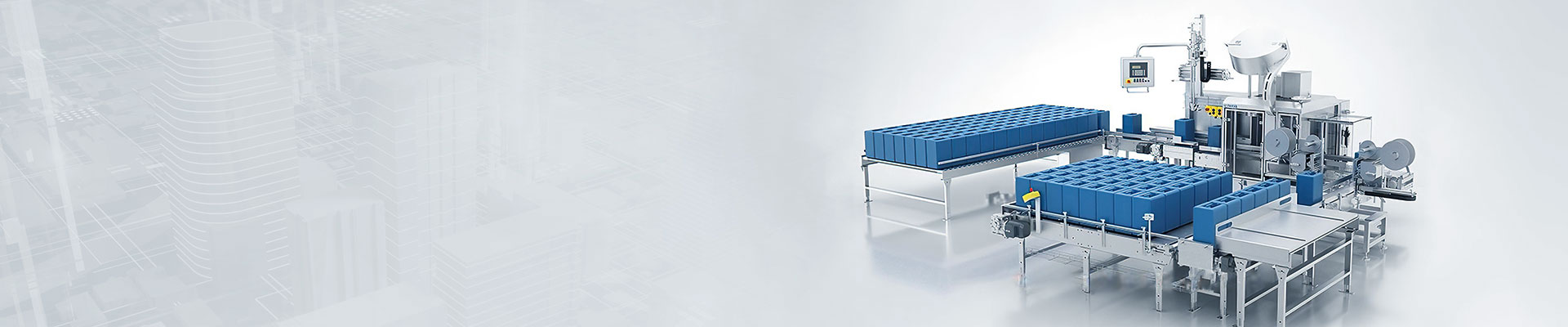
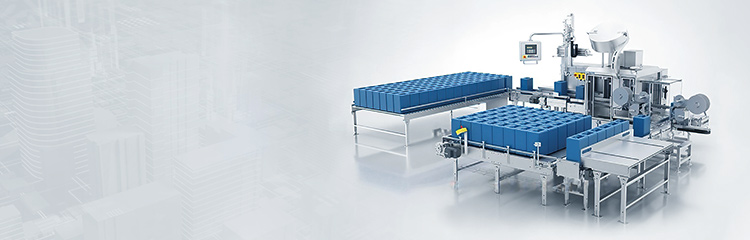
The charging machine adopts Siemens MMI software WINCC, and the system is mainly divided into four screens: process flow screen, parameter setting, centralized control, trend curve and report. In addition, in the process flow, there are main material feeding unit, dosing unit, vacuum feeding unit, mixing unit, finished material unit, pulse valve parameter setting, weighing instrument parameter setting, temperature alarm limit setting, motor current display, valve summary control, temperature alarm curve.

The feeding system scheme takes the vacuum Feeder as the control unit, and each vacuum feeder is equipped with a recipe setting boundary to feed and convey different recipes, so as to flexibly meet the requirements of different production batches and different recipes. Formula, feeding and discharging are all controlled by computer.
In addition to the hopper, the scale body includes dynamic weighing module, precision amplifier, A/D converter, microcomputer, display, printer and execution system. The touch screen control system can control multiple stirrers, and can control the time of dry mixing and wet mixing. It can prepare several to dozens of materials, display the batching process and print the name, quality, total quality, cycle time, formula, daily report and monthly report of each material at the same time.
The feeding system can provide rich software and convenient program modification, and it is a product with high degree of automation. Through weighing instrument or touch screen, the required weights of various materials are set, which are automatically transported to dosing machine by the auger in sequence for automatic weighing and flow control, so as to realize accurate metering and batching.
The feeding system uses compressed gas as the power source and the conveying medium. Forced pneumatic conveying is adopted, and the closed pressure vessel (sending tank) is used as the transmitter. Generally, the air source pressure is 0.5 MPa ~ 0.7 MPa, and the operating pressure is 0.3 ~ 0.5 MPa. The sending tank can only adopt intermittent conveying mode, and the conveying distance can reach more than 1000m m.. The transportation of materials in the pipeline at low speed, sand dune state, fluidization or agglomeration state is called positive pressure dense phase transportation. High-pressure roots blower can also be used.
According to the transportation characteristics, the system can also be divided into two ways: positive pressure dense phase dynamic pressure transportation and positive pressure dense phase plug transportation. The way in which materials are transported in the pipeline in the state of medium-low velocity sand dunes or fluidization is called dense-phase dynamic pressure transportation; The way in which materials are transported in the pipeline at a low speed in an agglomerated state is called dense-phase plug transportation.
Basic principle:
Due to the pressure, the material enters the conveying pipe from the sending tank, and the compressed gas is opened and closed by the electromagnetic valve at a certain frequency to form a pulse airflow (air knife). With the help of the pressure of the air knife greater than that of the sending tank, the material is cut into material plugs, and the static pressure difference before and after the material plugs is used as the driving force to push the material forward. After reaching the separation device to separate the material from the gas, the material falls into the silo and the gas is discharged into the atmosphere, thus realizing the conveying.
Product features:
1. Low flow rate but large conveying capacity has little influence on material quality;
2. The system has high pressure and low gas consumption;
3. The control system is automatic, which has high requirements for various electrical components;
4. Multi-point feeding and multi-point discharging are possible;
5. Due to the low material conveying speed, the pipeline and material wear is low;
6. The sending tank (also called warehouse pump) is a pressure vessel, which is a compulsory signing equipment;
7. The air source is generally a screw air compressor, and the post-processing equipment must be matched;
8. The system is reliable and requires little maintenance, but it requires high quality of operating technicians.
9. The conveying gas volume is small, and the separation of material and gas is easy to realize.
10. The working pressure is high, so long-distance transportation can be realized; The booster can be used to realize ultra-long distance transportation;
Basic parameters:
1. Positive pressure dense phase dynamic pressure conveying:
Air speed: 8m/s-15m/s, conveying capacity: 3-50th, conveying distance: up to 100-1000m, air source type: Roots blower, air compressor.
2. Positive-pressure dense-phase embolic transportation:
Air speed: 4m/s-12m/s, transport capacity: 2-20/h, transport distance: up to 50-200m.