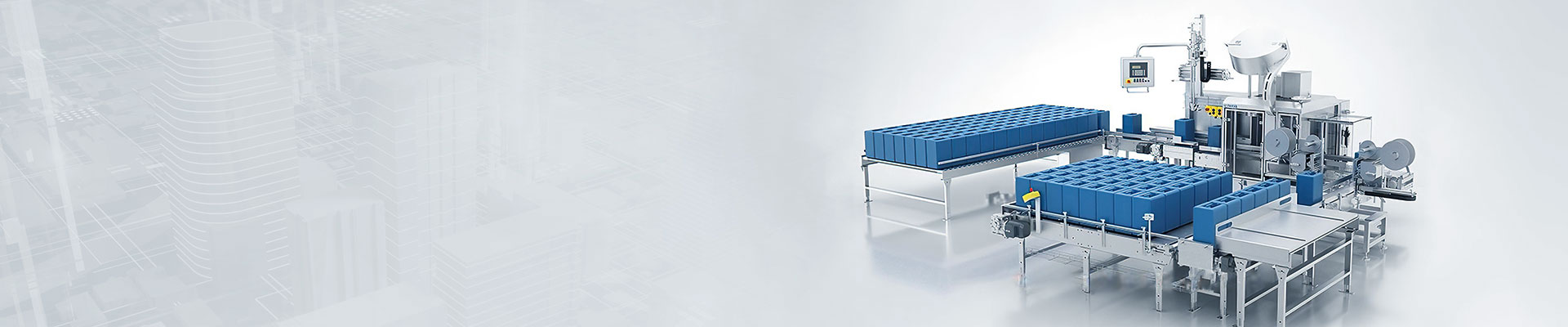
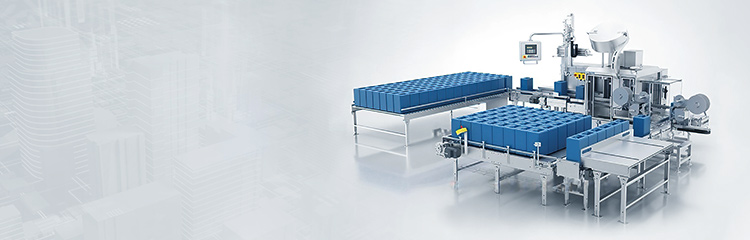
Speed dosing machine through the touch screen to complete the field dosing control and formula weight collection, the field operator only need to carry out the necessary manual intervention, you can complete the entire production, avoid human error, but also improve the production efficiency. With rich functions such as production monitoring, recipe management, batch statistics, alarm prompt and report printing, it is very suitable for real-time, multi-task control. Through the supporting communication interface, the relevant production information can also be uploaded to the data server or ERP to achieve information sharing.

The feeding system mainly consists of two parts: storage bin, filtering body and rotary conveying body. The weighing instrument consists of front circuit, display circuit and microcontroller communication circuit. The function of the digital radio module is to forward data, receive and send signals between the weighing instrument and the computer in the central monitoring room. The weighing and mixing machine integrates computer technology, automatic control, communication technology and weighing technology as a whole, with perfect control function, display, centralized operation, convenient data processing, simple installation and maintenance, easy expansion of the system, which solves the problem of "dangerous centralization" of computer centralized Dosage system, and achieves "management centralized and dangerous decentralization", and the system is stable and reliable to satisfy the use in the process of continuous production. The communication between monitoring computer and module adopts RS232 to RS485 interface.
The speed regulating batching machine is composed of silo, loading electric vibration machine, hopper scale, discharging electric vibration machine and three tension measuring modules. The batching process is as follows: firstly, the material is supplied to the weighing hopper through the loading vibrator, and at the same time, the on-line metering of the material is carried out until it reaches a certain value, and then the loading process is stopped. However, the discharging metering is carried out. That is, the material is continuously discharged to the screw conveyor through the vibrator. In the process of discharging, the computer samples and calculates the discharging amount according to a certain sampling period, and when the given discharging amount is reached the discharging process stops and a dosing process is completed.
The change of the material in the weighing hopper is sent to the computer through the load cell through AD conversion and computer processing for display, and based on this, the loading and unloading electric vibration machine is controlled. The accuracy of the dosage control mainly depends on the performance of the weighing module, transmitter, vibrator and controller as well as the control algorithm. This dosage control only on the material changes in the cumulative amount of material changes, and the flow of material changes in the requirements are not high, as long as the electric vibration machine and the controller's output capacity to meet the requirements and more stable on the control accuracy will not have a worthwhile consideration of the impact of the weighing module and transmitter is to affect the accuracy of the key factors, the selection of high-precision and high stability of the weighing module, and the use of multiple Weighing modules (choose 3 weighing modules can be) parallel combination of ways. ) Parallel combination mode. Circuit should also use advanced integrated circuit amplifier, in order to achieve ideal measurement results.