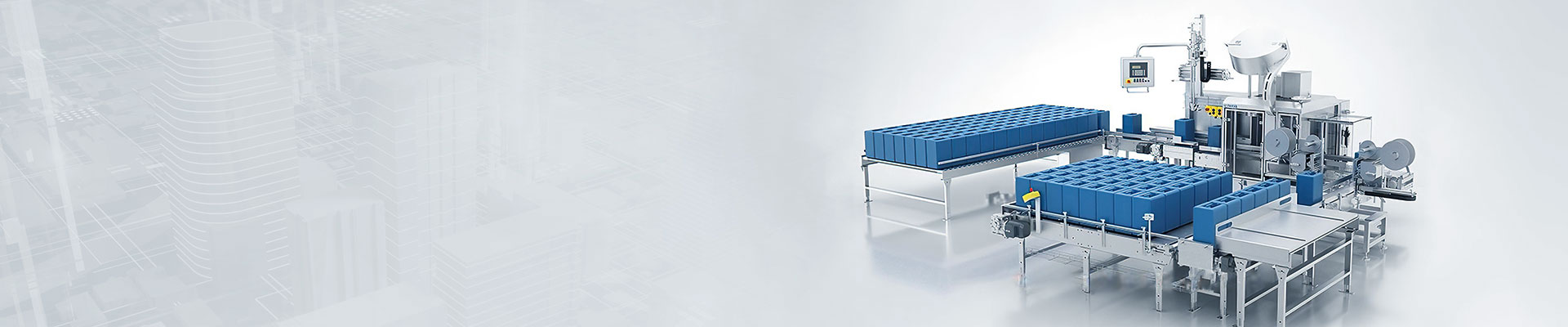
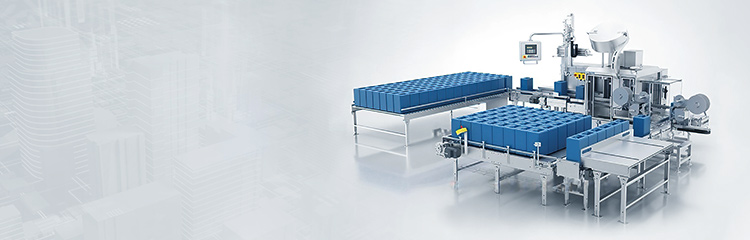
Weighing conveyor will pass through the material on the belt, through the weighing scale frame under the load cell to detect the weight, the feeding controller will be the flow and set the flow rate for comparison, the output signal from the controller to control the frequency converter speed regulation, to achieve the requirements of quantitative feeding. It is an automatic scale that continuously weighs the bulk material on the conveyor belt without the need to subdivide the mass or interrupt the movement of the conveyor belt.

Weighing Conveyor can be operated in a variety of control modes, such as continuous operation, beat-to-beat operation and variable speed operation, etc. It is mainly composed of conveyor belt, frame, belt roller, tensioning device, transmission device and tensioning device. Among them, the Weighing system device in the weighing conveyor is specialized in material weighing and design, the material after multiple processed by the weighing system device for its material weighing and packaging into finished products, this device is also an indispensable device for belt conveyor equipment.
Weighing system device in the process of installation, must be the scale of tension and tension changes in the smallest place, preferably installed in the tail of the weighing conveyor, weighing rollers should be installed from the point of loading not less than nine meters, from the tail of the guide rails shall not be less than five roller spacing, in order to reduce the contact with the belt to contact with the guide rails (or in the guide rails in the material) of the impact.
In order to obtain the highest accuracy of the weighing system, weighing conveyors with a length of more than 12 meters should have a gravity tensioning device to ensure a constant tension on the conveyor belt. For high accuracy requirements, it is recommended to use special weighing rollers to ensure that the radial runout of the rollers is minimized, provided that they have the same dimensions and slot angles as the original rollers of the weighing conveyor. When the scale is installed, all the rollers should be adjusted to a straight line in the weighing section to minimize the additional force introduced into the weighing system due to changes in belt tension or other external forces when the belt is running over the rollers. The weighing rollers and the three sets of rollers before and after the installation should be calibrated dimensionally, while the scale body should be adjusted up and down with shims so that the scale body will not be affected by the change of belt tension. The weighing rollers and the three sets of rollers before and after the weighing rollers should be calibrated very accurately in order to make the weighing platform or section as smooth as possible, so as to ensure that the ideal change of the belt groove shape will be obtained in all kinds of belt loading conditions.