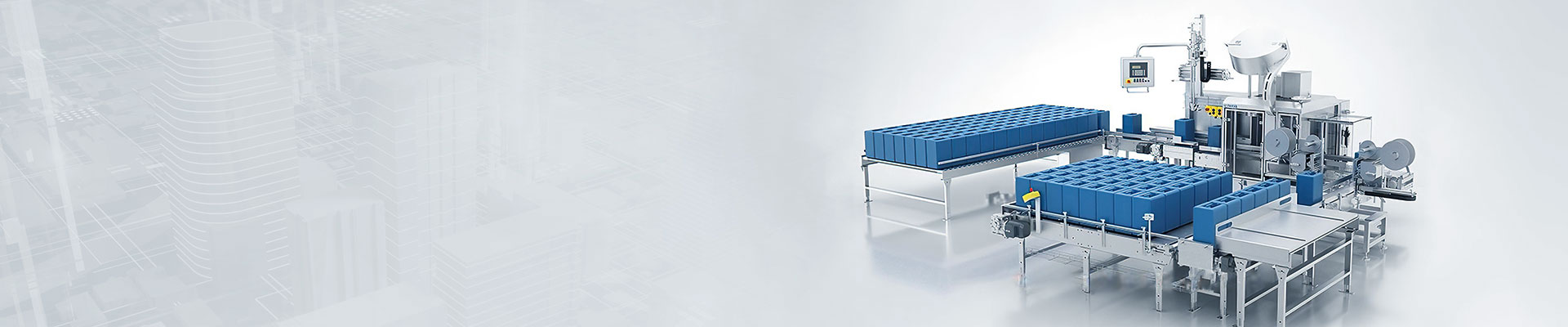
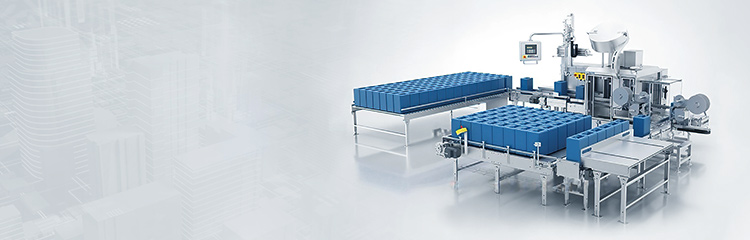
Variable frequency batching system is a device used for pre-mixing, PLC as the main control of the unit, weighing module to collect the weight of the material in the mixer, and should be located (when the material is lost). The limit switch, when the lifting action reaches the position, should send a signal in the appropriate position. Analog output signal, 4-20mA to 4 valve switches, control the opening, with the S-type tension to collect the material position, and close the valve when the weight reaches the required batching weight.

Automatic feeding system is a kind of granular, material feeding, storage, dosing, mixing, conveying, packaging and other links integrated system. According to different material characteristics, advanced weighing module is used for fine measurement of materials. Automatic batching algorithm can realize intelligent batching of materials, reduce manual intervention, and improve batching accuracy and efficiency. The main control object of the Batching system is the vibrating screen, transmission screw and crusher of the four silos, using PLC and frequency converter as the control core, and supplemented by field operation box and touch screen to automatically control the system. The automatic control system adopts Siemens S7-200 series PLC, which mainly realizes the feed speed adjustment of the transfer system, the speed adjustment of the transmission spiral, the material level detection of the raw materials in the bin, the running speed adjustment of the crusher, the manual/automatic mode switching of the system, and the local/remote mode switching. In addition, closed-loop control is carried out on the system transfer screw, the material unloading speed and the material level of the bin.
Feeding system mainly includes manual and automatic control mode, automatic control mode, can be divided into local and remote control mode. Both control modes can automatically adjust the operating state of the inverter according to the amount of material in the bin through the PID closed-loop control model inside the PLC, or manually adjust the operating state of the inverter through the touch screen setting, and local control can also be carried out through the control box.
Schneider inverter, internal PID closed-loop control function and ATEX safety function, can safely achieve internal automatic setting or external manual adjustment control mode quickly switch. Through the frequency converter, the feeding speed of the silo, the feeding speed of the conveyor screw and the crushing speed of the crusher can be continuously adjusted in real time. The touch screen provides the man-machine interface for the system. The touch screen can monitor the production data and equipment status of the system in real time. A control box is installed in the electric room of screening workshop. Receive the control signal of the main control room PLC, the control box is equipped with a simple relay circuit, and the relay state is changed through the control of PLC, so as to realize the remote/local working mode of the inverter. The control box can be used to transition the internal control terminal of the inverter, so as not to change the wiring of the original inverter cabinet.