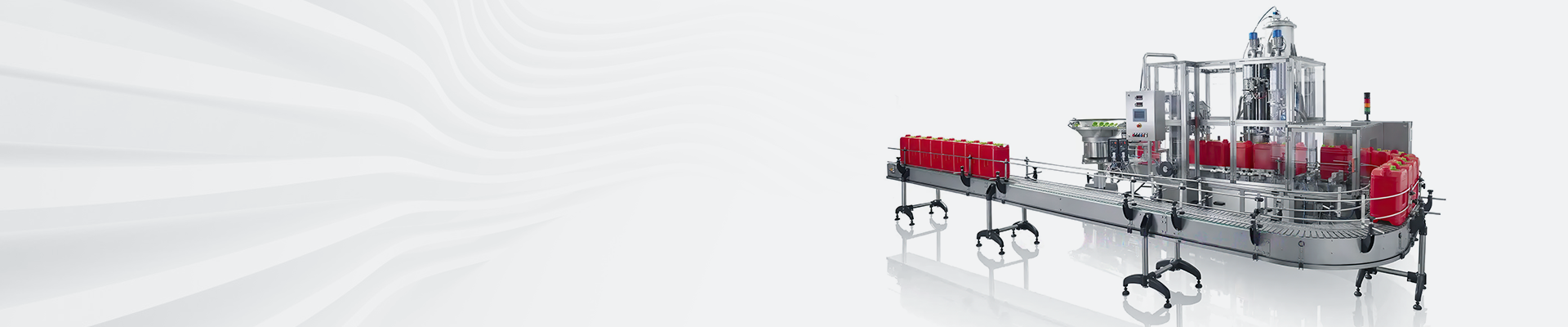
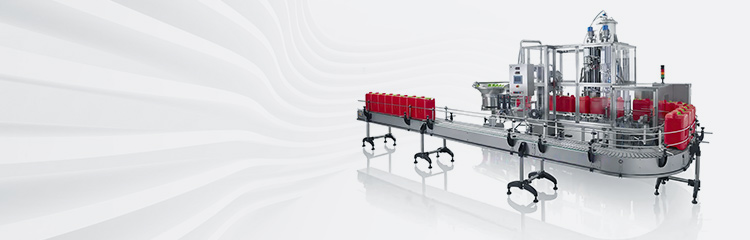

Summary:The automatic batching control system can realize online dynamic weighing in the production process. By implementing dynamic weighing, the accuracy and reliability of the system can be improved, and complex function support can be provided for the system.The system has been debugged and now put into use, effectively improving the batching accuracy and production efficiency.
1.1 System Composition
The system has 5 raw material tanks, 1 weighing tank and 1 mixing tank, when working by the motor driven pump to the weighing tank sequentially injected into the different raw material tanks of liquid material, the target weight of the material set by the touch screen, each raw material weighed and injected into the mixing tank when the 5 kinds of raw materials are all injected into the mixing tank after the mixing to complete the entire process. The automatic weighing and batching control system is composed of PLC, weighing instrument, touch screen and frequency converter, PLC model is OMRONCP1H-X40DR-A, weighing instrument is Toledo IND236 weighing instrument, touch screen is OMRONNP5-MQOO0, frequency converter is OMRON3G3MV, the batching control system uses PLC as the master station, IND236 weighing instrument as the master station, and OMRON3G3MV as the inverter. IND236 weighing instrument as a slave station, can connect more than one IND236 weighing instrument as a slave station, this design only use one IND236 as a slave station can meet the production needs, such as the need for more slave station need to add PLC expansion module [control structure as shown in Figure 1.
1.2 Communication Setting
In the weighing control system, RS232 serial communication is used for data exchange between PLC and IND236 weighing instrument, PLC and touch screen. The OMRON PLC used in the system comes with two communication ports. The CP1W-CIFO1 option board is used to configure COM1 and COM2 as RS232C serial communication ports, which are connected to IND236 weighing instrument and touch screen respectively.
IND236 weighing instrument supports one standard serial port and one optional serial port, which are COM1 (standard serial port on the motherboard) and COM2 (optional serial port.) COM1 is the default communication port of IND236 instrument, which adopts RS232 communication method. COM1 is the default communication port of IND236 instrument, which adopts RS232 communication mode, and COM1 is selected as the communication port, and COM1 is set as the continuous output mode for PLC real-time data processing.
The continuous output mode of IND236 can continuously send weight data and weighing status information to the remote device PLC.
The serial communication parameters include port number, baud rate, data bit, stop bit and parity bit; port number is set to COM1 and COM1 is set to continuous output mode, baud rate is 9600, data bit is 8, stop bit is 1, parity bit is 0 and other parameters are defaulted. after adding the communication option board to the PLC, the PLC is programmed with OMRON PLC programming software CX-P to set the communication parameters, baud rate 9600, data bit is 8, stop bit is 1, parity bit is 0 and other parameters are defaulted. Parameter settings, baud rate 9600, format 8, 1, N, mode RS-232C, start code set 0X0002, end code receive byte 18, communication parameters and weighing instrument communication parameters are consistent.
1.3 Control strategy
During the material feeding process, the impact on the weighing tank will affect the weighing accuracy and stability, in order to coordinate the weighing accuracy and weighing speed, the three-stage speed feeding method is adopted. Five kinds of raw materials feed in turn, using a frequency converter to control five motors, PLC through the different combinations of output switching quantities to control the frequency converter for frequency control, to achieve fast feeding, slow feeding and fine feeding. At the beginning of weighing fast feeding, when the fast feeding prediction value WW1 is reached, the slow feeding starts; when the slow feeding prediction value W2 is reached, the fine feeding starts; when the total weight of feeding reaches the "target weight - pipeline material weight a permissible error" when the feeding stops, in which the pipeline material weight is the residual material in the pipeline that will continue to flow into the weighing machine when the motor stops rotating. W1 and W2 are the percentage of the target weight, the optimum value is taken from the actual test, and the target weight and allowable error are set by the touch screen.
Programming
2.1 PLC main program
The system is equipped with two working modes, manual and automatic, and the working mode is switched by the conversion switch of the control panel. Manual mode, press the corresponding feed button, when the material reaches the target value set by the touch screen, stop feeding and wait for the next material feeding instructions; automatic mode, when the first material reaches the target value into the mixing tank and then into the next material, and so on until the last cycle of material. Both manual and automatic modes need to set the target value of materials and other related parameters on the touch screen, the touch screen interface includes monitoring interface, parameter setting interface and alarm interface.
2.2 Communication subroutine
The core part of the control system program is the communication subroutine, whether the communication program design is reasonable or not directly affects whether the system can operate normally and the accuracy of the dosage, the following is the design of the communication subroutine and the communication interruption phenomenon to do a brief discussion.
Automatic dosage system weighing instrumentation is set to continuous output mode, PLC real-time reading of weight data and determine whether the data is valid, after the system starts, PLC special auxiliary relay area serial port 1 and then start the flag A526.01 set serial port start delay reset, the serial port began to receive weighing data; received data is stored in the buffer area of the PLC, when the reception of the 18 set up, the serial port 1 receives the data, the serial port 1 receives the data. After receiving the set 18 bytes, the serial port 1 end-of-reception flag A392.14 is set, and the data in the buffer is read by the PLC's serial port receiving instruction RXD and stored in the corresponding storage area. The weighing instrument sends ASCII code weight information, and the PLC needs to convert the data after reading.
In the dynamic weighing communication process, communication interruption occurs easily, which is mainly caused by data overflow. When the end of data reception flag A392.14 is ON, RXD instruction quickly read out the received data, if so continue to receive data, when more than the capacity of the buffer, the serial port for the overflow error state, to stop receiving action, then need to restart the serial port to clear the buffer data to resume communication.
3 Conclusion
The designed automatic weighing and batching control system for liquid materials has been put into use, making the batching accuracy and production efficiency has been greatly improved to meet the requirements of the production process and improve the maintainability of the equipment.