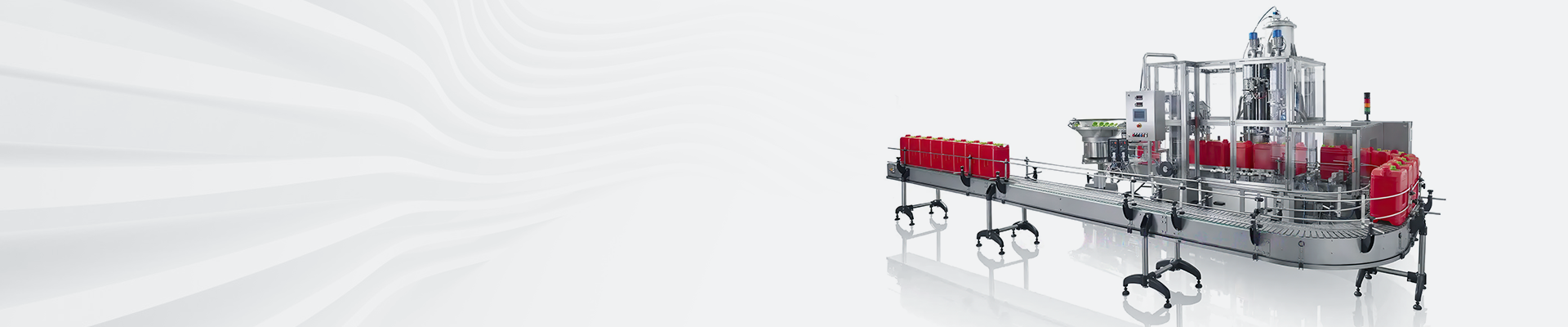
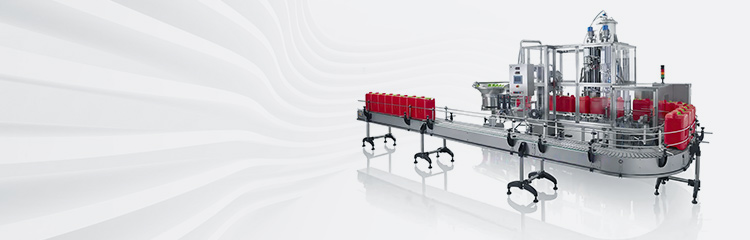

Summary:The weighing sorting machine is a device that realizes high-speed, high-precision weight detection and automatic sorting of overweight or overweight products under online dynamic conditions to meet users' needs for net weight detection in packaging.
Precision fittings are the basic units that make up the various parts of precision fittings. With the development of China's economy and the gradual increase in the level of national income, precision fittings have become more and more people's transportation tools. And precision fittings spare parts industry also with the growth of demand for precision fittings in China has been prosperous and development. High-quality precision fittings spare parts products can not only help precision fittings spare parts enterprises to reduce production costs, and more importantly, to ensure the quality of precision fittings products.
Precision fittings spare parts forging product weighing relationship. Generally speaking, precision fittings are composed of 15 parts such as body, trunk, engine, front axle, rear axle, frame, transmission, drive shaft, steering system and so on. With the development of China's precision fittings industry, the assembly of precision fittings required to use the parts continue to increase, the matching precision fittings spare parts forgings requirements are also increasingly high. Forging is a metal material through the forging process and get the workpiece or blank. Precision parts forgings are characterized by complex shape, light weight, poor working conditions, high safety requirements. For example, precision parts engine crankshaft, connecting rod, camshaft, front axle beams, steering knuckles, rear axle half shafts, half shaft casing, transmission gears in the bridge box, etc., is not a precision parts about the safe operation of the key forgings. If weighed, 17-19% of the components on the precision parts will use forgings. During the production of forgings, each piece is required to be consistent and free of any porosity, excess space, inclusions or other imperfections. Components produced by this method need to achieve a high ratio between strength and weight for consistent safety performance.
According to current international standards, the weighing tolerance of brake pads generally needs to be controlled within 3g. For manufacturers of precision parts and components, in addition to ensuring production efficiency, the quality of parts and components is also very concerned about the quality of the product, because the quality of precision parts and components is the first condition to ensure the safe operation of precision parts and components.
The defects of manual weighing and testing due to the high demand for precision parts and accessories forging products (i.e., each piece of forging products are required to be consistent, and need to achieve a certain weighing ratio), in the production process, the production company generally through the weighing of the product weighing and testing, to eliminate substandard products. In the past, the weighing and testing of precision parts and components was carried out in the form of manual testing, i.e., after the cutting and processing process, the finished products were manually weighed by the operators, and then the parts were categorized according to the weighing standards. Because of the complete reliance on manual operation, it is easy to cause deviation and inaccuracy in the process of weighing and sorting, and also lower efficiency, the direct result is to increase the manufacturing cost, and the quality of the finished car also has a certain safety risk.
After the design improvement, the weighing inspection machine has been developed from the original simple weight inspection to the sorting according to the weight, and the level of sorting has been developed from the first level in the field of weight rejection and weight sorting to more than 20 levels at present. Commonly used in accessories, hardware, electronics and other fields of weight and size sorting.
Sorting scale is the equipment to realize high-speed and high-precision weight detection and automatic sorting of overweight or overweight products under online dynamic conditions. To provide a comprehensive and perfect weighing solution. The special high-speed and high-precision data acquisition board is combined with touch screen, which can ensure the high-speed characteristics of data acquisition and processing, and also can fully combine the flexibility and convenience of PLC system in operation, providing customers with more close to the production needs and more humanized solutions.
Checkweigher can be more than one weighing and sorting machine communication, combination of use, to achieve more than one weighing and sorting machine on-line work, to meet the needs of users for the net weight detection of packages; - more than 10 types of grading and sorting by weight - intuitive graphical interface display, easy to operate for the user - a wealth of data statistics, easy for the user to find out the problems in the process - attentive data analysis to facilitate the user to improve the packaging, filling Process automatic weight sorting machine scope of application of this product is suitable for large weight, large volume of the weight of the goods detection, especially for the whole box of goods missing detection; such as: lack of bottles, lack of boxes, lack of a, lack of bags lack of cans and so on.
Checkweigher has gradually become an indispensable link in modern industrial production, especially in the production process of food and pharmaceutical industries. Weighing and sorting machine completes the measurement of product weight in the process of product conveying, and compares the measured weight with the pre-set range, and sends out the instruction from the controller to reject the unqualified products or send the products with different weight ranges to the designated area.
Weighing and sorting machine usually consists of conveyor belt, controller, inlet and outlet conveyor. Among them, the weighing conveyor completes the collection of weight signals and sends the weight signals to the controller for processing. The in-feed conveyor is used to ensure adequate spacing between products by increasing speed. The outfeed conveyor is used to transport the finished products out of the weighing area.
Measuring and sorting machine report function: built-in report statistics, the report can generate EXCEL format; can automatically generate a variety of real-time data reports, the individual weight of each discharge port and the total weight statistics, at any time to grasp the production situation.
U disk can store more than 1 piece of statistical data;
Interface function: reserved standard interface, data convenient management, can communicate and network with PC and other intelligent devices;
Realize centralized control: it can realize the centralized control of one computer/human-machine interface to multiple checkweighers;
Parameter recovery function: provide factory parameter setting recovery function.