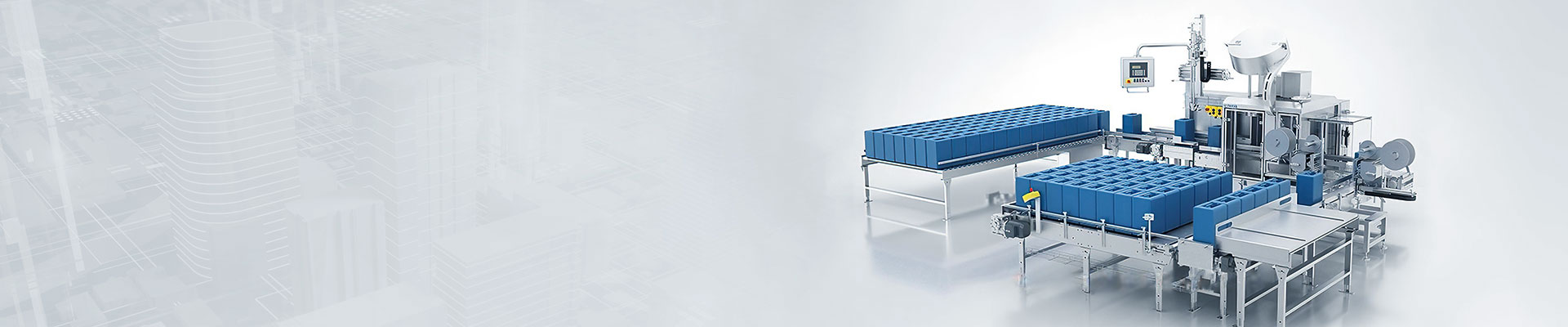
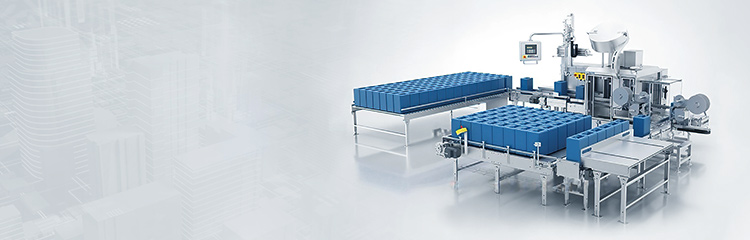
Weighing and filling machine consists of separated visual de-embossing robot, separated visual blocking robot, and double-station visual addressing filling machine, which has the functions of automatic de-embossing, filling, metering, blocking, self-diagnostic, self-testing, self-detection, self-inductive, remote monitoring, composite anti-explosion, and on-line visualization. Adopting advanced visual addressing technology, it is suitable for occasions requiring large quantities of continuous and fully automatic filling. Optional extensions and combinations with other systems ensure individual adaptability.

The weighing and Filling machine integrates computer technology, automatic control, communication technology and weighing technology. The Filling system adopts the programming software and field equipment library in accordance with the IEC-1131 international standard, which provides continuous control, sequential control and high-level language. The field equipment library provides a large number of commonly used field equipment information and function blocks, which can greatly simplify the configuration work and shorten the engineering cycle.
Liquid filling machine application configuration software to complete the data acquisition and process control support a variety of communication protocols to provide users with a variety of equipment support, colorful dynamic screen and the system's powerful features, so that you can easily operate, with a strong scalability, easier to integrate with other systems, more effective protection of the user's investment. The redundant station utilizes two redundant CPUs to improve higher availability and security.
According to the principle of choosing one out of two, the switch automatically switches from the running system to the other system when a fault occurs, and double power supply or industrial Ethernet communication module can be provided and combined for each sub-system. Safe, reliable and advanced practical system design chooses the mature and advanced distributed computer control system, under the premise of centralized management of information and scientific operation in the production process, it makes the danger decentralized and improves the reliability of the system, collects all kinds of data on the site with PLC and transmits them to the central control room for centralized monitoring and management through high-speed network, and the mainframe computer of the central control room also transmits the control commands through the high-speed network to the The mainframe of the central control room also transmits control commands to the PLC measurement and control terminals through high-speed network to implement the decentralized management of each unit.
Basic parameters:
Maximum weighing capacity: 1000kg
Minimum Sensitivity: 0.2kg
Filling error: ±0.2-0.5kg
Filling speed: 1000L about 50-80 barrels/hour
Control mode: 2-speed control
Filling method: Insertion, liquid level up
Gun head line: Teflon gun head, valve + Teflon hose
Structure material: host SUS304 stainless steel, conveying palletizing carbon steel anticorrosion paint.
Weighing platform size: 1200×1200mm (304 stainless steel power raceway)
Empty barrel raceway: 1200mm × 2500mm (304 stainless steel power raceway) with another 1200mm slope without power roller
Heavy drum raceway: 1200mm×2500mm (304 stainless steel power raceway, 2 sets)
Separate barrel device: suitable for 200-1000L barrels, carbon steel anticorrosive paint structure, 304 stainless steel raceway.
Palletizing equipment: pan-transfer type, suitable for pallets 1200×1200×140mm, including supplying pallets, palletizing, and lower pallet conveying.
Pipe pressure: 0.2-0.6MPa (related to material properties).
Material interface: DN40 flange connector 4, according to the user to provide interface standards
Air Connection: User supplied 12mm air hose connector for quick coupling connection
Power supply: AC220/50Hz (user-supplied to one side of the machine)
Using air source: 0.4-0.8Mpa (provided by the user to the side of the machine)
Use temperature: -10℃-50℃
Base conditions: solid concrete floor of the assistant suspension agent flat, concrete thickness should be more than 10cm.
Optional models: standard, explosion-proof filling