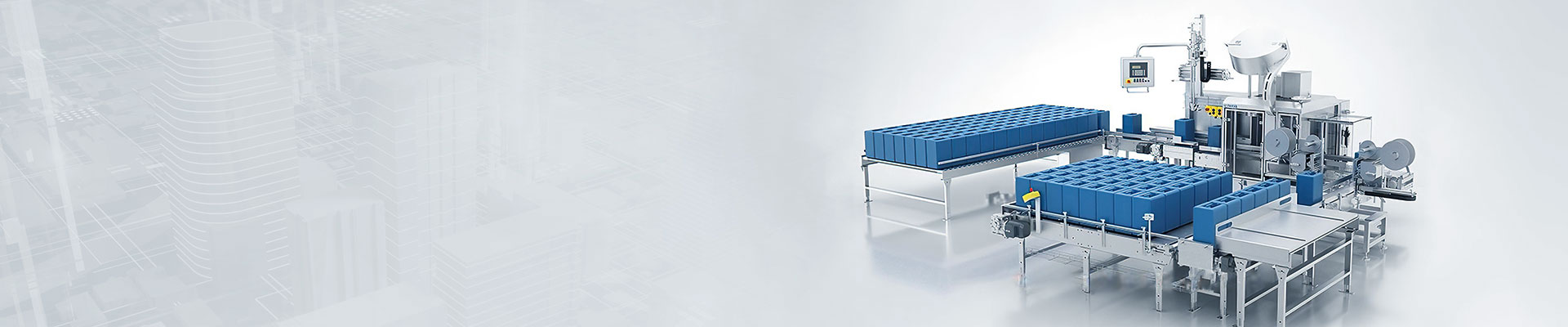
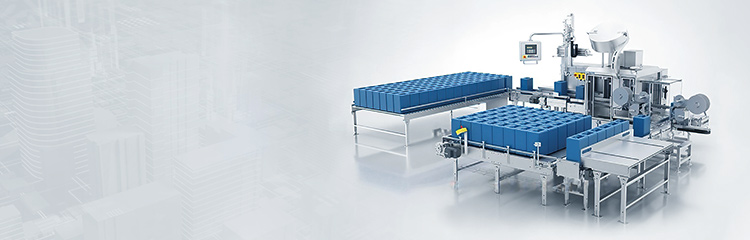
The variable frequency feeding system is mainly composed of steady flow feeding screw, weighing bridge, decelerating motor, weighing sensor, velocity sensor, weighing control instrument and tank system, etc. The weighing bridge is lever-type, and its lever fulcrum uses a lug shaft, which is not affected by corrosion and external factors on measuring accuracy. The velocity sensor is placed on the non-driving end of the helix.Used for quantitative feeding of bulk materials, feeding process for spiral rotation continuous feeding, from the user to the silo or other feeding equipment for material delivery weight detection; At the same time, the speed measuring sensor spiral is installed in the end to detect the speed; The detected weight signal and the speed signal are sent to the weighing controller for calculus processing and display the instantaneous flow rate in tons per hour and the cumulative quantity in tons.

The dosing system is based on the pre-formulated formula to orderly and quantitatively mix a variety of raw materials and related processing to form the required product. Batching production is an important and necessary part of industrial production, the quality of the products produced by batching directly affects the normal operation of the subsequent production, the existing batching through local detection instrument control combined with on-site manual monitoring to achieve automatic and visual batching industrial control system.
The variable frequency feeding system is mainly composed of steady flow feeding screw, weighing bridge, decelerating motor, weighing sensor, velocity sensor, weighing control instrument and tank system, etc. The weighing bridge is lever-type, and its lever fulcrum uses a lug shaft, which is not affected by corrosion and external factors on measuring accuracy. The velocity sensor is placed on the non-driving end of the helix. It is used for quantitative feeding of bulk materials. The feeding process is spiral rotation continuous feeding, and weight detection is carried out on the material conveying from the user to the bin or other feeding equipment. At the same time, the speed measuring sensor spiral is installed in the end to detect the speed; The detected weight signal and the speed signal are sent to the weighing controller for calculus processing and display the instantaneous flow rate in tons per hour and the cumulative quantity in tons.
The batching machine is to realize the function of motor start/stop, thermal protection and high/low speed conversion. According to the requirements of the batching process, each reactor is equipped with a stirring motor, and the stirring motor needs to be switched between high and low speed operation modes. Is the switching switch for high/low speed operation of the mixing motor (2 gears: high speed and low speed). When FSB1 rotates to the low gear, the contactor KM2 line receives power (at this time, the contactor KM3 and KM4 line loses power), its normally open contact is closed, and the mixing motor Ml is in the low speed (triangular) operation mode. When FSB1 rotates to the high-speed gear, the contactor KM3 and KM4 lines are covered with electricity (at this time, the contactor KM2 loses power), the corresponding normally open contact is closed, and the stirring motor Ml is in the high-speed (double star) operation mode, respectively controlling the reactor discharging.