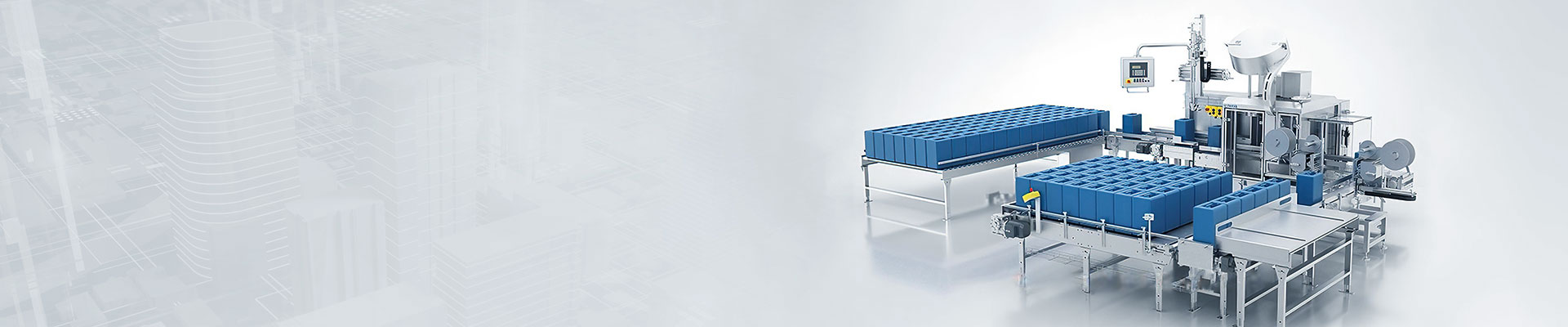
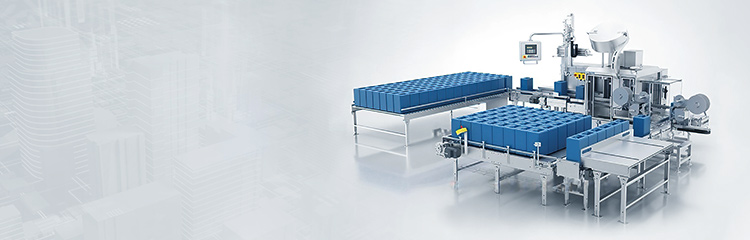
Explosion-proof filling machines are controlled by weight filling with self-adjusting filling nozzles that are adapted to the filling container by means of an adjustable gate or an optional feed screw drive. By setting the gate size through the container, the filling can be set for double dosage, bottom-up filling, facilitating quick changeover.

The automatic Filling machine management software integrates recipe management, filling and weighing, personnel management, report generation, provision of interfaces and data management, of which the most critical part of the software is to solve the data communication between the computer and the Electronic scales. The display divider is used to connect the display at the filling site with the computer monitor in the office, two serial communication lines are used to connect the two electronic scales at the filling site with the two serial ports of the computer host in the office, and the keyboard divider is used to connect the keypad at the filling site with the computer in the office (the workers at the filling site operate the mainframe in the office through the keypad). The distance between the administrator's office and the filling site is 5 to 8 meters.
Explosion-proof filling machines with better openness, scalability and compatibility improve the configuration efficiency of the user interface and bring new creative concepts of device-level automation. In SIMATIC products can be used to configure all WindowsCE-based operator panels, from the smallest panels to touch control panels, multifunction panels. The Quantitative Filling Machine combines the control core of a PLC, the CPU313C from the SIMATICS 7-300 series to design the configuration of a touch panel for industrial filling. Some of the good features include manual operation, fault alarms, recipe management, trend charts (display and analysis) and print results.
Technical Parameters
Maximum weighing capacity: 300kg
Quantitative range: 100kg~300kg
Graduated value: 100g
Canning accuracy: OIMLR61 x (0.2)
Canning speed: 10~20 cans/hour
Power supply: AC220V50Hz
Using air pressure: 0.5MPa
Control mode: 2-speed control
Conveying method: the tank adopts manual conveying method valve material: SUS-304 (optional: SUS-316)