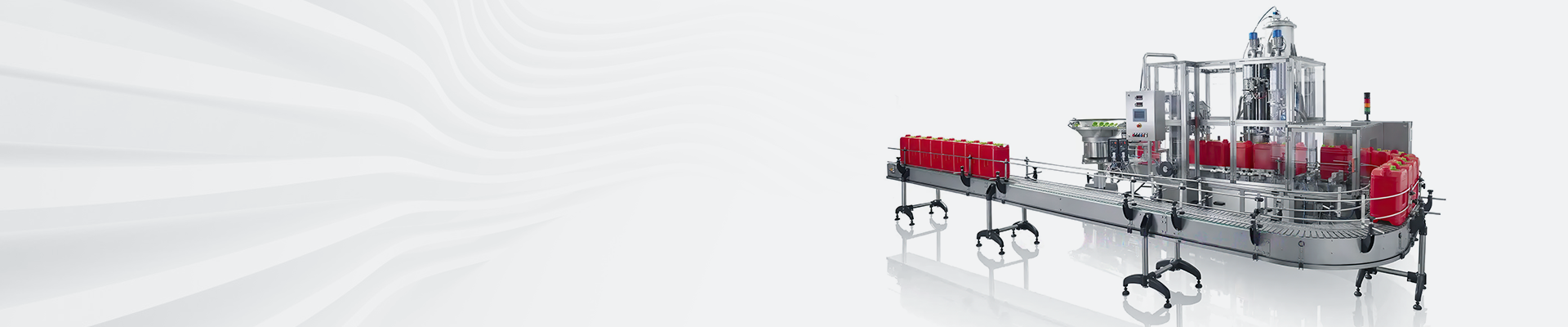
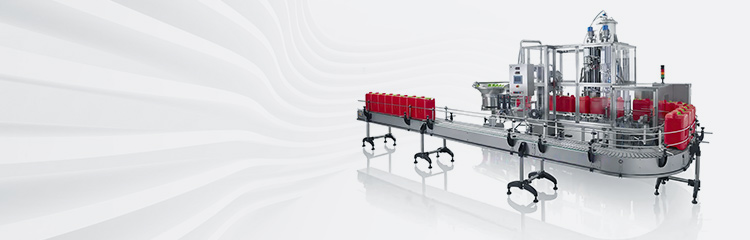

Summary:The batching system calculates the feeding amounts (given values) of various materials based on the production plan and recipe proportions.And it is handed over to the lower PC for batching control. The PLC calculates the action time of the pneumatic valve according to the given value. When the pneumatic valve operates for a certain time and the material is close to the given value, it will make slight and small-scale adjustments to make the scale weigh in. The material is infinitely close to the given value to the allowable error range, and the feed pneumatic valve is closed.In this way, the added amounts of the three materials mixed each time can be accurately measured.
1 Overview
With the deepening of China's reform and opening up, people's living standards and self-care awareness is increasing, people's diet is no longer simply "fill your stomach", but how to scientific diet, in order to achieve the purpose of fitness and disease prevention, the human body needs trace elements to add an important topic, and salt is the best trace elements to add the best Salt is one of the best carriers of trace elements. In order to meet the market demand, a lot of salt industry, on the basis of the traditional salt production process, the human body daily essential such as zinc, selenium, calcium, potassium, iron, magnesium, riboflavin and other nutrients scientifically and reasonably into the edible iodized salt to produce a wide variety of salt products to meet people's needs. Such as: fortified nutritional salt, balanced nutritional salt, low-sodium salt, flavored salt and so on. These varieties of salt are more and more favored by people, thus bringing a new revolution in the production and use of salt. However, the addition of trace elements is very small (general content are mg/kg), such a small amount of addition to the measurement and dosage system puts forward a new topic, for this reason, combined with my company's many years of experience in the development and promotion of measuring scales and dosage systems, our company put forward for the nutritive salt dosage system of "static weighing, dynamic production "We know that the precision and stability of static weighing is much higher than that of dynamic weighing, which provides the possibility of high-precision and high-stability addition of trace elements, and at the same time, under the premise of guaranteeing uniformity of mixing, by adjusting the control parameters, the subsequent production process after mixing is continuous and stable. To summarize, the nutritive salt so produced should be a high-quality qualified product with precise trace element content and uniform mixing.
2 Process analysis
Nutritional salt ingredients in order to ensure the continuity of production, the choice of two sets of mixing systems. Only run 1 # mixing system and any two packaging machines; when the nutritional salt production program more, then run 1 #, 2 # mixing system and a whole packaging line (5 packaging machines). Salt raw materials from the packaging of the third floor 2 # warehouse, before mixing, according to the production plan by the system automatically (or manually) to determine the number of input mixing system and the addition of three materials, when the last material mixing is almost over, in advance of the three kinds of materials into the weighing body in static weighing and waiting for the mixing machine, once the material out of the mixing machine, the three kinds of materials will be weighed immediately in the weighing body to add to the mixing machine to start a new round of mixing, and so on repeatedly to perform In order to ensure the accuracy of measurement, mixing uniformity, and mixing uniform nutritive salt is sent to the hopper, and then packaging, as long as the hopper to ensure that there are always materials to ensure the continuous production of nutritive salt.
3 control basic principle
Balanced nutritional salt automatic dosage system includes two sets of independent quantitative dosage mixing system and a packaging line. And each set of mixing system contains a mixer, three sets of measurement control equipment.
3.1 Measuring and weighing control principle
According to the site-specific conditions, the metering control system is operated by PLC as the host, and the calibration work is done by the upper computer, which calculates the dosage amount (given value) of various materials according to the production plan and formula ratio. And handed over to the lower PC dosage control, PLC according to the given value, respectively, calculated the pneumatic valve action time, when the pneumatic valve action to a certain time and the material has been close to the given value, and then a small range of micro-adjustment, so that the material in the weighing body is infinitely close to the given value of the permissible range of error, the closing of the feed pneumatic valve. In this way, the three materials can be weighed accurately each time the amount of material added to the mix.
The mixer mainly consists of a fixed frame, a mass acquisition module, a signal conditioning module, a storage module, a serial communication module, a processor, a power supply module and an LCD display. The quality acquisition module includes weighing module and angle weighing module. The weighing module is mounted on the fixed frame of the weighing test bench and the angle module is mounted on the tail shaft of the discharge material.
When the angle module detects that the rotation angle of the tail shaft is greater than 10°, the processor starts to collect data, the weighing module collects the force of gravity perpendicular to the surface of the weighing platform, and stops collecting data when the cumulative amount of collected data is greater than 1000. The output signal of the weighing module is amplified and converted by the signal conditioning module, and then the mass of the reactor is calculated and processed by the processor, and the calculation result is sent to the storage module and shown on the LCD display.
3.2 Mixer control principle
When the mixing material is added, the mixer will act immediately, and the total amount of material added for each mixing and the mixing time should be determined according to the amount of material in the hopper and the minimum time required to ensure uniform mixing, in order to avoid the phenomenon of material breakage in the packaging production line.
3.3 Upper management computer control principle
The upper computer real-time monitoring of the production line in a variety of parameters, a variety of parameters exceeding the standard alarm, production reports to print, and save at least one month of real-time data for production management and analysis, at the same time, but also with the PLC to participate in the management of the measurement of the weighing.
4 control system structure
According to the automatic dosage control system design principles and balanced nutrient salt dosage mixing system control of the actual needs of the entire control system is divided into the field implementation layer, control layer, management level of three-level structure. Field implementation layer is mainly composed of detection instrumentation and actuators, including: weight detection, material level detection; control layer consists of programmable controllers (PLC); management layer consists of industrial control machine and the upper configuration software (configuration king).
The upper computer completes the man-machine interface, parameter adjustment, data management, alarm processing, report printing and other functions.
The lower PLC completes the dosage quantitative control, mixer mixing control work, out of the human material control and hopper material level detection.
The mixer completes the material mixing work.
High-precision weighing module and weighing transmitter complete material weight collection.
Material level meter completes the material level detection in the hopper.
Pneumatic control valve to complete the material control.
5 software design
Feeding system software is divided into the upper computer management software and the lower PLC monitoring software two parts. In order to realize the tasks and functions proposed by the monitoring and management system, and reasonably and efficiently use the hardware and software resources of the control system, the monitoring and management system is reasonably designed.
5.1 Management System
The control management system is mainly composed of the following screens:
System general view: the process flow is made into a diagram, indicating the direction of each material of the system, while the values of various physical quantities are displayed in real time at each detection point;
Operation panel: the whole screen is composed by the control circuit as a unit, providing the interface for modifying the set value of the main control parameters of the control circuit and real-time display;
Debugging window: Provides modification of control parameters of the control loop and observation of the operation effect;
Real-time trend graph: it can be automatically rolled up to quickly reflect the changes of variables over time;
Historical trend graph: complete the historical data of each important parameter of the system;
data query; Alarm window: record and alarm the abnormal situation of each important parameter;
Gang group window: introduce the whole control system and explain the operation method in detail;
Report window: provide statistics and printing function for the important material parameters of the system in terms of shift, day, year and as a unit, providing basic data for management.
5.2 Lower control system lower
PLC software to complete the management and control of measuring scale, mixing control, material level detection function.
6 Conclusion
The control system has the following characteristics:
1)The system adopts the three-layer control system structure of execution layer, control layer and management layer, which is in line with the principle of centralized management and decentralized control of the centralized control system, and provides a good and open platform for the enterprise to realize automation, informatization, and auxiliary decision-making.
2) Provide friendly man-machine interface to make the operation simple and accurate. The system is designed from the design idea of advanced, economic, practical, good and durable, each part of the system is demonstrated, the products selected and the technology adopted are proven to be feasible, from local to overall, to ensure that the control system is reasonable and economical. According to the modern latest automation technology specifications and requirements, the control system program is comprehensively and carefully designed to realize the balanced nutrient salt production process with a high degree of intelligence and automation. From the actual control and management needs, the control system provides as flexible and convenient functions as possible.