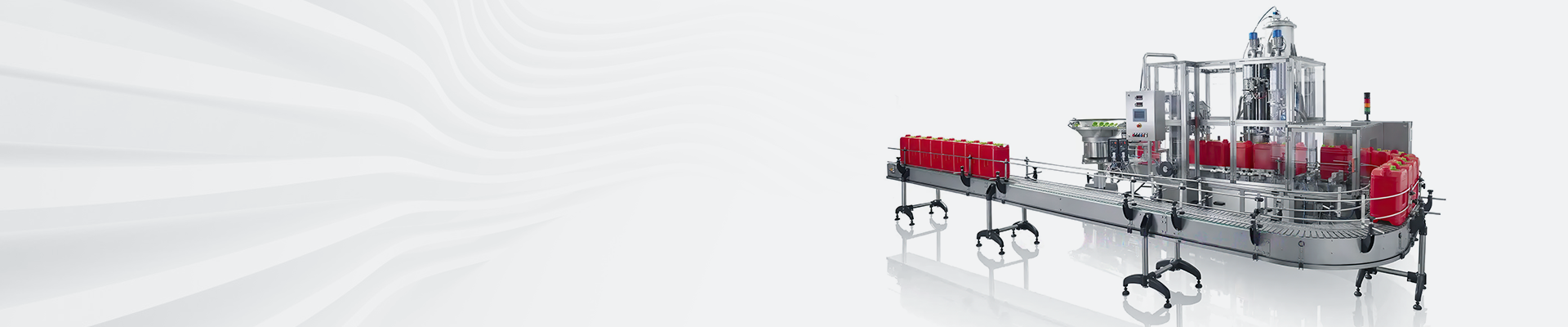
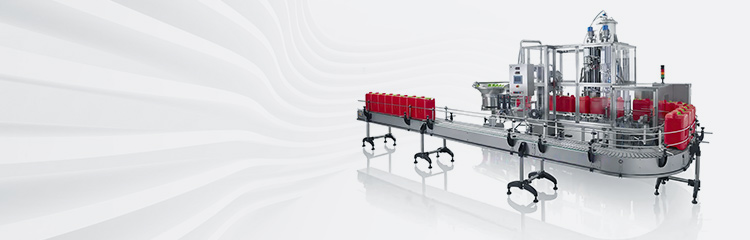

Summary:In the process of monitoring the weighing control system, based on the support of KingView and VB for dynamic data exchange technology, VB's MSComm communication control is used to solve the serial communication between the weighing control system and the computer to achieve real-time monitoring of the ingredient weighing process. .Through on-site implementation, the system reduces errors and improves work efficiency and the management level of the enterprise.
In a variety of batching and weighing industrial processes, for the traditional weighing monitoring system, the analog signal is susceptible to interference in the transmission process, which is easy to cause data reading errors, and manual data recording is also prone to errors, and it is also inconvenient to view the historical data. In view of the above problems, this paper designs a set of monitoring system and proposes a new method of communication between feeding system and Configuration King, which solves the problem that the two cannot communicate directly. Nowadays, the popular industrial control system is generally composed of the upper and lower computer, in this paper, the upper computer adopts PC, in this project, it is necessary to set up good communication with the weighing control system, dosing equipment, industrial control software and other equipment to realize convenient and efficient monitoring.
1 weighing monitoring system
1.1 Batching weighing process
In this paper, from a fiber plant dosage control hand, in the entire production process, five kinds of raw materials is the key to put, these five kinds of raw materials to be cast in a certain proportion of the production process, each weighing tanks are equipped with a dosage system, through the weighing control system to read the quality of the parameters, and then the quality of the parameters are transmitted to the monitoring room, the operator through the display device to read the weight of the dosage in the tank. First of all, when feeding to the weighing tank, open the feeding valve, the operator should record the time and weight of each feeding, when the raw materials in the five weighing tanks reach the standard ratio, close the feeding valve, open the discharge pump, discharge operation, discharge should also be discharged according to a certain ratio, discharge is completed, close the discharge pump, the end of an operation. Then, the proportion of laboratory tests, if there is an error between the test results and the standard test value, but also to adjust the proportion. According to the different needs of the raw material ratio, the operator of each discharge and feeding operation should be adjusted to ensure the smooth progress of production.
1.2 Configuration software
At present, the use of configuration software as industrial control software phenomenon is very common, the application of configuration not only realizes the convenience of accurate data recording and real-time view of historical data, but also in the alarm, monitoring and control to improve the efficiency of the enterprise, the user's welcome. In this paper, the monitoring interface using the Beijing Asian control company launched the Configuration King 6.53, the software in the historical database, historical trend curve, reports, etc. There are many features, the design of the monitoring system interface is friendly, easy to grasp.
1.3 Monitoring system
According to the above batching and weighing process, this paper designs a set of real-time monitorable configuration control system. The weight of raw materials in the five weighing tanks can be seen directly from the monitoring screen, the operator can input the ratio value in the system, the feeding valve operation, and so on to reach the input ratio, the discharging pump will be automatically opened, the feeding valve will be automatically closed, after the end of the discharging, the discharging pump will be automatically closed. It can also be operated manually as needed. Configuration King realizes the control of valves and pumps by connecting with PCL724 board through DO card. The system can automatically calculate the standard assay value and assay result, which is convenient for the operator to control the feeding and discharging. It can also view the historical data in real time, and the system will backup the historical data regularly for easy viewing in the future.
2 Communication link
2.1 Configuration King and VB support for DDE Configuration King supports Dynamic Data Exchange (DDE), and other applications that support Dynamic Data Exchange to easily exchange data through DDE, engineers can use the PC's rich software resources to expand the "Configuration King" functions, you can use the VisualBasic development service program to complete the data acquisition, report printing, multimedia sound and light alarms and other functions, so that it is easy to form a complete management system on the machine. Since the configuration king can not directly communicate with the weighing system, based on the configuration king and VB support for DDE, this paper adopts VB to develop application programs to realize the communication between the configuration king and the electronic weighing system.
2.2 MSComm communication control of VB
VisualBasic is a visualization of the window development environment, VisualBasic applications developed in a very large number, which is widely used in educational software, computer software and a variety of control systems [3] VisualBasic is not only easy to learn, and can be designed for the system built-in and plug-in controls is more numerous, and Microsoft will be in the Microsoft has designed a very useful control in VisualBasic, i.e., the MSComm communication control, which allows us to complete the design of serial communication. There are two types of serial communication, one is RS-232 serial communication and the other is RS-485 serial communication!] . RS-232 serial communication has been used for a long time in system control applications and is quite an important interface. We can see it in PLCs and also on the 0 interface of instruments. In the paper, we use M
3 communication program preparation
To realize the computer and electronic weighbridge serial communication, you must develop an application program through which to achieve dynamic data exchange between the two, the development of serial communication applications can be carried out according to the following three steps: set the communication control CommPort, Settings, PortOpen and other attributes of the establishment of the communication link: establish a link to the use of the communication control 0ut-put, Input and other attributes of the data exchange; after the end of the data exchange set PortOpen to False, close the serial port. After the link is established, use the properties of the communication control 0ut-put, Input, etc. to exchange data; after the data exchange is finished, set PortOpen to False to close the serial port.
3.1 Initialization Settings
The following is an example of a raw material (MA), the initialization of the communication port settings, the other four raw materials in addition to the communication port needs to be different, the other settings are the same. Select the 2nd communication port for the control MSCommMA corresponding to MA. Transmission is performed at a rate of 2400 bits per second, and even parity bit checking is performed. Each data cell is 7 bits and the stop bit is 1 bit. The status of the communication connection port is then returned.
3.2 DDE interface design for weighing system
To select VB as the server to deliver data to the configuration king, it is necessary to set the value of attribute LinkMode on the communication window to 1. Since string data are read in the weighbridge, in order to make it easy for the operator to observe the data, it is necessary to convert the received data into numerical data in VB to be sent to the configuration king. the VB and the weighing control system are linked through RS-232 serial ports, and since the raw materials are of five kinds, and the Since there are five kinds of raw materials, and there are only two serial ports in general PC, it is necessary to add RS-232 expansion card to expand the ports. When designing the DDE interface of the weighing control system, six communication ports are set up to receive data, and the received data is displayed in a text box. In this interface, there is an area for displaying the weight of the ingredients, an area for displaying the data of the weighing control system, an area for the operation of the buttons and an area for the selection of the communication ports. Clicking on the corresponding button realizes the corresponding operation of the dosage.
3.3 Program flow
After the dynamic link is established between the configuration king, VB and the dosage control system, after checking that the communication is normal, VB receives the data from the dosage system, then converts the string data in VB, and then sends the converted numerical data to the configuration king through DDE.
4 Conclusion
In this paper, the dosage control system monitoring system is designed to solve the communication problem and data processing between the upper computer and the feeding system. In the practical application, the combination of configuration king and VB application program through dynamic data exchange realizes the data communication between VB and configuration king, and obtains very good application effect, which makes the formula management easier to operate and manage, and the system has been successfully applied in the production.