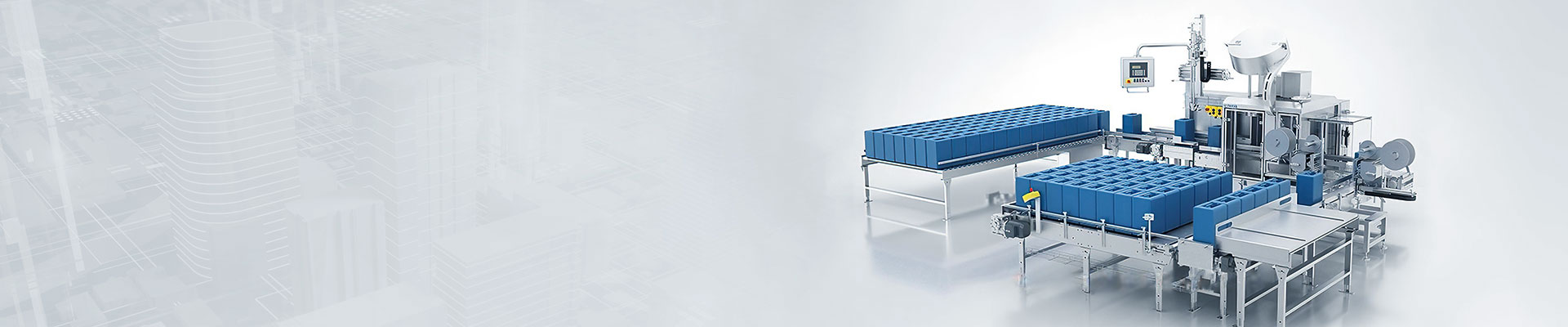
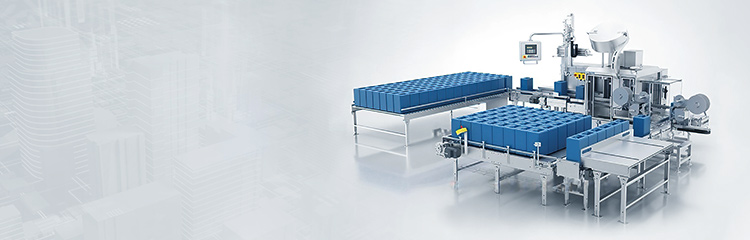
Disinfectant liquid filling machine with capping and labeling machine is a production line that can optionally include a filling solution that can handle different types of liquid products, liquid or thick, foaming or non-foaming, and filled in different packaging forms, consisting of filling, capping, sealing, palletizing, weighing equipment, and corresponding conveyor belts, supplemented by automatic control and automatic adjustment systems.

Automatic Filling machine through the software programming to achieve the weight signal acquisition, by the PLC on its conversion, calculation, and grading control pipeline valve opening, closing, so as to achieve the filling accuracy control; the use of photoelectric position recognition function to control the positioning of the filling container and locking mechanism of the opening, closing, to achieve automatic positioning, automatic start-stop as well as no bucket without the filling control function; material category selection and setting, automatic adjustment and setting of the corresponding parameters for manual/automatic conversion. After the material category is selected and set, the corresponding parameters will be adjusted and set for manual/automatic conversion. Automatic control is divided into automatic control of single machine and overall control of production line. In the automatic state, interconnection and interlocking can be realized between the single machines, and when the single machine needs debugging, maintenance or in case of failure, it can be converted to the manual operation state.
The metering signals of the weighing and filling machine are converted into the PLC through the metering controller and weighing modular respectively, converted into binary code through the program and stored in parallel BCD code in the data register of the PLC, the output voltage signal of the weighing modular is converted through the A/D, accumulated through the junction box and passed to the weighing instrument, which displays in real time the weight of the material in the current weighing (filling barrel). The displayed weight data is transmitted via serial communication to the PLC, which compares the collected weight of the weighing module with the weight set in the touch screen (or computer) in order to control the behavior of the whole filling machine.
Basic parameters:
Maximum weighing capacity: 30kg
Minimum Sensitivity: 0.01kg
Filling error: ±0.01-0.02kg
Filling speed: 20L about 150-180 barrels/hour
Control mode: 2-speed control
Filling method: Insertion, liquid level up
Gun head line: Teflon gun head, valve + Teflon hose
Structure material: host SUS304 stainless steel, conveying palletizing carbon steel anticorrosion paint.
Weighing platform size: 400 × 800mm (304 stainless steel power raceway)
Empty barrel raceway: 400mm × 2500mm (304 stainless steel power raceway) with another 1200mm slope without power roller
Heavy drum raceway: 400mm×2500mm (304 stainless steel power raceway, 2 sets)
Separate barrel device: for 20L barrels, carbon steel anticorrosive paint structure, 304 stainless steel raceway.
Palletizing equipment: pan-transfer type, suitable for pallets 1200×1200×140mm, including supplying pallets, palletizing, and lower pallet conveying.
Pipe pressure: 0.2-0.6MPa (related to material properties).
Material interface: DN40 flange connector 4, according to the user to provide interface standards
Air Connection: User supplied 12mm air hose connector for quick coupling connection
Power supply: AC220/50Hz (user-supplied to one side of the machine)
Using air source: 0.4-0.8Mpa (provided by the user to the side of the machine)
Use temperature: -10℃-50℃
Base conditions: solid concrete floor of the assistant suspension agent flat, concrete thickness should be more than 10cm.
Optional models: standard, explosion-proof filling