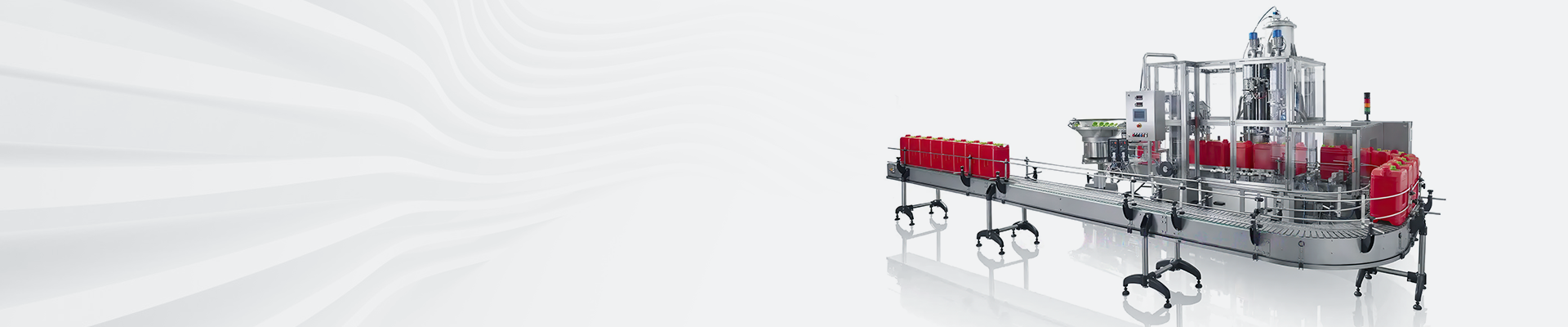
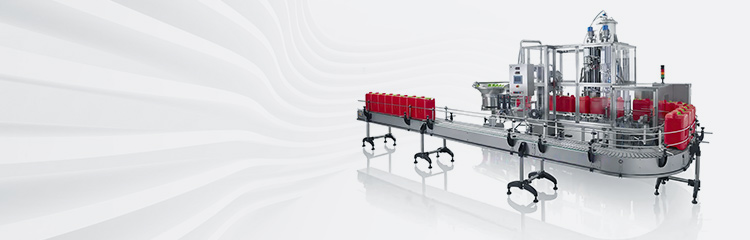

Summary:The weighing and batching system adopts fully enclosed automatic material distribution and polymer material feeding control, and requires the realization of multiple feeding methods such as centralized feeding, step-by-step feeding and formula feeding.
Polymer materials, also known as polymer materials, are materials made up of polymer compounds as a base with other additives (additives). This paper takes polyacrylate PVC impact modifier ACR as an example to describe the application of DCS in polymerization reaction control.
ACR polymer processing aids are the main modifiers in PVC production, used to improve the processing properties of soft and hard PVC. Reduce the melt weight of PVC, shorten the melt time, improve production efficiency, and obtain high quality PVC products with uniform structure and glossy surface.
ACR is an acrylate copolymer, which belongs to "core-shell" structure copolymer. Its preparation is based on various types of acrylic esters, as well as crosslinking agents, emulsifiers, initiators, molecular weight adjusters and other raw materials, through a number of emulsion polymerization and the production of white fine non-toxic, non-corrosive powder.
The appropriate amount of water, emulsifier and part of the ACR monomer, acrylic ester formulated into an emulsion; add initiator, regulator, so that the monomer polymerization, to maintain the polymerization of weighing higher than the initiation of the weighing of 5 ~ 10 ℃, the reaction and holding time of 1.5 ~ 2h; through a certain way, in the above emulsion to add the rest of the monomer, the interval of a certain period of time, supplemented by the initiator, and continue to react for 2 ~ 3h, to control the weighing of not more than 70 ~ 80 ℃; the polymerized emulsion is cooled and filtered; the emulsion is spray dried into powder, automatically weighed and packed.
The main production equipment includes material distribution/loading system, reactor weighing, initiator and other additives system, mixing kettle, spray dryer, condenser and common system, etc. The technical key of this product mainly lies in the process formulation and process control.
Second, process control difficulties
ACR product specifications, each specification of the formula consists of more than a dozen kinds of material parameters and dozens of adjustable parameters, so the batch formulation system is very complex. Requirements for the dosage system has a flexible design, able to adapt to a variety of product process changes. The entire production unit consists of a number of independent systems, in the batch production process, the batch master program to the independent system resources and equipment to coordinate, and in accordance with the order of the implementation of the unit process;
The weighing and feeding system adopts the fully enclosed automatic dispensing and polymer material feeding control, which is required to realize a variety of feeding methods such as centralized feeding, step-by-step feeding and formula feeding, etc., and the accuracy of the feeding is required to be extremely high;
Polymerization kettle reaction process is lengthy, roughly divided into three stages: emulsion particle generation stage, uniform polymerization stage and speed reduction stage, containing a total of 28 steps. Weighing control is through the adjustment of the half-pipe jacket and the size of the inner cold pipe water flow to stabilize the control kettle weighing changes, weighing curve is complex, each stage of the weighing control requirements for accurate, timely response, cooling time to achieve uniform cooling.
Third, the control program ~ automatic batching system
Weighing and feeding system batch production process is characterized by the use of the same set of production equipment, the production of a number of varieties of products, which is very common in chemical plants, pharmaceutical factories, food and beverage factories. As society's demand for multi-species, small batch production continues to increase, as well as the requirements for traceability and quality assurance of product production, the importance of batch production mixing is becoming more and more prominent. Batch production systems can be very flexible in assigning a unique identifier to each batch of product, through which the unique identifier realizes the traceability of each batch of product produced in the factory and meets the requirements of quality assurance.
An automated batching recipe consists of the operational processes and steps of the equipment's resources, detailing how each batch was produced.
A batch dosage requires a variety of functions and interfaces, for example, the batch dosage needs to communicate with the control equipment, it needs to provide a screen interface for the production operator to monitor the batch production process, a recipe generator for the process engineer, and a database to record the complete information of the production process for later analysis.
In view of the extremely complex production process described above, ACR introduced the S88-compliant UWinBatch software as a batch control and automation solution.
The Recipe Management screen is where you can add the required product recipes and involves four main operations:
Creating a batch, which is used to make decisions about major production activities, such as the production of an ACR product of a certain specification. A batch is the highest level in the process control structure, and it is used by unit processes and/or operations and/or stages to accomplish its tasks;
Completing the definition of a unit unit, a unit unit process is used to define a group of related operations that occur within a unit of plant, e.g. a polymerization reactor is a unit process. It is common for a process to have multiple unit processes executing simultaneously within their respective units;
Add operation, operation is a step in the production program, by clicking on the interface "+" can be added steps, such as feeding, material control, temperature, heat preservation, drainage, to be reversed, etc. are some common operating steps;
Add a stage, a group of organized stages to form a step, the same can be added by clicking on the interface in the "+" stage, stage is a sub-processing tasks. The result of the execution of a stage may be commands for basic control, commands for other stages and/or data sets, such as manual, waiting, scripts, devices, jumps etc;
IV. Weighing Control Program
The most critical quality indicator of a polymer product is the degree of polymerization, which is independent of the initiator dosage and conversion rate, but highly dependent on polymerization weighing. Weighing performance is stable, chain initiation is fast, polymerization centers are many, chain transfer is fast, chain termination is also fast, thus the reaction speed is accelerated. However, the generated polymer has small molecular weight, small degree of polymerization and poor quality. Therefore, the weighing of the polymerization reaction must be strictly controlled in order to obtain products with uniform molecular weight distribution. Generally, the polymerization kettle weighing fluctuation is required to be ≤±(0.2~0.5)℃.
We will polymerization reaction weighing is divided into four stages, the first stage is warming up, the polymerization kettle material weighing up to the process requirements of the reaction weighing control point, the key point of this stage is to the fastest speed to the requirements of the reaction weighing to reduce the polymerization degree of dispersion; the second stage is the transition, the jacket of hot water quickly replaced by circulating water, in preparation for the absorption of polymerization reaction exothermic, the key point of this process is to How to seize the inflection point weighing, close the steam valve, to prevent the reaction lag caused by weighing fluctuations, to achieve a smooth transition of warming and heat absorption and polymerization exothermic; the third stage is a constant temperature reaction, the requirements of a smooth transfer of polymerization process of the release of the reaction heat, to ensure that the polymerization of the weighing of the control accuracy, but the polymerization of the heat released is uneven, how to adaptive control is the key to the problem. The fourth stage is the end of the reaction, when the conversion rate will reach 80%~85%, due to the lack of monomer, the reaction rate decreases rapidly, adding terminator to terminate the reaction. How to achieve the highest conversion rate while ensuring the shortest reaction time is also the key to the problem.
4.1 Heating stage
Through the jacket steam heating to warm up the polymerization kettle material weighing up to the process requirements of the reaction weighing, the key is when to close the steam valve. If the closure is too early, jacket weighing down too fast, will inevitably lead to kettle temperature drop too fast, resulting in kettle materials can not trigger polymerization reaction, reaction time is extended, resulting in the "second heating" or "stewing pot" phenomenon; on the contrary, it will cause jacket weighing down too slowly, kettle temperature rises too high, exceeding the set value. The opposite will cause the jacket weight to fall too slowly, the kettle temperature rises too high, more than the set weight, resulting in fluctuations in the reaction weight. Both will affect the product quality. For this problem, we adopt the rule control method to solve it. When the difference between the set weighing and the weighing in the kettle is greater than N℃ (N>0), we adopt the method of closing the cold water regulating valve and fully opening the steam valve. When the kettle temperature is less than or equal to N℃ from the temperature rise setting, the rate of change of the kettle weighing is fuzzified, and each of them is divided into three states, namely, high (increased), medium (normal) and low (low). According to the fuzzified rate of change, the corresponding steam valve opening degree can be obtained, so as to get the data of the relevant control parameters.
4.2 Transition phase
At this stage, the material in the kettle has just started to trigger the polymerization reaction, the polymerization reaction is still very unstable at this time, the reaction exothermic heat is also relatively small, and the exothermic heat is not uniform, when the excess heat is replaced by the circulating water regulating valve, there are two situations that may occur:
(1) add too much cold water, replace too many people, resulting in the kettle temperature can not reach the set reaction weight, resulting in "under-adjustment" or "smothering" phenomenon, prolonging the reaction time, such as Figure 6, shown in curve C;
(2) Cold water is added too little, jacket weighing high, can not inhibit the kettle weighing trend, resulting in "overshoot" phenomenon, resulting in insulation section of the kettle weighing fluctuations are too large, need to be adjusted over a long period of time, such as Figure 7, shown in curve A;
The above two situations will directly affect the polymerization kettle production efficiency and product quality, in order to polymerization kettle weighing rate control within a certain range, quickly and smoothly cut into the insulation stage, the transition of the optimal control algorithm to regulate the opening of the circulating water valve, the formula is as follows:
MV=(t1,t2,t3,x1,x2)
Where: MV ~ jacket weighing regulator output;
t1 ~ the measured value of jacket weighing;
t2 ~ set value of jacket weighing at the end of transition process (can be modified by the operator);
t3~measured value of circulating water weighing at the end of warming up;
x1 ~ cold water balance coefficient (can be modified by the operator);
x2 ~ kettle and valve-related prediction parameters (pre-made in the program, the operator can not be modified)
Through the above means to control the polymerization kettle weighing, can be very good to avoid the occurrence of the two aforementioned undesirable phenomena, is the polymerization reaction is carried out smoothly, and minimize the transition time, optimize the production of his, improve efficiency.
4.3 Constant reaction stage
After the weighing in the kettle reaches the set weight of polymerization, it is the constant temperature reaction stage until the material is discharged. This stage requires smooth transfer of polymerization reaction process released reaction heat, the kettle weighing stability in the set weighing near the required fluctuations of less than ± (0.2 ~ 0.5) ℃, the use of logic prediction cascade control strategy, structurally similar to the conventional cascade adjustment system, cascade stage by stage control, to the kettle temperature as the main parameter, jacket water weighing as a sub-parameter of the cascade control, the use of kettle weight as the main ring, jacket weight as a sub-ring The kettle weighing is the main loop, and jacket weighing is the secondary loop.
4.4 Reaction end stage
When the reaction ends, the kettle pressure drops to a certain set value, then press the "end of reaction" button, and the state of each valve, kettle temperature and jacket weighing regulator is restored to the initial state through the smooth control program.
V. Operation effect
Weighing and batching system in the project since the commissioning of the production operation shows that the formula management makes the whole production process simple and easy to carry out, improve the production efficiency by 30%, and realize the full automation control, reduce human error, improve product quality. And the weighing of the polymerization kettle has been controlled by various control schemes such as rule control, single-loop-serial switching control, logic prediction serial control, and follower control, and satisfactory results have been achieved, such as the weighing fluctuation of the constant inversion stage is controlled at ±0.2℃, the heating speed is fast, and the smooth transition between heating up and heat absorption and exothermic polymerization is achieved.