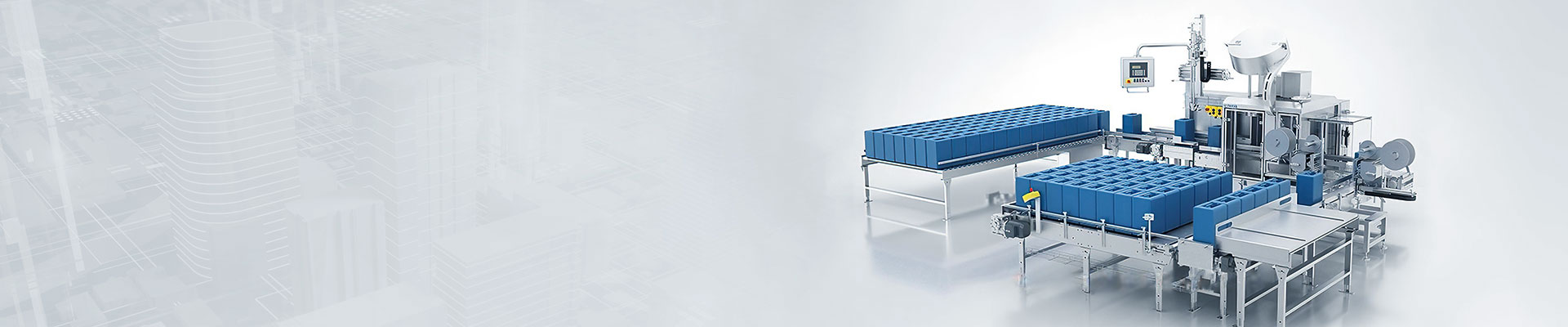
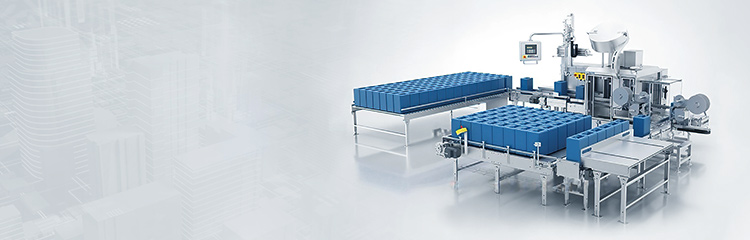
The pellet batching system is controlled by PLC, touch screen and weighing module. The PLC and its corresponding electronic control main circuit are installed in the electrical control cabinet to control the field signal. Touch screen HMI is installed on the surface of the control cabinet to monitor and adjust, display the working status, time setting, ingredient adjustment parameters, alarm information, etc., to improve the reliability of safe operation of ingredients.

The feeding system adopts PLC control system to automatically feed different products with one or more kinds of materials according to the weight ratio specified in the formula. It systematically realizes the functions of material measurement and transmission, dosage control, formula management, production data collection and management.
The feeding system is mainly controlled by PLC, touch screen and weighing module, PLC and its corresponding electric control main circuit are installed in the electric control cabinet to control the field signal. The control cabinet is installed with touch screen HMI for monitoring and adjusting, displaying the working status of dosage, time setting, dosage adjusting parameters, alarm information, etc., in order to improve the reliability of safe operation of dosage. According to different kinds of powdery objects mixed together in different weight proportions and the new material, the use of dynamic data exchange (DDE) technology to achieve InTouch on the production site data collection and transmission, while completing the data interaction between VB and InTouch, and gives a specific configuration process dosage program.
Raw materials are loaded into the silo, after the transportation of the feed extruder screw, the relative density of the granular material increases exponentially), and fed into the two extruder rollers bite angle.
The raw material is extruded into flakes according to horizontally placed (vertically placed) pressure rollers, which are selected according to the characteristics of the material with different surface structures, varying the number of teeth on the surface circle, the total width of the journal grooves and the depth of the journal grooves) as well as the speed ratios of the pressure rollers.
According to the hydraulic control valve's automatic pressure maintaining linear send the working pressure required by the material to the pressure roller, parallel arrangement of the pressure roller can ensure the consistency of the relative density of the material.
The mesh size of the screens in the software of the pelletizing system of the dosing plant can be interchanged for different particle sizes.
The sheet thickness of the material lies in the screw rate of the feed extruder, the speed ratio of the pressure roller and the working pressure of the hydraulic cylinder are adjusted to each other, and significant achievements have been made.