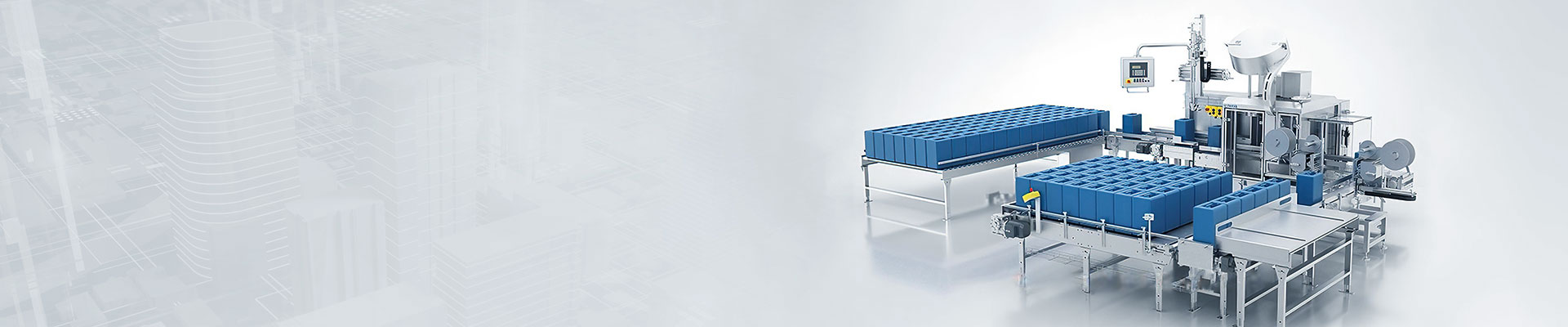
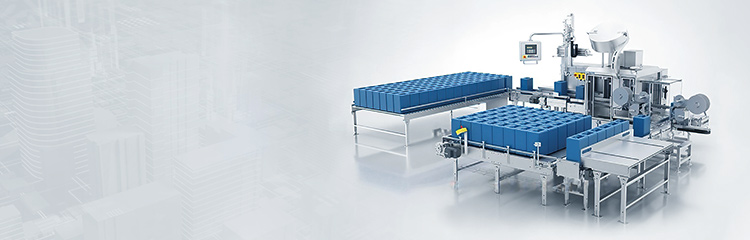
A checkweigher is a belt conveyor with a weighing platform that is itself a small, independent conveyor, and is known to weigh items at the moment they pass through the conveyor. With three-in-one motorized pulley (i.e. motor, reducer and pulley integrated), the weighing characteristic conforms to the normal distribution curve, the same product measured many times will have different values which will be distributed in the intervals of this normal distribution curve, and the upper and lower limits of the rejection are set to be smaller than the upper and lower limit intervals of the user's request for rejection. It consists of a conveyor and a weighing device. There are various types of conveyors such as belt, chain or roller. The size of the conveyor depends on the size of the object to be weighed.

The automatic sorting scale tracks the objects on the pressure-free control chain, collects the information of image processing, carries out summary analysis, gives the results to the objects, and removes the unqualified products when the objects reach the eliminator. Using the world's advanced digital weighing unit, to achieve high-speed, stable measurement. Patent scale frame structure, to ensure that the dynamic working period to maintain accurate, stable LCD touch screen operating system, English and Chinese operation interface, easy to learn; Powerful data statistics function, record the detection data of each shift; The use of dump conveyor belt, easy maintenance. It is mainly used for automatic weight detection, up and down line discrimination or weight classification selection on various automatic packaging lines, through the weighing sensor, amplification circuit, AD conversion circuit, MCU circuit, display circuit, keyboard circuit, communication interface circuit, voltage regulator power circuit and other circuits.
When the object is placed on the pan, pressure is applied to the sensor, which deformates, resulting in a change in impedance, and a change in the excitation voltage is used to output a changing analog signal. The signal is amplified by an amplifier circuit and output to an AD converter. Converted into a digital signal for easy processing output to the CPU operation control. The CPU outputs this result to the display according to keyboard commands and programs. Until this result is displayed. Products through the weighing test, qualified returned to the original conveyor belt, unqualified to be eliminated (or alarm stop), and according to the setting of the product classification and statistics, automatically provide feedback signals to adjust the correction of the feeding equipment, text display fault alarm information, a variety of graphical statistical display functions.
The object running on the chain first triggers the front side wall photoelectric, and uses A structure array A to record its current encoder value, and the good or bad information of the front wall sorting. Material port photoelectric trigger record the value of the current encoder, and then subtract the value of the current encoder from the pulse distance between the material port photoelectric and the front wall photoelectric REMOVE1, and then find the value of the encoder in the front and side wall structure array in a tolerance range △ (that is, REMOVE1±△ range) to find the good or bad information of the material's record of the front and side wall sorting. Copy to the structure array of the material port, and record the good or bad information of the material port sorting. If this material is not found in the front sidewall structure array, the bottle is considered to be an excess material, possibly sliding too much or artificially inserted material, and the bottle is recorded as unqualified. In the same way, the material bottom photoelectric trigger is used to check the structural array of the material port, the rear wall photoelectric trigger is used to check the structural array of the material bottom, and the rear wall structural array is checked when the photoelectric trigger is removed. The structure array with photoelectric rejection collects the current photoelectric trigger encoder value and all the information of front wall, material port, material bottom and rear wall sorting. By monitoring the current encoder value and the information in the cull structure array, decide whether to allow the cull action to cull the material.
Technical parameter
Sorting range: 400~36kg
Sorting accuracy: 20g
Sorting speed: Max.30 times/min
Minimum display: 10g separator (width 200~650mm) (length 150~1130mm, height 150~1130mm)
Power supply: AC110/220V, 50/60HZ
Operating temperature: 20℃~50℃