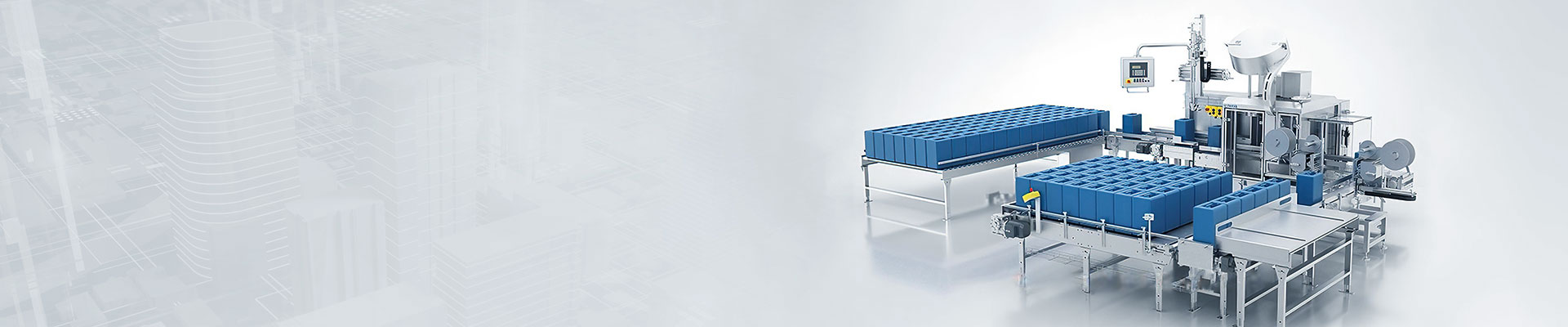
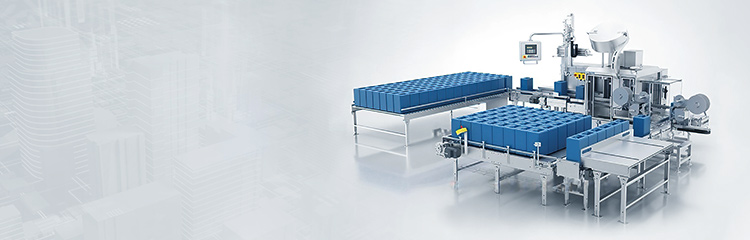
Pneumatic dosage scale utilizes PLC output and weighing instrument to control the motor frequency, and controls the on-site motor frequency converter through three ways of ratio giving, flow rate giving and frequency giving at PLC output. When the operator selects the proportioning giving on the operation screen, he only needs to input the total flow rate of the dosage and the proportioning ratio of each sub-scale, then the amount of material to be discharged from each scale can be calculated automatically and the tracking adjustment can be carried out according to this discharging amount. The flow rate of each scale is controlled through the flow rate setting area on the screen, which is required for the PID parameterization of each scale.

Automatic dosage scale is a new generation of reaction pot control system based on years of experience in developing control system and the affirmation of many customers. The reaction pot is characterized by simple control, applicable functions, high dosage accuracy and long trouble-free time, etc. The signals of each Electronic scale are amplified on the spot and then adjusted to the flow rate. The signal of each electronic scale is sent to A/D acquisition card for A/D conversion after on-site amplification, and then the processed data will be sent to the display to show the weight of materials, and the reaction pot will be dosed according to the dosing value given by the computer during automatic dosing, and the computer will automatically start the material feeding and conveying system according to the control parameter set by the user after the dosing and dosing of the materials are all completed, and then put each material into the mixer for mixing, and at the same time, the dosing time will be changed. The computer will automatically start the material feeding and conveying system according to the control parameters set by the user, and put the materials into the mixer for mixing, meanwhile, the batching data will be stored into the database for the management system. If the control computer can not start, the system can also display the scale value of each electronic scale, which is convenient for users to batch manually.
The dosage scale utilizes PLC output and weighing instrument to control the motor frequency. The PLC output controls the on-site motor frequency converter in three ways, namely, rationing, flow rate and frequency. When the operator selects the proportioning giving on the operation screen, he only needs to input the total flow rate of the dosage and the proportioning ratio of each sub-scale, then the amount of material to be discharged from each scale can be calculated automatically and the tracking adjustment can be carried out according to this discharging amount. The flow rate of each scale is controlled through the flow rate setting area on the screen, which is required for the PID parameter adjustment of each scale.
Main performance characteristics:
It has manual, semi-automatic and full-automatic dosage function, and all the weighing adopts electronic scale.
Adopting high-grade industrial computer and high-precision data acquisition card, with high reliability.
It has two kinds of batching methods: drop control and precision control.
The feeding order of each material can be set flexibly.
The control parameters can be adjusted online.
It has the function of operation authority management.
The formula can be set to be input and modified by the relevant personnel through this machine or LAN.
With bill printing function.
With network management interface function.
The management system adopts standard database, which is favorable for customers to install ERP management information system later.
Functions are perfect and practical.
Users can carry out secondary development of the operation database according to their own needs.
It has the function of secondary measurement or monitoring of feeding.
The control parameters are completely open, which is favorable to the flexible control of the mixing plant.