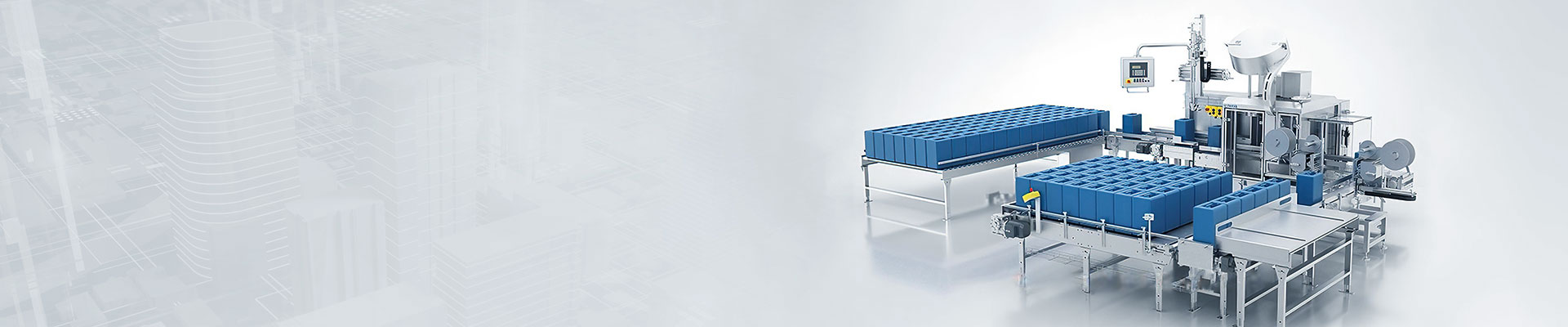
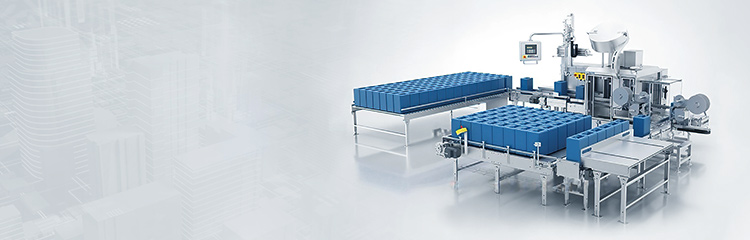
Automatic filling machine in turn: barrel, barrel feeding, feeding, filling, barrel discharge, capping, sealing, stacking and other 9 steps. Cycle scanning according to the procedure programmed by the weighing instrument. It can communicate with the control host through RS485 network. RS485 distributed control system network can be easily formed by using multiple modules. Each network can be connected to a maximum of 255 modules in series, and the network can be connected to the control computer through RS232/RS485 conversion.

The liquid Filling machine is composed of Filling system, frame, stainless steel roller table, capping system, pneumatic control, electrical control and other systems, so as to realize manual bucket placement - automatic filling - manual cap placement - automatic capping - finished product storage, using the PID adjustment most widely used in industrial control for actual flow control, according to weight deviation, The control quantity is calculated by the proportion, integral and differential, and the speed of the motor is adjusted by the frequency converter to make it equal to the set value to complete the automatic filling process. The computer is connected with the weighing instrument through serial communication, which can collect and process the data in real time, input and save the data on the production line. Filling and packaging drums complete the steps of barreling, barrel feeding, feeding, filling, barrel discharging, capping, sealing, stacking and so on. The filling device is equipped with an automatic meter, which will fill the paint directly into the transmitted packaging bucket through the set amount of the filling nozzle according to the pre-set standard, and the packaging bucket filled with liquid will be transmitted to the next step through the power track.
Automatic filling machine is composed of filling, capping, sealing, palletizing, weighing equipment and the corresponding conveyor belt, supplemented by automatic control and automatic adjustment system. When the four-riser drum reaches the feed conveyor belt, the drum is separated by the screw Feeder and sent to the fixed weighing platform under the oil nozzle of the rotating oil tank. The quantitative filling is to arrange the piston cylinder symmetrically around the circular rotating oil tank, and each piston is connected to a shaft by a connecting rod and slides according to the inclined circular trajectory. The first 180 degrees of inclined circular motion causes the piston to rise, and the last 180 degrees causes the piston to fall. When the piston is lifted, the material is controlled by the valve from the upper oil tank into the piston cylinder. When the valve connecting the piston cylinder and the oil injection nozzle is opened, the material is injected into the lower barrel, the bulk metering verification selected by the filling machine is defined according to the time and the total flow per unit time, the precision of the metering verification can be controlled by the PLC, according to the industrial touch screen - touch screen to detect the operation, the main parameters of the operation can be changed online.