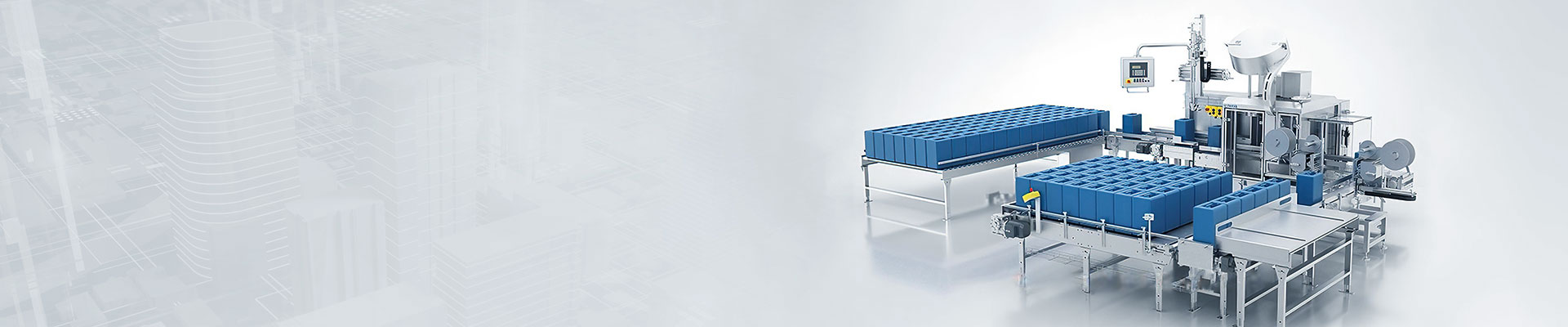
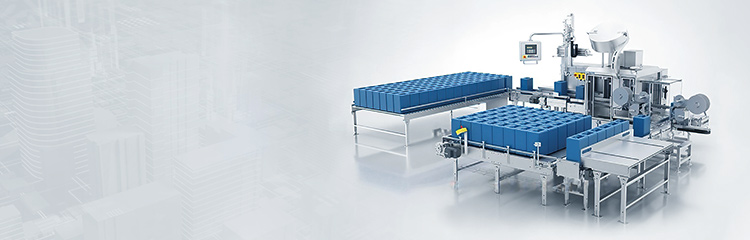
The feeding scale consists of conveying and loading equipment, storage equipment, automatic weighing system, dust removal system and PLC electrical control system. Feeding scale is an indispensable automation equipment in ensuring the stability of industrial production operation and product quality, eliminating the traditional multi-manual work, improving the measurement accuracy of the formula weighing, and realizing the batch production of automatic loading and accurate dosing for a wide range of material varieties.

The feeding scale adopts PID regulation, and the metering control is a combination of metering deviation and frequency conversion speed regulation. The batching control process is a multi-input and multi-output system, where each batching and conveying production line is strictly coordinated and controlled to monitor and regulate the material level and flow rate timely and accurately. The system consists of programmable controller and screw Weighing system to form a two-stage computer control network, connecting field instrumentation, control computer, PLC, frequency converter and other equipment with high intelligence and fast processing speed through field bus. In the automatic batching production process, the main material and auxiliary materials according to a certain proportion with the completion of the spiral conveyor conveyor materials for measurement. PLC is mainly responsible for conveying equipment, weighing process for real-time control, and complete the system failure detection, display and alarm, while the inverter output signals to regulate the spiral speed of the role of the inverter.
The feeding scale is composed of conveying and feeding equipment, storage equipment, automatic weighing system, dust removal system and PLC electrical control system. Feeding scale is an indispensable automation equipment in ensuring the stability of industrial production operation and product quality, eliminating the traditional multi-manual work, improving the measurement accuracy of the formula weighing, and realizing the batch production of automatic loading and accurate dosing for a wide range of material varieties. Weighing and batching equipment is now used in various fields such as lithium, refractory, building materials, cement, ceramics, steel, non-ferrous metals, glass, petrochemicals, machinery, boilers, light industry, electric power, military and so on.
The feeding scale is suitable for the site without continuous batching requirements, these sites do not require high time for batching, can be batch batching, batch allows the existence of a certain time interval, such as the blast furnace slot feeding before and after the two batch time interval of 3 ~ 5min, each batch of material from a variety of materials, materials accounted for the ratio of the requirements of the process over a period of time in a relatively fixed proportion of the composition of a single material is not strict, as long as the composition ratio of materials in more than one batch can achieve the same level, the material composition ratio of the material in more than one batch can be achieved. The composition ratio of materials in a large number of batches can meet the process requirements.
Powder feeding scale various materials are stored in different silos, silo feeding generally use electric vibration feeding, screw feeding or gated feeding and other forms. Measurement is generally used to measure the bin, and equipped with pressure or weighing module for force conversion, the signal is amplified by the secondary instrumentation access to PLC or DCS to complete the measurement. In some of the application occasions of wide time requirements, you can use a measuring trolley for unified measurement, measuring trolley running along the track, positioned in turn to the bin under the proportion of material dosing, the amount of various materials dosed using the method of calculation of the difference between the subtraction. There is also a single fixed measuring bin way, the bins in a ring-shaped distribution in a measuring bin around the measurement of the material is also used to reduce the difference between the measurement of the method, the material from the chute or belt conveyor in order to proportionally add to the measuring bin.
Dosing equipment, respectively, and check the advantages and disadvantages of the method of measurement. Separate measurement can be based on the weight and volume of each addition to the design of the appropriate measurement of the warehouse and measuring instruments, can improve the accuracy of measurement, especially for small proportions of the material, but the measurement of the warehouse and measurement of the equipment doubled, the cost is higher. Reduced difference method of measurement using a measuring silo or measuring trolley, measuring equipment investment is less, and at the same time, due to the same measuring equipment, no matter how the measurement error, but can ensure that the material is proportional to the dosing, but for a small proportion of material dosing is difficult to ensure its accuracy.
After the measurement of the material after the collection, generally form a layer or segment distribution, through the conveying equipment (such as belts or trolleys) to the receiving port, into the next process, that is, the completion of a batch of material dosing. As the material metering, conveying, joining and other aspects of the time can be overlapped, in the control process can be used in parallel, in order to save the feeding time, improve the feeding speed.
Optional parts for each component:
Feeding system: pneumatic conveying (positive and negative pressure), mechanical conveying (bucket, belt, screw, pipe chain, etc.)
Weighing system: static measurement (gross weight, net weight, with mobile trolley), dynamic measurement (self gravity flow scale, belt flow scale, spiral flow scale, etc.)
Weighing and mixing system: continuous mixer, batch mixer.
Packaging system: valve bag packaging machine, open bag packaging machine.
Palletizing system: articulated robot palletizing, mechanical palletizing (high and low position).
Dedusting system: pulse bag duster, plastic burner plate duster, cartridge duster, etc.
Dosing control system: industrial control machine + PLC + printing
Functional features
Suitable for automatic feeding of tonnage bags and small bags, realizing dust-free feeding and loading;
Unique storage bin arch-breaking mechanism has arch-breaking function to ensure good material flowability;
The metering system adopts a variety of feeding institutions with control to ensure high speed and high precision;
Mixing system has continuous mixing and intermittent mixing, mixing forms, to ensure high speed and high uniformity;
Packaging system can be automatically weighed and measured, and the operation is extremely convenient;
-Palletizing system can realize automatic stacking operation, greatly reducing the labor intensity of workers;
Dust removal system can effectively inhibit dust and ensure a good working environment when feeding, measuring, mixing and packing;
Adopting computerized full-automatic control, high precision and speed without guarding, convenient and reliable control system, intuitive display, equipped with fault alarm system, and can be equipped with a printer to print the class output and related data.