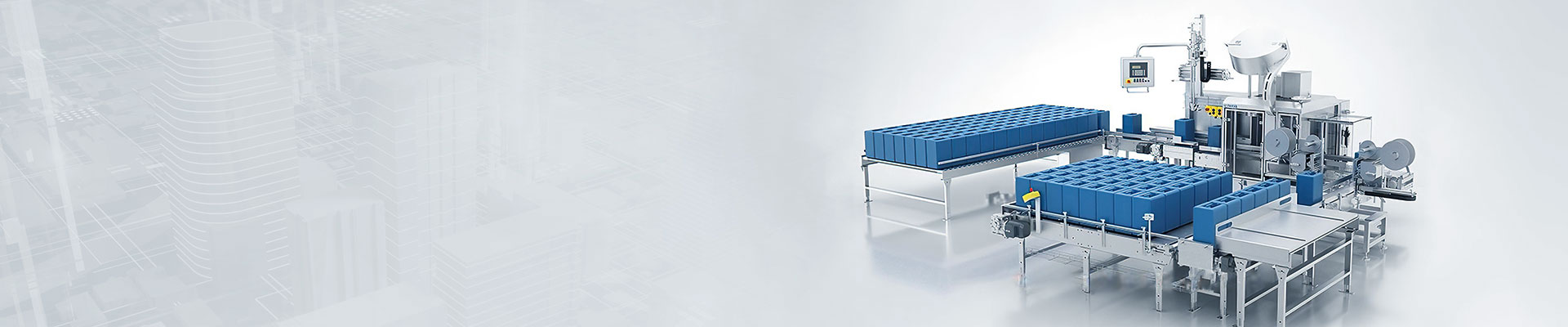
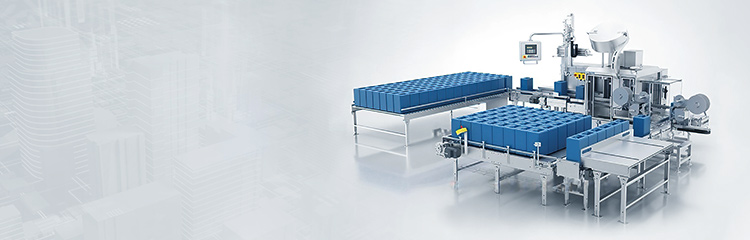
The feeding system is a complete set of automation equipment that realizes dynamic weighing and batching control through electrical control management and visualization man-machine software configuration. The electrical control part of the system adopts Siemens PLC, which is programmed and controlled according to the production requirements; the software adopts human-machine configuration, which controls the weight and flow of the materials loaded into the weighing hopper according to the process requirements through the monitoring system and the PLC program, thus realizing the precise measurement and dosage. The weighing system has strong stability and high cost performance, and can provide accurate measurement data and control means for production control and management of various industrial sites.

Feeding system is suitable for conveying, measuring and batching of powder and granular materials (such as refractory, cement, fly ash and coal powder, etc.). The weighing and batching trolley and screw are used as the conveying tools of materials, and the complete set of automation equipment for dynamic weighing and batching control is carried out at the same time. The Weighing system can control the weight and flow of the materials loaded into the weighing and batching trolley according to the user's specific production process requirements through the man-machine setup monitoring system and PLC program, so as to realize accurate measurement and batching. As a dynamic continuous measuring and batching automatic control device, the weighing system can also provide accurate measuring data and control means for production control and management of various industrial sites.
Feeding system is an important link to ensure the accuracy and uniformity of dynamic quantitative weighing, in order to coordinate the contradiction between weighing accuracy and weighing speed, it adopts two-stage feeding method. Weighing mixer in order to raise the rate and solve the problem of over-difference, the / first fast, then slow, and finally pointing 0 feeding control mode, aimed at / fast feeding 0 to shorten the feeding time, improve the weighing speed; / slow feeding 0 to reduce the impact of the material to improve the detection accuracy; and finally / pointing feeding 0 to replenish the material in order to ensure the accuracy of the final quantitative weighing.
Due to the time-varying nature of the spiral mixer dosage device, with the corresponding dosing flow, when the dosing signal is issued, the weighing screw Feeding machine always lags for a period of time before the start of the dosage; when stopping the dosage, the spiral dosing mechanical inertia and to delay for a period of time before stopping; spiral dosage stops, there is still space in the air has not yet fallen into the hopper of material (known as the fallout, also referred to as the amount of early shutdown), so that the weighed value increases, and its The size of the increase is related to the flow rate before stopping feeding.
Composition of automatic Dosage system
1、Feeding part: the feeding part is the part of feeding from the silo to the weighing equipment, according to the different characteristics of the material, the use of different feeding equipment, such as electromagnetic vibrating Feeder, screw feeder and so on.
2、Weighing part: the weighing part consists of transducer, standard connecting parts, junction box and weighing hopper, which is used together with the weighing instrument to weigh the material and detect the error.
3、Discharge equipment: Discharge equipment can be weighing equipment (reduction method) or discharge equipment (incremental method, zero method), usually consists of emptying valve, electromagnetic vibration feeder, screw feeder, electric (pneumatic) valves and so on.
4、Control system: the dosage system is composed of weighing instrument, industrial control machine, programmable controller and other control devices.
5、Calibration system: the sensor of Batching system should be calibrated regularly to ensure the accuracy of system batching.
The main functions of dosage system
1、Monitoring function: detect and monitor the instantaneous flow rate, daily total, monthly total, annual cumulative amount and other parameters of the belt weighing process.
2、screen display: through the computer monitor can display the dosage process control parameters of the operating parameters, as well as display real-time dosage curve and table.
3、Printing management: the dosage report can be printed at any time, so as to save and query.
4、Communication function: two-way data and information exchange can be carried out between IPC, PLC and meter.
5、Data processing: the system can automatically process the collected signals and output them to the corresponding control quantity.
6、Control function: according to the corresponding set value before operation, it can automatically control the normal operation of the equipment, including PID adjustment.
7、 alarm function: the host in the screen mode and sound and light signal mode alarm various parameters abnormal or equipment status.