material entering the metering bin, and then the time of discharging from the feeder to the metering tank is controlled according to the material proportioning requirements, so as to control the weight entering the metering tank, thus completing the weighing process once until the specified weighing times for each batching are completed.

The negative pressure Weighing system has the professional performance test and analysis ability of powder, granule and block materials, and the big data storage foundation of sample analysis for pipeline diversion. Can make more accurate determination of transportation parameters and pipeline optimization design ability for specific projects, so as to reduce various influencing factors in transportation.
Weighing dosing machine achieves the requirements of batching control accuracy and reduces the cost as much as possible through the dosage ratio of each raw material. According to the difference of each batch of materials, the optimization calculation table is input into the database, and a visual man-machine interface is developed by using VisualBasic, so that the calculation data can be read and displayed in the interface, and the database application program can be created visually, which makes the application of the database more convenient and flexible, and supports the application of the network environment.
Pressurized dense-phase pneumatic conveying is often used to convey materials with low speed and long distance and large conveying capacity. It can realize single-point to single-point and single-point to multi-point long-distance transportation in the conveying process, and can also complete drying, crushing, screening and mixing in the conveying process.
Dense-phase pneumatic conveying system equipment includes: air system (air compressor+cold dryer+filter+gas storage tank, etc.), conveying bin pump system, pipeline system, dust removal system and control interlocking system equipment.
The weighing and Batching system provides a man-machine interactive interface, and completes the functions of controlling information input, data management, data display, storage, statistics and reports. The industrial computer inputs the weight of batching through the host keyboard, generates the weight of various materials according to the proportion of raw materials, and transmits it to PLC through communication. In the process of batching, dynamic real-time monitoring is carried out, and other switching values in the detection and control system sent by each slave machine are collected regularly, and the weight signals of each material are collected in real time and compared with the given signals to determine the next control scheme, and at the same time, the weight signals are transmitted to the upper computer.
Characteristics of negative pressure weighing system of mixer
1. Simple and reliable configuration
The weighing control system is simple in configuration, and different warehouse pump transmitters are determined according to the parameters and conveying capacity of different materials. There are few rotating parts in the system, only the feed valve and the discharge valve are rotating parts, and there are no other auxiliary equipment; The operation mode is flexible and changeable, and it can run continuously or regularly.
2, the conveying material gas ratio is high.
The weighing system adopts high-density high-pressure plug-flow conveying, which consumes less compressed air and can convey more materials, and the ratio of conveying material to gas can be as high as 60-70. Taking the fly ash transportation with a distance of 100m as an example, the ratio of ash to gas can be as high as 70kg/kg, and its air consumption is only 1/2 ~ 2/3 of other forms of pneumatic transportation systems.
3, the energy consumption of ingredient conveying is low.
Due to the small amount of compressed air and low conveying pressure, the energy consumption of conveying is much lower than that of other forms of pneumatic conveying systems. The energy consumption per 100 meters per ton of conveying capacity is 1.5KW, which is about 65% of that of other pneumatic conveying forms.
4. The conveying speed of the weighing system is low
The conveying speed of batching control system is low, with the initial outlet speed of 5m/s and the final speed of 15m/s (depending on the distance).
5, pipeline wear is small.
Because of the low conveying speed, and the pipeline wear of pneumatic conveying is proportional to the conveying velocity, reducing the pipeline velocity will greatly reduce the pipeline wear, prolong the service life and reduce the operating cost.
6, low operation and maintenance costs
Because the system configuration is simple, the equipment is few, the required installation height of the outlet flange of the ash hopper of the electrostatic precipitator is also low, and because of the reliable equipment, less maintenance and low energy consumption of the system, the safe and reliable operation of the system can be guaranteed at a low cost.
7. The feed valve adopts advanced pneumatic dome valve.
The valve is reliable in structure, long in service life, easy to repair and maintain, and adopts advanced air-tight structure. When the valve is opened and closed, there is no contact between the valve core and the inflatable sealing ring, which can ensure the service life of 500,000 times.
8. The discharge valve adopts a unique alloy rotary valve (ceramic valve).
The valve has reliable structure and high machining accuracy, and is specially developed for plug-flow pneumatic conveying system. Smooth transition between valve core and pipeline, no curvature change, suitable for dense phase plug flow transportation, and wear-resistant valve core is adopted to ensure service life of 500,000 times.
9. The valve pneumatic actuators has reliable performance, long service life and large thrust.
Pneumatic actuators adopts fully enclosed rotary push rod, driven by straight cylinder, with track conversion in closed cavity and rotary output. Even if it is used in bad working conditions, it will not cause internal leakage due to the wear of actuator seals.
10. The control level of ingredients is high
The feeding system adopts advanced programmable controller (PLC), which has three control modes: automatic control, remote operation and local manual control. Under normal circumstances, the automatic control mode is adopted. The control system can realize automatic collection of operation data and fault signals, automatic analysis and fault judgment of operation data, and realize classified alarm of faults in the system.