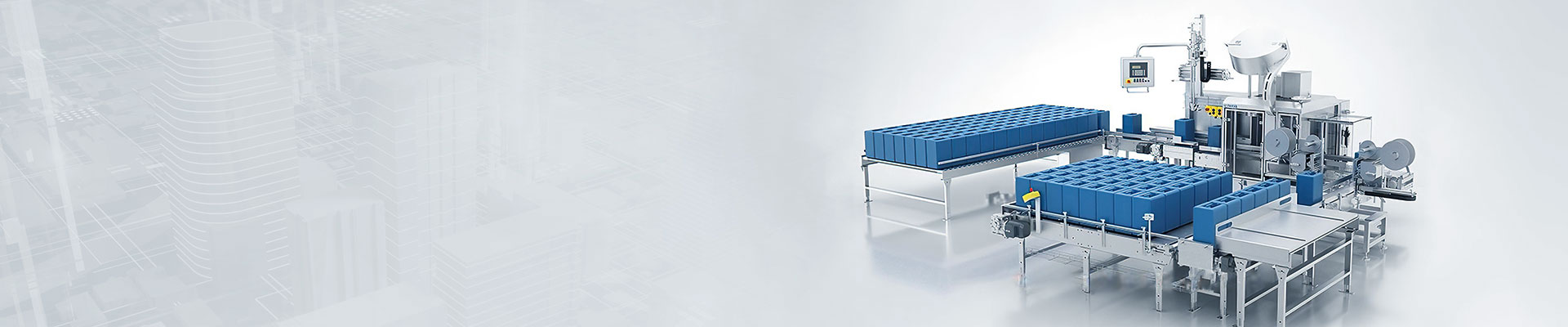
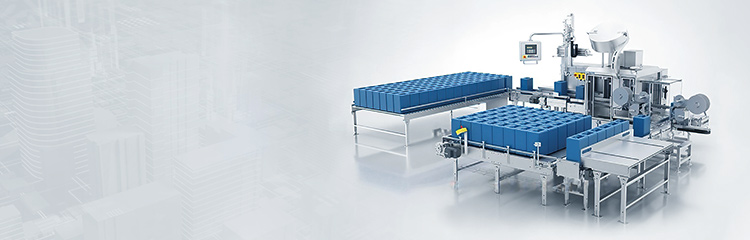
The weighing bin device is a complete set of automatic equipment for dynamic weighing and batching control at the same time. The weight and flow of the material loaded to the weighing and batching truck are controlled by the human configuration monitoring system and PLC program, so as to achieve accurate measurement and batching. As a dynamic continuous metering and batching automatic control device, it can also provide accurate measurement data and control means for the production control and management of various industrial sites.

The weighing silo device is the silo body, silo cover and fixed support, all of which are welded by ordinary steel plates. A weighing sensor is installed under the fixed support. Besides measuring materials, the weighing sensor can also scalar-calibrate the weighing body of the material conveying equipment in the initial stage. The material handling equipment is installed in the lower part of the hanger, and the hanger is suspended. The main working process of the weighing bin with hanger: the material falls into the bin through the feed port on the bin cover, falls into the belt machine installed on the hanger through the bin discharge port and rod valve, and is transmitted to the next production link by the belt machine. The hanger of the equipment is higher than the ground, which makes the material conveying equipment off the ground, and the bin body is supported on the platform by the weighing module as a whole.
Weighing bin with hanger changes the weighing method of traditional weighing equipment on the ground, and connects the conveying equipment and the bin into a whole through the hanger. This installation method enables the weighing module of the bin to measure the weight of the material in the whole, and effectively solves the problem of uneven feeding at irregular times during the unloading process, which causes the measurement fluctuation of the weighing sensor of the bin. The material conveying equipment is detached from the ground, and the bin body is installed on the working platform as a whole by the sensor support and fixed by the weighing sensor support, which does not produce horizontal displacement, so that the gravity sensor on the sensor support is only subject to the force generated in the vertical direction, so the material measurement is accurate.
System composition
1, the feeding part: the feeding part is the part that is fed from the bin to the weighing equipment. According to the different characteristics of the material, different feeding equipment is selected, such as electromagnetic vibration Feeder, screw feeder, etc.
2, weighing part: the weighing part is composed of sensors, standard connectors, junction boxes and weighing buckets, and weighs materials together with weighing instruments and error detection.
3, discharge equipment: discharge equipment can be weighing equipment (decrement method) or discharge equipment (incremental method, zero method), usually by the discharge valve, electromagnetic vibration feeder, screw feeder, electric (gas) valve and other components.
4, control system: batching scale is composed of weighing instrument, upper industrial computer, programmable controller and other control devices.
5, calibration system: the sensor of the batching scale should be adjusted regularly to ensure the accuracy of the system batching.
Main function
1, monitoring function: detect and monitor the instantaneous flow of spiral weighing process, daily total, monthly total, annual cumulative amount and other parameters.
2, screen display: Through the computer monitor can display the operating parameters of the control parameters in the batching process, as well as display real-time batching curve and table.
3, print management: you can print the ingredient report at any time in order to save and query.
4, communication function: I and PLC, the instrument can be two-way data and information exchange.
5, data processing: The system can automatically process the collected signal and output it to the corresponding control quantity.
6, control function: according to the corresponding set value before operation, automatic control of the normal operation of the equipment, including PID adjustment.
7, alarm function: the host in the screen mode and sound and light signal mode alarm various parameters abnormal or equipment status.