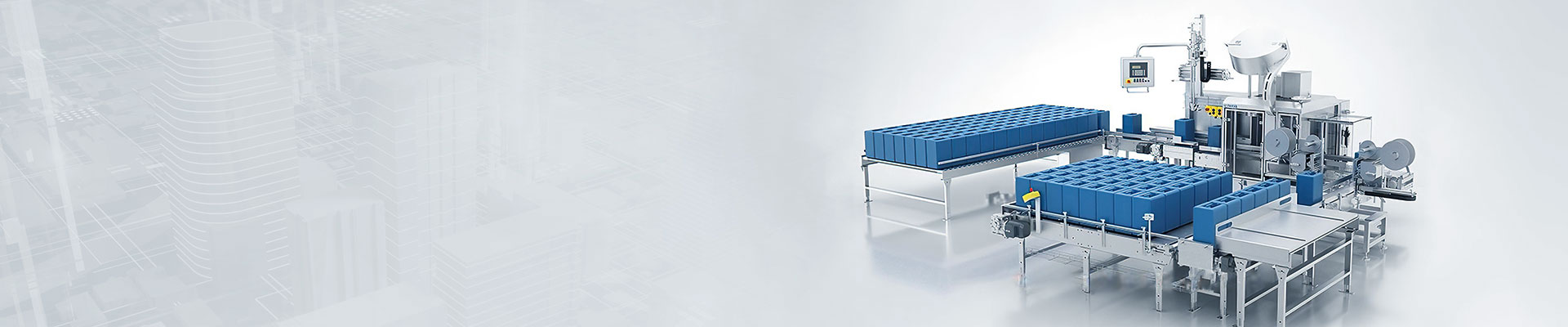
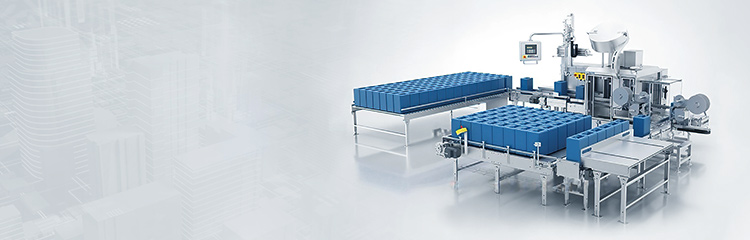
The feed distribution line is a complete set of automatic equipment for dynamic weighing and batching control through electrical control management and visual man-machine software configuration. The electrical control part of the system adopts Siemens PLC, which is programmed according to the production requirements. The software adopts the human configuration, according to the process requirements, through the monitoring system and PLC program to load the material to the weighing hopper weight, flow control, so as to achieve accurate measurement and batching.

The bottom of the storage hopper of the supply distribution line is generally large and small, and when the material is discharged downward from the storage bin, due to the role of the material's own weight, and constantly overcome the internal and external friction resistance to flow downward, the material in the process of falling, its particles continue to mismove, squeeze and recombine to adapt to the change of cross-section shrinkage, and when you want to approach the discharge port, the extrusion friction of the particles is intensified. When the resistance is greater than the weight of the body, it will form a phenomenon such as shed material or bridge, which affects the normal progress of feeding. Therefore, when designing the hopper, the characteristics of the material should be fully considered to prevent the shed material.
When the material level in the storage hopper is reduced, the upper material is reduced, the extrusion pressure between the lower material particles is reduced, the internal and external friction between the material particles is also reduced, and the material flow rate at the discharge port is gradually accelerated. When the material is about to be emptied, its flow rate increases sharply, which will lead to excessive weighing and even overflow from the weighing bucket. Therefore, in order to ensure accurate weighing, a low level meter should be installed on the storage hopper, and the amount of material under the level meter should be greater than 2 times the maximum weighing amount.
Frequency conversion speed regulation control process is mainly through the screw scale to measure the Feeder conveyor, the weighing instrument receives the weighing signal and speed signal, after processing into the cumulative value and instantaneous flow, and the cumulative value, instantaneous flow signal is transmitted by RS-485 days to the industrial control machine (upper computer) with 4mA~20mA analog current signal transmitted to the PID regulator. After the regulator compares the signal with the internal set value, the analog signal of 4mA~20mA is sent to the frequency converter, and then the speed of the screw feeder is adjusted by the frequency converter. When the flow rate increases, the speed of the screw feeder is reduced, and the speed of the screw feeder is increased, so that the flow rate and the cumulative amount of the two materials are maintained within the set range. Thus, reliable product quality is obtained. The parameters and operation process can be set and monitored by the industrial computer, and the value of the PID regulator can also be manually modified. The operation is convenient and the control is reliable. The whole system realizes a high degree of automation and forms a relatively independent and interconnected closed-loop control system.