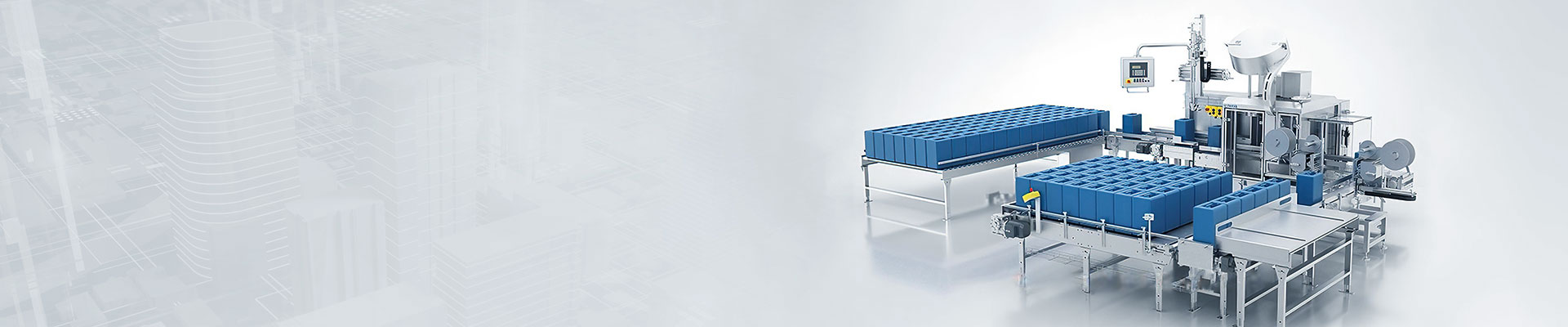
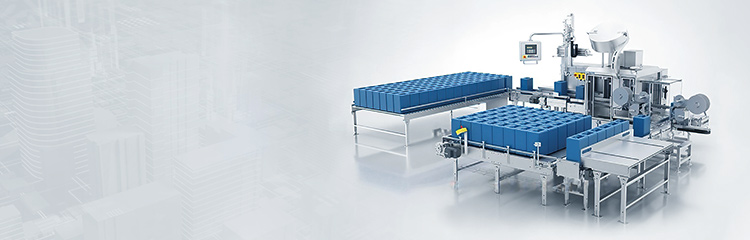

负压称重系统有着专业的粉、粒、块料性能试验分析能力和输送管道分流的样本分析大数据储备基础。能针对具体项目做出较为精确的输送参数确定和管道优化设计能力,以降低输送中的各种影响因素。
称重配料机通过各原料的用量配比,达到配料控制精度的要求、尽量降低成本。根据每批物料的不同而任意改变,优化计算表输入数据库利用VisualBasic开发可视化的人机界面,读取计算数据并显示在界面中,可视化的创建数据库应用程序,使数据库的应用更加便捷、灵活,同时支持网络环境的应用。
压送式浓相气力输送常用于低速远距离大输送能力的物料运送,可以在输送过程中实现单点对单点,单点对多点的长距离的输送,同样可以在输送过程中完成干燥、破碎、筛分、混合等工艺处理。
浓相气力输送系统设备包括:空气系统(空压机+冷干机+过滤器+储气罐等)、输送仓泵系统、管道系统、除尘系统及控制连锁系统设备。
称重配料系统提供人机交互界面,完成控制信息输人、数据管理、进行数据显示、存储、统计和报表等功能,工控机通过主机键盘输人配料的重量,根据原料的配比,生成各种物料的重量,通过通信传送给PLC。配料过程中,进行动态实时监视,定时收集各从机发送来的检测和控制系统中的其它开关量,实时收集各物料的重量信号并与给定信号比较,决定下一步的控制方案,同时将重量信号传送给上位机。
混合机负压称重系统特点
1、配置简洁可靠
称重控制系统配置简洁,根据不同物料的参数及输送量来确定不同的仓泵发送器,系统内转动部件少,只有进料阀和出料阀为转动部件,无其他辅助设备;运行方式灵活多变,可连续运行,也可定期运行。
2、输送料气比高
称重系统采用高密度的高压栓流式输送,消耗较少的压缩空气可以输送较多的物料,输送料气比可高达60-70。以100m距离的粉煤灰输送为例,输送灰气比可高达70kg/kg,其空气消耗量仅为其他形式的气力输送系统的1/2~2/3。
3、配料输送能耗低
由于输送等量物料需要的压缩空气量较小,且输送压力较低,因此输送能耗远低于其他形式的气力输送系统。吨输送量每百米能耗为1.5KW,是其他气力输送形式输送能耗量的65%左右。
4、称重系统输送流速低
配料控制系统输送速度低,出口初速度为5m/s,末速度为15m/s(视距离而定)。
5、管道磨损小
由于采用较低的输送速度,而气力输送的管道磨损与输送流速成立方比例,降低管道流速必然大大降低管道磨损,增长了使用寿命,降低了运行费用。
6、运行维护费用低
由于系统配置简洁,设备少,要求的电除尘器灰斗出口法兰安装高度也较低,而且由于设备可靠,检修维护量少,系统能耗低,所以只需较低的费用就可保证系统安全可靠运行。
7、进料阀采用先进的气动圆顶阀
阀门结构可靠,寿命长,检修维护简便,采用先进的气封式结构,阀门启闭时阀芯与可充气密封圈之间无接触,可确保使用寿命可达50万次。
8、出料阀采用独特的合金旋转阀(陶瓷阀)
阀门结构可靠,加工精度高,专为栓流式气力输送系统研制。阀芯与管道平滑过渡,无曲率变化,适合于浓相栓流式输送,采用耐磨阀芯,确保使用寿命达到50万次。
9、阀门气动执行器性能可靠,寿命长,推力大
气动执行器采用全封闭回转推杆式,采用直缸驱动,封闭腔内轨迹转换,回转输出,即使用于恶劣工况,也不会由于执行器密封件的磨损而导致内泄漏。
10、配料控制水平高
投料系统采用先进的可编程控制器(PLC),有自动控制、远方操作和就地手动控制三种控制方式,正常情况下采用自动控制方式。控制系统可实现运行数据和故障信号的采集自动化,对运行数据自动分析和故障判断,并对系统中的故障实现分类报警。