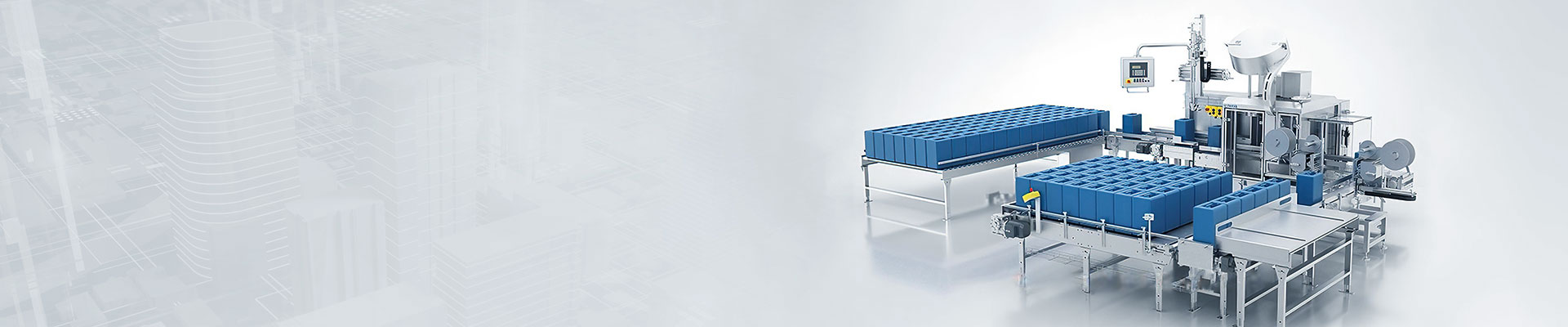
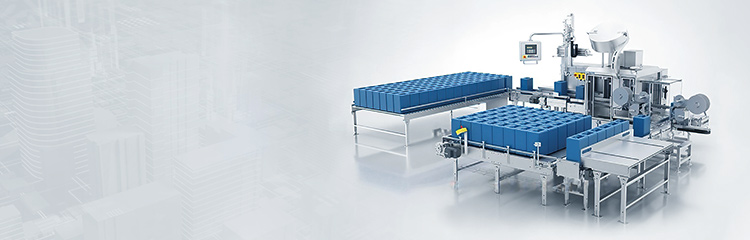
The pneumatic batching system mixes and feeds the mixture according to the formula through the weighing module and the tank, and the mixed material is sent to the reaction kettle by the fan for mixing and batching. The weighing instrument receives the weighing signal and the speed signal, which is converted into the cumulative value and the instantaneous flow rate after processing, and the cumulative value and the instantaneous flow rate signal are transmitted to the industrial control machine (upper computer) by the RS-485 port.

Pneumatic conveying system is the use of air energy in the closed pipe to transport granular materials, powder materials. The pneumatic conveying used in the packaging of dried finished products is composed of an air source part, a sending part, a pipeline part, a material receiving and dust removal part, and a control part. The delivery bin pump is a key part of the transmission, and its role is to mix the material and compressed air into the transmission pipe for transmission.
The weighing module, as an analog sensor for detecting weight, is installed under the support of the silo, and the loading amount of the required material is set and input on the touch screen. If the loading amount of the material is set to be less than the minimum limit or greater than the maximum limit, the system will issue an alarm. When the loading amount is set within the range of the loading amount, it is compared with the value set inside the system, and the PLC output controls the fan in the pipeline from the lower level to the upper level in order to start and put materials. If the amount of material to be loaded is less than or equal to 10% of the set material load, the conveying is in low speed operation; If the amount of material to be loaded is set at more than 10% of the material load, the conveyor is automatically converted to high-speed operation, and the material is also increased, thereby improving the conveying speed and shortening the material loading time. When the loaded material reaches 90% of the set load, the conveying automatically switches to low-speed conveying, and the material dropping is reduced. When the material loading reaches 100% of the set value, the conveying automatically stops and the material loading is completed.
The specific principles are as follows:
Feeding stage: the sealing valve, air sealing valve and exhaust valve are opened, and other valves are closed. The material falls into the bin pump under the action of gravity. When the time reaches the set value, the sealing valve, air sealing valve and exhaust valve are closed to complete the feeding process.
Fluidization stage: the intake valve automatically opens, the compressed air enters the bin pump, diffuses through the fluidized bed, and gradually increases the pressure in the bin pump when the material is fully fluidized.
Conveying stage: When the pressure of the transmitter reaches a certain value, the pressure transmitter sends a signal, the discharge valve automatically opens, the material fluidization on the fluidized bed is strengthened, the conveying begins, the material in the bin pump is gradually reduced, and the pressure display gradually falls back. In this process, the material on the fluidized bed is always in a state of fluidization and conveying.
Purge stage: when the material in the pump is completed and the pressure drops to the pipeline resistance, the intake valve is closed, the discharge valve is closed at a certain interval, the pressurization continues for 3 ~ 5s, the pipeline is cleaned, the feed valve is opened, and a transmission cycle is completed.