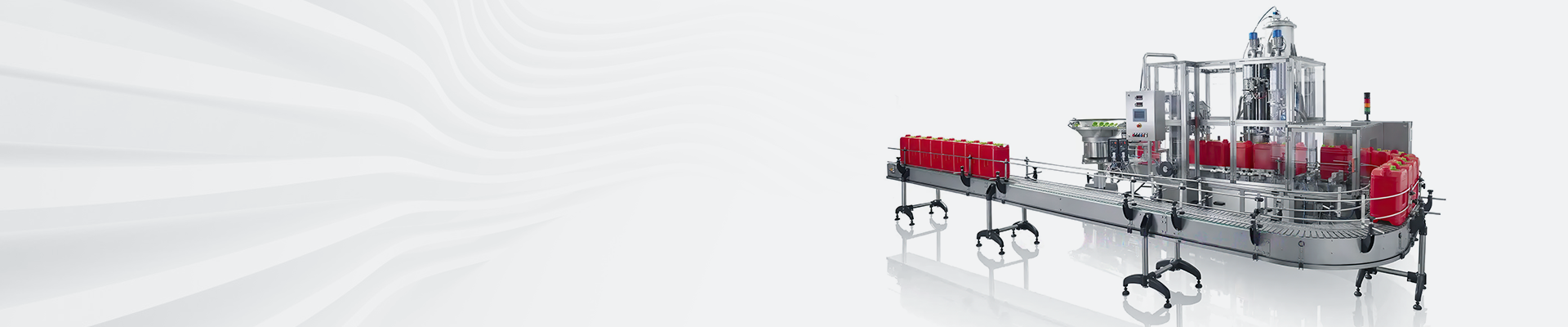
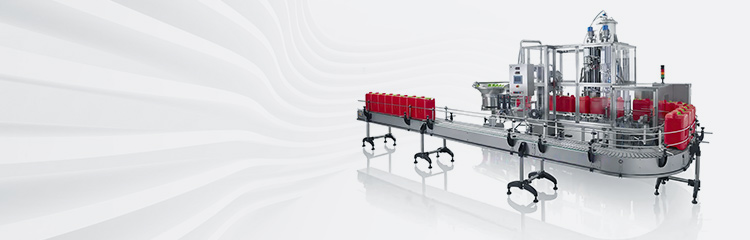

Summary:The bulk cargo measurement system uses nuclear radiation technology, microcomputer control technology and digital signal processing technology to conduct non-contact dynamic measurement of materials. It uses computers to intelligently control bulk cargo measurement and designs scientific and reasonable mathematical design and processing algorithms to improve measurement and control accuracy. The article also analyzes several key elements to improve measurement accuracy, and uses coal in dry bulk cargo as an example to perform dynamic measurement, with good results. The system has the advantages of high dynamic measurement accuracy, good stability, and strong anti-interference ability.
In the past, bulk terminals often used two kinds of measurement means for dry bulk cargo operation: one is water ruler, the other is electronic scale; the former is affected by wind, waves, hydrology and other factors, the accuracy can not be guaranteed; the latter uses weighing module, the structure is complex and difficult to adjust, easy to deformation, difficult to adapt to the harsh environment of dry bulk cargo operation in bulk terminals, and there are more safety and economic problems The bulk terminals often have a large amount of dry bulk cargo operation hourly, which can be as high as hundreds or even thousands of tons. Hundreds or even thousands of tons, easy to cause too much loading, so that the ship is overloaded, which may cause serious shipwrecks, capsize accidents; if the loading is too little, but also increase the cost of transportation Therefore, the accurate measurement of the bulk terminal dry bulk cargo operations is very important.
1 System structure
For the bulk terminal dry bulk operation of the site environment is extremely poor, the development of bulk terminal material measurement and control system of the microcomputer nuclear scale system consists of weighing body part and the host part of the composition.
2 Measuring Principle
To dry bulk coal as an example of nuclear scales made using the principle of material attenuation of rays, radioactive sources and rays, in the weighing of the plane composed of the body bracket was fan-shaped irradiation, the material from the weighing of the body bracket through the middle of the radioactive sources and rays, a part of the attenuation of coal, the rest of the part of the penetration of the coal, irradiated to the ray detector and ray detector, so the size of the ray detector output signal, which can be reflected in the material on the conveyor. Therefore, the size of the output signal of the radiation detector can reflect the amount of material on the conveyor.
The output signal of the weighing module is proportional to the intensity of the rays and is the output signal when there is material. Through the calibration to determine the value, you can get the conveyor material load, the flow of the conveyor can be calculated from the cumulative amount of material.
3 Measurement and control of the software design
The dosage system using weighing instruments as the main control equipment unified realization of the measurement and control functions, which control part of the control using control with a high degree of intelligence, the sensor includes two kinds of sensors, respectively, weighing sensor and speed sensor, weighing sensor is the ionization chamber, which will be measured substances and rays are converted into a certain impulse signals speed sensor for real-time speed detection of the belt conveyor, the input and output signal Adjustment part of the signal for the necessary filtering, shaping, amplification, level conversion and other processing weighing controller through an empirical knowledge base to control the operation of the entire system, do not need to establish a complex mathematical design, can be well adapted to the nonlinear.
1) instantaneous flow formula program design using nuclear scales and microcomputers composed of multi-way mineral material dosage control system, should strive for real-time and accuracy of the flow formula program design, should minimize the amount of the program to improve the implementation of the feeding system speed in the instantaneous flow formula program design using the known parameters according to the determined range of changes in the establishment of the data table method, the feeding system work will be the collected signals according to the Digital volume from the EPROM data storage device to find out the corresponding data, after a simple calculation to get the flow result value.
2) instantaneous flow of units and calibration coefficients of the final results can be provided to the user through the microcomputer with the display or printer, commonly used flow unit is kg and t right, the program design needs to be through the coefficient operation into a practical flow unit.
Nucleus belt scale is a non-standard mineral material flow sensor, the mineral material measurement should be calibrated before the flow of the upper limit value, first of all by the standard scale weighing load mass, and then the standard load mass applied to the nucleus belt scale, according to the micro-computer display of the numerical value of the situation, through the setting of the flow of the calibration coefficient in the formula to complete the calibration coefficient of the value can be set through the keyboard to modify the numerical keys.
3) the cumulative flow of the program design cumulative flow processing program is part of the entire flow program, the program design mainly consider the cumulative accuracy of the cumulative flow and the cumulative results of the unit, in the design of the program according to the results of the unit requirements of kilograms, tons, kilotons of units in order to meet the accuracy and display printing requirements.
4 system's main errors and improvements
4.1 The optimal load factor of the nuclear scale
The measurement error of the nuclear scale consists of two parts, namely, the error caused by the material load and the error caused by the speed; the error of the nuclear scale is mainly composed of the shape of the material, the mass attenuation coefficient, the sensitivity of the ionization chamber, as well as the error of the speed sensor. Realize high-precision material measurement, must be established on the basis of high-precision speed measurement and high-precision load measurement, for speed measurement to choose high-precision speed measurement tools. In order to improve the measurement accuracy of the nucleus scale, the load factor must be limited, too large and too small will lead to a sharp increase in the measurement error, so the nucleus scale operation is best run at the best load.
Changes in the composition of the material has a certain impact on the measurement results of the system, but if the material composition changes are large, it is also necessary to re-calibrate the system or load constant re-correction In addition, the shape of the material on the performance of the nuclear scale also has a great impact However, in the field calibration of nuclear scales, if the selection of the calibration of the measurement section is reasonable, which contains a variety of material distribution shapes that may occur, then the error caused by the shape of the section can be effectively eliminated to achieve the required measurement accuracy. Can be effectively eliminated, to achieve the required measurement accuracy of course, in the feed addition of material shaping device, you can get a more stable material shape, which is also an effective means to solve the cross-section error.
5 Conclusion
The system extends the application field of nuclear technology for bulk terminal dry bulk cargo operations provide an effective means of measurement and monitoring of the system in a port put into practice, running performance is good, stable so that enterprise developers will focus on writing business logic, greatly simplifying the development of e-commerce system plays an important role in the.