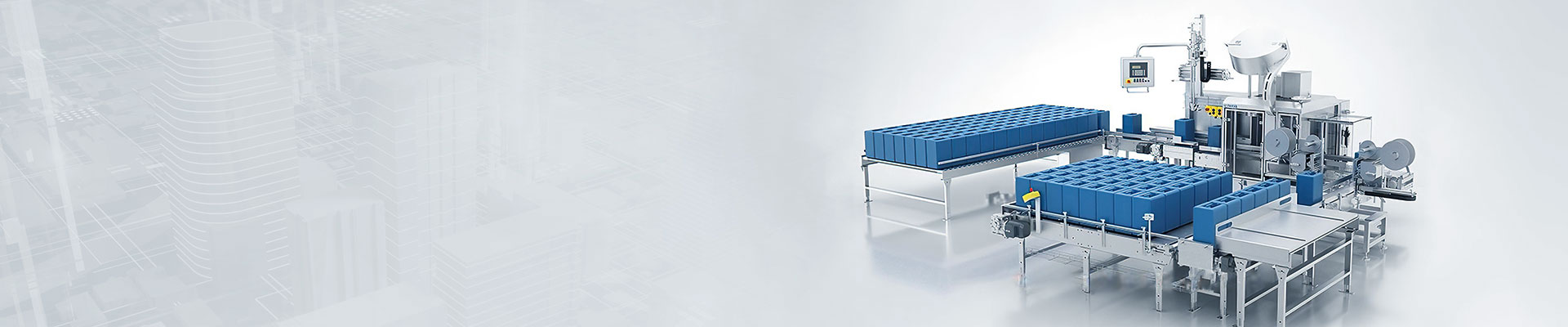
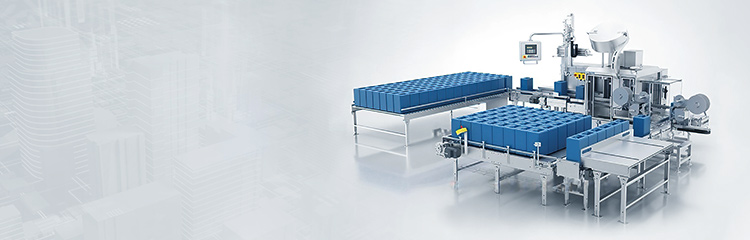
The weighing device of the automatic batching machine adopts a spiral weighing bin, and the materials stored in each bin are not exactly the same. Under the bin is a frequency-controlled broadband feeder, and the materials flow to the weighing bin through the spiral, and then to the mixing mixer, and there are three weighing modules in each weighing scale and connected to a junction box, and the signals are transmitted to the weighing instrument through the junction box, and then the analog signals and pulse signals are transmitted from the weighing instrument to the PLC, and then the PLC processes the signals and outputs DO signals to the computer to monitor and control the operation. The PLC processes the analog and pulse signals and outputs the DO signals to the computer for monitoring and control, and the PLC transmits the commands from the computer to the weighing instruments for processing.

Automatic batching machine for different types of materials (solid or liquid) for conveying, proportioning, heating, mixing and packaging of finished products, such as the whole production process of batching control, the use of PLC control and novel frequency conversion feeding mechanism, with the batching control software package, to achieve the material transfer, batching control, recipe design, production data management and other functions. And it can realize the aggregate control of multiple batching through network.
The feeding system reads the main totalization, instantaneous flow rate, set flow rate, weighing instrument status and other related data from the weighing instrument. Weighing instrument status display (zero state, interval state, running state or alarm state), online monitoring and management by computer, with high requirements on weighing speed, weighing accuracy, system compatibility and expandability.
In the automatic feeding system in the middle layer or different layers of the bus dosage equipment are used between digital signals for communication, while a pair of wires can be realized on the transmission of multiple signals (including a number of operating parameters, a number of dosage equipment status, fault information), a large number of reduced wires and connecting accessories to improve the reliability of the system and the ability of anti-jamming.
The dosage controller is connected to the upper computer and the on-site weighing instrument, reads the formula data sent by the upper computer and returns the real-time data, collects the on-site weighing data sent by the on-site weighing instrument, and controls the on-site actuator to carry out the weighing action. The on-site weighing instrument converts the signals from the pressure weighing module into standard signals, connects to the bus through the bus interface of the weighing instrument, and transmits the weighing data to PLC, which carries out the corresponding control according to the received data. The on-site actuator is controlled by the controller and works according to the instruction to realize the functions of feeding, unloading, receiving and rotating the turntable.