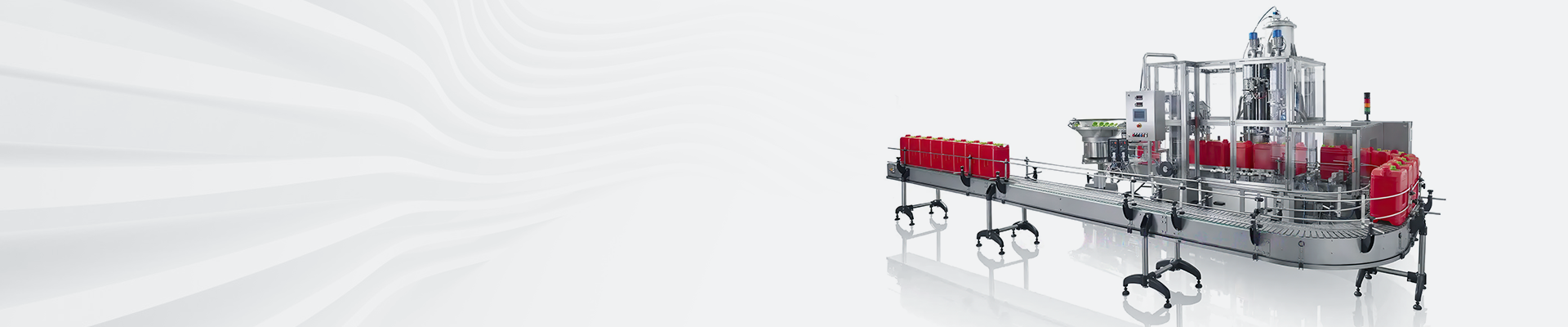
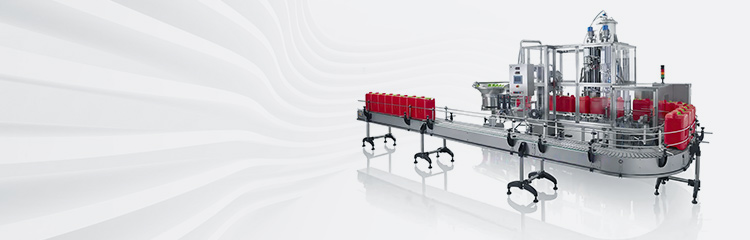

Summary:On the formula management page of the weighing and batching system, you can see the product formula information of all pesticide production lines for emulsifiable concentrates, water\microemulsions, microcapsules, suspensions, powders, and granules.
The weighing and batching system adopts full redundancy design (power supply redundancy, network redundancy, control redundancy, IO redundancy, operation redundancy), and the control station adopts the latest high-performance CPU, real-time data memory, redundant SNet drive unit and redundant CNet drive unit and other functional modules, which are composed of powerful data computing and processing ability and standard industrial hardware quality to ensure that it is able to realize various complicated control strategies at high speed and stably in the industrial field. Various kinds of complex control strategies. The analog volume adopts single-point card, which supports point-to-point isolation, point-to-point power distribution and point-to-point online replacement of modules. Not only is it highly reliable, but also easy to maintain. In addition, it is also equipped with Modbus communication module, which is responsible for realizing seamless connection with other third-party equipments in the whole plant.
Recipe Station
The mixing system formula operation station provides the functions of formula management, production task management, batch report and so on.
1 Recipe Management
The formula management page of the weighing and feeding system can see the formula information of all pesticide production lines for emulsifiable oil, water, microemulsion, microcapsules, suspensions, powders and granules, and can create, modify and delete the formula of a certain product. The product formulation information includes the product type (emulsion, microcapsules, etc.), the equipment unit (oil phase kettle, water phase kettle, etc.) through which the product needs to be produced, and the production process parameters (temperature, time, weight, etc.) of the equipment unit.
When creating a new recipe, select the product type, and the weighing and dosing system will automatically call out the recipe template for the product type. The recipe template can be pre-configured or maintained by the user's process engineer.
Take microencapsulation product A as an example, the recipe information of product A is as follows:
If Product A does not need to add encapsulant in the oil phase kettle, just do not fill in the "amount of encapsulant added" or delete this item.
In view of the confidentiality of the recipe, only process engineers with recipe management rights can do the recipe management function (rights can be configured).
2 production task management
Automatic dosage system in the formula operator station to create a new production task, select the product formula, the planned amount of finished product production and the planned execution time, weighing and dosage system will produce a production task plan. When creating the task, the weighing and dosing system can calculate the required package materials according to the predefined information.
By clicking on the details, you can see the ratio of the various raw materials in the production recipe. Process engineers with recipe management rights can also see the production process parameters of the production recipe. The created production task can be modified and deleted.
30 minutes before the scheduled execution time (configurable), the weighing and dosage will indicate that a production plan needs to be executed, and the production manager can check the production readiness. The production manager can check the production readiness. After the production manager confirms, the production task will change its status to "Waiting for execution".
The production operator can click on the "Start" button to start the execution of the production task. After the task is executed, the batch number is generated automatically (the batch number generation rule is configurable), and a production task can contain several production batches. At this point, the production task status:
Production batch status:
It is also possible to create batches manually under the task, the batch number is generated automatically by weighing and dosage.
During batch execution, the sequence control logic configured in the control station is executed step by step, prompting the operator to operate step by step in accordance with the operating procedures. For example, the control logic for microencapsulation product A is as follows:
Each step of the logic can include control sub-logic. The material preparation sub-logic is as follows:
The oil phase kettle sub-logic is as follows:
Each step within the oil phase kettle sub-logic can be broken down into finer sub-logic.
The process parameter variables in the control logic come from the recipe information. If a process parameter is missing from the recipe information, the weighing and dosing will skip this logic and move on to the next step.
The quality department can enter the results of the tests performed on each batch and during the production process into the weighing and dosage system. By selecting a task or batch, you can view the event logs, operation logs, alarm logs and product quality data of the task or batch.
The production manager can select the search conditions to filter the production tasks, find out the production tasks that match the search conditions, print the production task reports, such as daily, weekly, monthly and yearly production task reports, and the batch information included in the task can also be printed out. Production managers can search for a specified product batch and find information about the production process of the traced batch.
3 Batch Report
Batch reports can be customized to meet customer process requirements.
The weighing and loading system can also be customized with various production management reports. For example, daily, weekly, monthly, quarterly, annual report of a certain product; daily, weekly, monthly, quarterly, annual report of a certain raw material consumption; daily, weekly, monthly, quarterly, annual report of water and electricity consumption.
Implementation of batch control logic on the DCS dosing platform
1 Unit equipment modeling
The main batching equipment has a corresponding control model on the DCS batching platform.
Figure9 Oil phase kettle equipment unit
On the DCS dosage platform, a corresponding control model is created, which includes the control logic within the unit equipment, such as pump start/stop, valve switch, pressure control loop, temperature control loop, and chain logic, etc. In addition, this model has its own event method. In addition, this model has its own event methods, such as xylene feeding, diaphragm pump feeding, silo feeding, oil phase kettle heating, mixing, discharging and so on.
2 Production Line Control Flow
The production of a batch of products will be from a source equipment unit through a series of equipment units to the final packaging of the finished product equipment unit. Because these equipment units in the DCS feeding system have a control model, so as long as the production of products through the equipment unit connected to the production of this batch of products in the production line control model has been established. Supplemented by the parameters of the production formula, DCS will automatically complete a series of equipment unit control, product production of the entire chain in the weighing and dosage of help in an orderly manner.