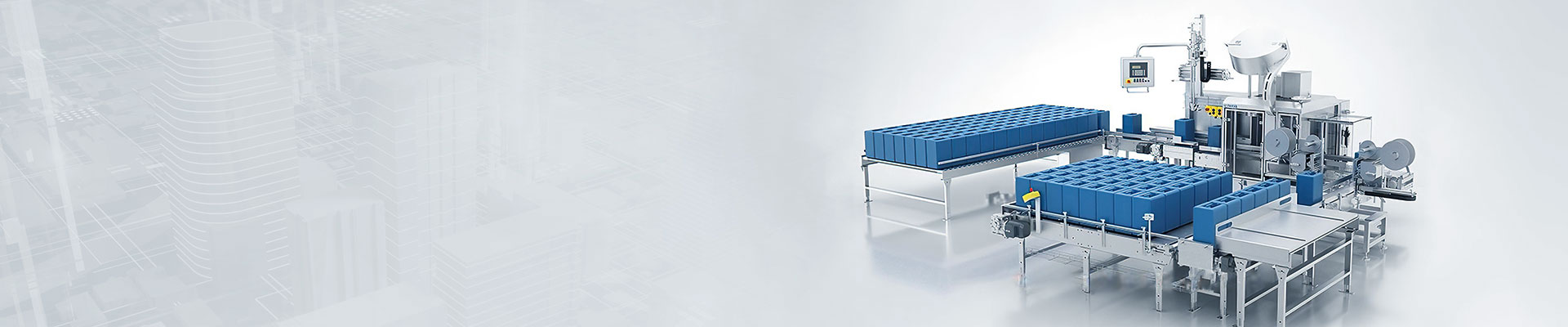
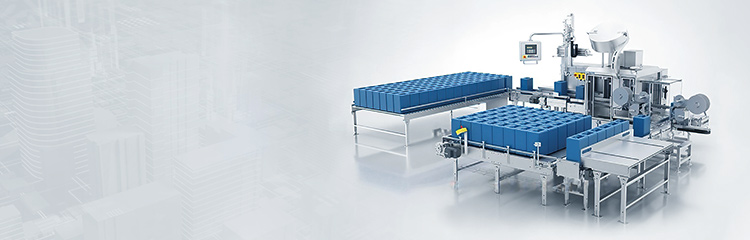
Automatic Belt Scale is an example of a belt scale with a fully suspended weigh frame formed by the support of four load cells, which are divided into four independent signals into the field digital converter. The belt is used for continuous feeding during the feeding process and the feeder delivers the material from the user's silo or other feeder and weighs it through the weigh bridge.

Automatic belt scales for the quantitative feeding of bulk materials. The belt is used for continuous feeding during the feeding process, the Feeder transports the material from the user's silo or other feeding equipment and detects the weight by means of a weighing bridge, while the speed sensor mounted on the tail pulley detects the speed of the belt. The measured weight and speed signals are sent to the accumulator for differential processing and display the instantaneous flow in tons per hour for comparison, and according to the size of the deviation from the output of the corresponding signal value (PID signal), through the frequency converter to change the speed of the motor to change the amount of feed to make sure that it is with a certain set value, so as to complete the control of the constant feed flow. From the weighing principle can be seen, the size of the instantaneous flow of the material measured by the electronic belt scale depends on two parameters, that is, the instantaneous flow is equal to the load value of the material on the loader measured by the load cell and the speed sensor measured by the speed value of the belt v (m/s) two parameters multiplied by the speed sensor measurement accuracy and stability and the measurement of the accuracy and stability of the load cell is equally important. At present, the accuracy of the load cell is generally increased to a few ten thousandths, while the accuracy of the speed sensor is mostly in a few thousandths, so improving the accuracy of the speed sensor is one of the effective ways to improve the accuracy of the electronic belt scale system.
In the field operation box press the start button relay at the same time, the frequency converter start signal closure, at this time the feeder and the motor fan began to run, running indicator light (dosage scale failure when this light flashes), through the field speed knob so that the frequency converter output current changes and the field motor speed also changes, found in the process of running deviation should be stopped by pressing the stop button to stop the belt to adjust, but also can be adjusted by the power on. The center control can be turned on generally speaking, the changeover switch can be played to the center control position, the panel of the ready light must be on, or on behalf of the center control can not be turned on or the light is damaged. Instrumentation to detect the function of each signal, such as faults will be found at any time on the display, when the fault disappears, the fault display must be reset to enable the instrument to lift the fault. Common failures of the instrument are: load cell failure, speed sensor failure, division error, etc. If the instrument appears to be dead (which is a rare phenomenon, but sometimes inevitable), the instrument will be cold-started, so that all the data is restored to the factory settings, the instrument needs to be reset and calibrated before normal use.
Belt scale system requires only a small amount of maintenance, can be achieved within a few weeks of satisfactory use, both the first calibration of the new installation, but also a simple zero calibration and interval calibration, can be realized in the belt scale calibration, put into use.
1)Regular cleaning, in order to prevent the scale volume of ash accumulation, resulting in weighing inaccuracy.
2)Regularly check the movable part of the belt scale, whether there are materials or foreign objects stuck. Specific inspection locations are: the center of the roller and conveyor frame, scale frame and scale beam.
3)If the belt runs off, adjust it regularly to prevent the measurement from being inaccurate.
4)Do not have external impact scales and sensors, maintenance personnel are strictly prohibited from overhauling the belt scale standing or operating other equipment.
5)Do not overhaul the equipment in the scale body welding, gas cutting and other operations.
6)Signal cable laying or use do not cross with the power cable arrangement to prevent interference.
7)The instrument should be reliably grounded and have independent power supply.
8)Ensure the weighing rollers and the rollers in the weighing domain are running freely, otherwise replace them.
9)The speed measuring roller should be cleaned regularly to prevent the material from sticking.
10)The bearing seat of the speed measuring roller should be lubricated regularly.
11)Regularly check the top wire at the shaft sleeve of the speed sensor to prevent it from loosening or falling off.