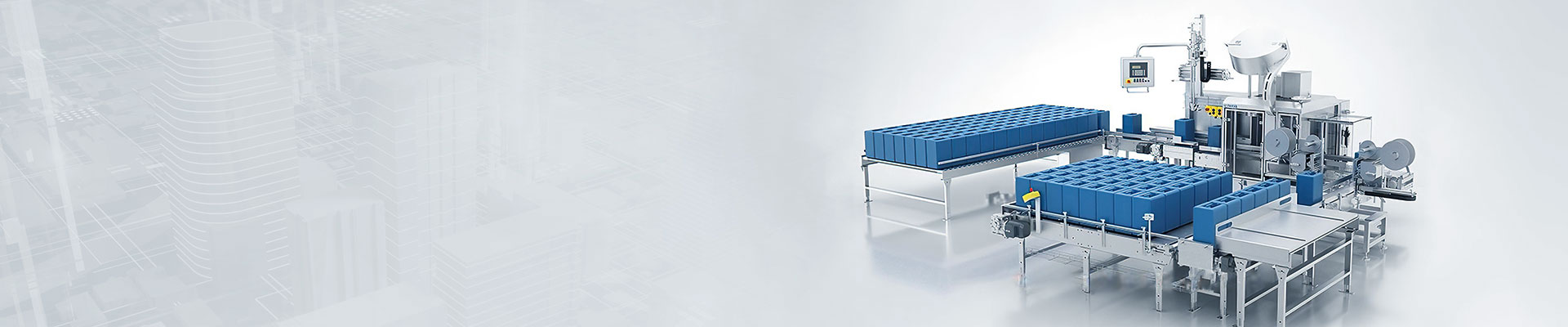
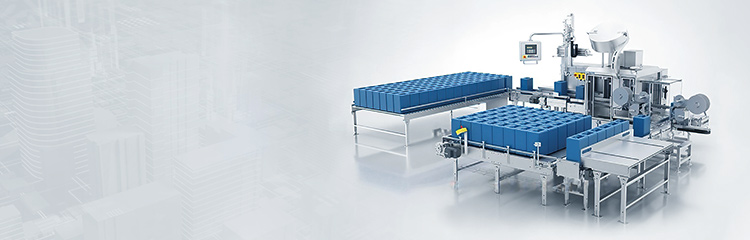
The belt scale adopts three groups of weighing bridge, one of which is installed at the back of the belt conveyor feeding point, where no material passes through, and can only weigh the tare, which can realize real-time online automatic peeling when conveying materials; The other two groups of scales are installed in the front of the blanking point, and weigh the material at the same time during the conveying process, and compare and calibrate the material online.

Belt scales can measure the quantity of material at the end of a cycle as well as the cumulative quantity of material over a period of time, the cumulative quantity being the result of the totalization. To measure the instantaneous quantity, the weight per unit length of the belt is measured and the instantaneous speed of the belt is measured. The instantaneous speed of the belt can be obtained from the rotational speed of the belt scale. Such as the raw materials transmitted on the belt in a certain unit length of the measured value of q (kg / m), at this time the belt's transmission speed for the v (m / s), then Q = qv, 0 indicates the instantaneous amount of material. Since the material flow rate is changing at each moment, the cumulative flow rate should be the integral value of the instantaneous flow rate over time.
General belt control cabinet are placed in the vicinity of the belt scale, so as to facilitate on-site commissioning and maintenance of the belt scale and regular calibration of the belt scale calibration, and at the same time convenient to change the flow of the belt scale after the nearest scale and parameter settings. In the control cabinet of the belt scale is also placed in the electrical control system and weighing instrumentation, will be the scene of the operation of the belt scale and the recorded data real-time response to the spraying center control room, the center control room according to the needs of the production or other aspects of the considerations of the flow of the belt scale to change the settings or to start and stop the belt scale.
The belt control system mainly includes two systems: signal acquisition and signal processing. The function of the signal acquisition system is to collect signals such as motor start/stop status, belt tearing and slipping, and to collect the switching and analog information of the equipment, which is mainly realized by relays and various sensors. Signal processing system is mainly responsible for the function of signal arithmetic and display, the system is mainly composed of PLC, human-machine interface industrial control machine.
The PLC is mainly composed of PLC, human-machine interface (HMI) and industrial control machine (ICM), etc. The controlled programmable controller is the S7-200 controller produced by Siemens, the PLC can adapt to the harsh environment of the underground working surface, and it has strong anti-electromagnetic interference ability to the other electrical equipment in the underground with high reliability and flexible configuration.The CPU selected for the PLC is the CPU226 which is used by the PLC with the analog input module EM231 as the expansion module.The functions of the PLC are mainly to Collect all kinds of signals on the scene, calculate the collected signals through the program, and control the start and stop of the equipment according to the results of the calculation, and at the same time, transmit the signals to the host computer, realizing the real-time monitoring of the belt conveyor. The function of system control is mainly to realize the linkage control of Feeder, belt scale and vibrating screen, and the function of system protection is mainly to realize the alarm for the belt's slipping, deviation, tearing and so on.
The control system is mainly composed of two parts: control function and human-machine interface. The control function is realized by programming the PLC, which is responsible for controlling the sequential start of conveyor and feeder, starting and stopping the control of 1 conveyor and 2 conveyor, sending alarm signals in case of equipment faults and handling the faults, and the human-machine interface is realized by the WINCC6.0 configuration software, which can process the signals acquired by the PLC and present the on-site equipment information to the controllers in the form of sound, animation and image. The configuration software can process the signals collected by PLC and present the information of field equipment in the form of sound, animation and image to the controller.
Operation mode
Automatic operation mode. The automatic control mode is realized by PLC program and configuration software, and the controller controls the equipment starting and stopping through the industrial control machine. When the system is changed to automatic control, the system can automatically control the start and stop of the belt conveyor according to the programmed sequence, and can analyze and calculate the collected signals, and realize the interlock and alarm function according to the analysis and calculation results. In the event of equipment failure or accident, the system can automatically shut down and send an alarm signal. At the same time, the fault conditions will be stored in the configuration system, and technicians can analyze the causes of equipment failure according to the stored fault information. The system can start emergency stop in case of emergency, which can stop all the equipments at the time of emergency.
Manual operation mode. In manual operation mode, the controller can start and stop any equipment. The system sets interlock and unlock status for each belt conveyor. In the interlocked state, the controller can start and stop each belt conveyor in the set order. In the unlocked state, the controller can control the start and stop of the belt conveyor out of sequence.
Starting method
There are two ways to start the equipment: start with material and normal start. When there is no material on the belt conveyor, start the 1 conveyor, then start the feeder, and when the 1 conveyor conveys the material to the 2* conveyor, the 2* conveyor will start, this kind of startup can avoid the 2" conveyor idling, which is called the startup with material flow. When there is material on the belt conveyor, start the 2" belt conveyor and then start the 1" belt conveyor, and then start the feeder, which is called the reverse material flow start.
Frequency conversion control
The motor of the belt scale is controlled by frequency conversion, and the soft start and stop of the motor can be realized by the frequency converter, which reduces the impact on the power grid when the motor of the belt conveyor starts and stops. The frequency converter communicates with PLC, and the constant speed rotation of the belt conveyor can be realized through PLC.
Detection and protection
In order to protect the working safety of the system, the system can monitor and protect the belt scale and motor in real time. A pair of deflection switches are installed at both ends of the belt scale and every 40m, which can issue an alarm when the first deflection occurs, and stop when the second deflection occurs, and pull-wire switches are installed every 40m for the belt scale, which can ensure the safety of the personnel and equipment by stopping the machine in case of failure. PLC and frequency converter can be connected to realize the real-time monitoring of the belt conveyor current and temperature, in the motor current or temperature is too large, the equipment stops running, the system to deal with the fault, to protect the belt conveyor motor. In addition, the system is also set up with other sensors such as smoke, tear and other sensors to monitor the operating status of the belt conveyor.