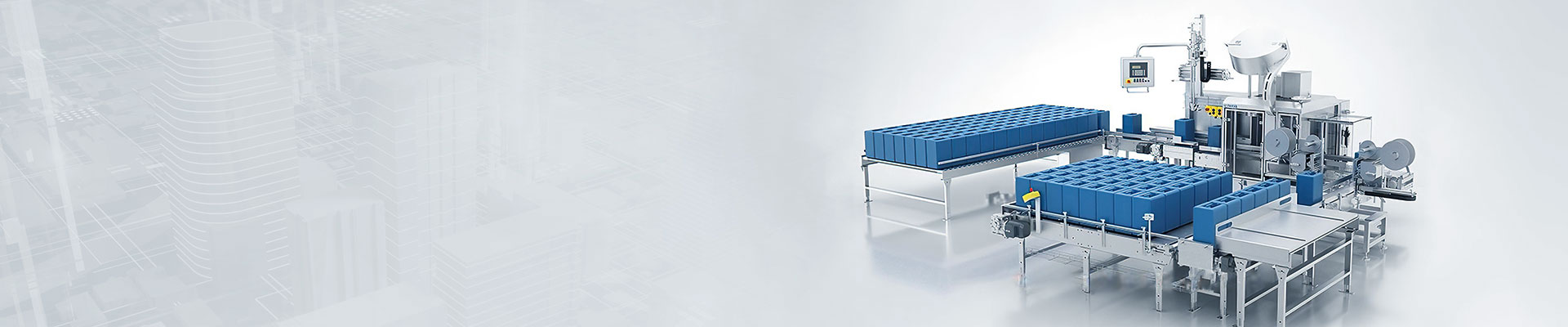
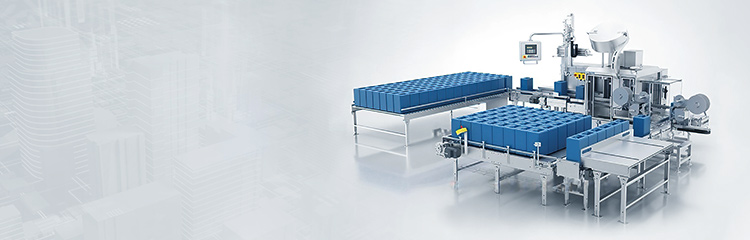
The mixing and dosing machine sets up the interface to display the instantaneous weight, the material level, the use status and the dosage sequence of the various materials. Complete the production record of batching process, including the pre-matching report of each shift, recording the weight, time and pot number of each material scale, and the post-matching report recording the amount of genuine and inferior products produced in each shift, the total amount of genuine and inferior products produced every day, and the instantaneous weight of the batching scale can be viewed from the interface of history curve. The alarm interface can display the valve closing and alarm signals such as feeding timeout and discharging timeout.

The mixing and batching machine comes from the screw conveyor and silo in the raw material workshop, and then it is mixed and fed through the weighing module and quantitative Feeder according to the formula respectively. The mixed material is fed into the mixing and batching through the screw feeder, and the weighing instrument receives the weighing signal and the speed signal, which are converted into the totalized value and the instantaneous flow rate after processing, and then the signal of the totalized value and the instantaneous flow rate is transmitted to the industrial control machine (the upper position) by RS-485 port, and the signal is transmitted to the PLC by 4~485 ports, and the signal is transmitted to the industrial control machine (the upper position) by 4~585 ports. The signal of accumulated value and instantaneous flow is sent to industrial control machine (upper computer) by RS-485 port, and the PID regulator is transmitted by 4~20mA analog current signal, and the regulator compares and calculates the signal with the set value sent by DCS, and then sends the 4~20mA analog signal to frequency converter, and then the frequency converter regulates the rotational speed of the conveyor, and reduces the rotational speed of the conveyor when the flow increases and vice versa, and increases the rotational speed of the conveyor, which makes the flow rate of the conveyed material and the cumulative amount of the phase are kept within the set range. The instantaneous flow rate and the cumulative amount of phases are kept within the set range. It also calculates the instantaneous flow rate and cumulative amount, and can display the cumulative weight, instantaneous flow rate, screw speed, tare weight, alarm signal content, etc., and transmits the instantaneous flow rate signal to the intelligent regulator through 4~20mA linear analog current output.
In the process of dosage, the powder is evenly distributed on the conveyor screw through the feeding hopper, the weight of the material on the conveyor is measured by the load weighing module, and the speed of the conveyor is detected by the speed generator, these two detecting signals are amplified, and then inputted into the pressure-frequency converter circuit with the weighing terminal as the core to become the digital pulse signals in order to enhance the anti-jamming ability. These pulse signals are then fed into the counter of the weighing instrument for counting. After counting and conversion, the load signal on the screw, the speed signal of the screw and the actual feeding rate are obtained, which are compared with the given feeding rate inputted on the industrial control computer. The actual feeding rate is sent to the industrial control computer through communication, and the corresponding adjustment quantity is derived through PID operation, which is then converted into the corresponding thyristor triggering phase-shift angle parameter, and communicated back to the weighing instrument as the time constant of the phase-shift triggering angle of the timer. The synchronization signal circuit is composed of weighing instrument and transformer, the synchronization signal is connected to the external interrupt INT0 port of the weighing instrument, and through the interrupt subroutine, the timer is used to generate the SCR trigger pulse in real time according to the time constant of the phase-shift triggering angle, so as to regulate the output voltage of the bi-directional SCR circuit, and to control the excitation current of the clutch of the sliding motor, so as to realize the speed control of the conveyor and the flow control of the dosing material. dosage flow control.