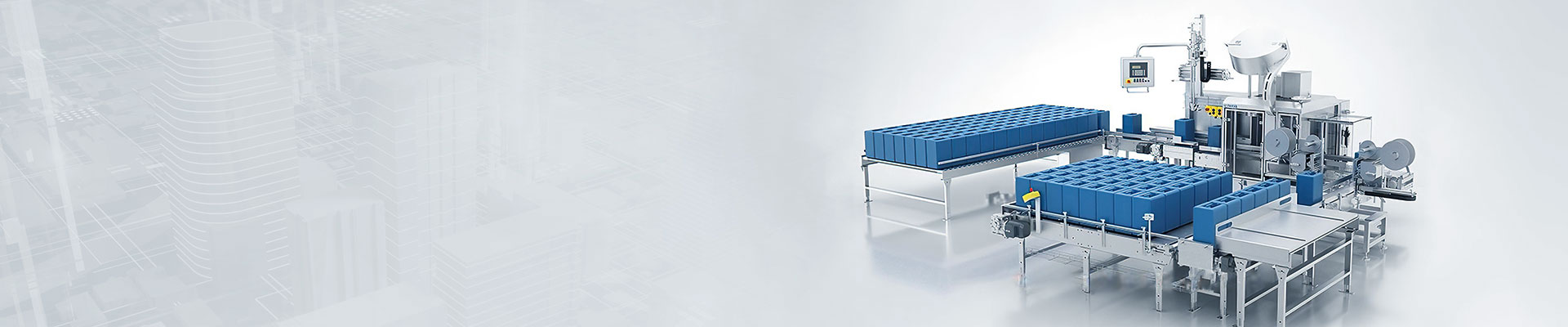
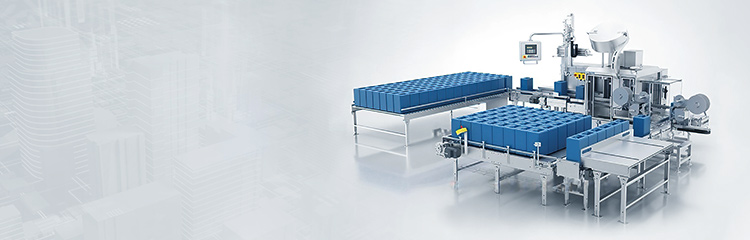
The signal of the weighing sensor collected by the weighing hybrid system is a MV-level small signal, and the dynamic weighing signal of the weighing module is in the range of 0 ~ 30mV, which can not be directly read by PLC, and needs to be processed by an external amplification circuit to convert it into a standard voltage signal of 0 ~ 10V. In order to achieve voltage amplification, four operational amplifiers with true differential input are used in LM324 series devices. The converted standard voltage signals from 0 to 10V are converted into digital signals that can be directly input into PLC modules through A/D converter (EM235 analog input module). Finally, these digital signals are transmitted to PLC for calculation and comparison. If the input reaches the pre-set value, the cylinder action is controlled and the blanking port is closed.

Weighing batching machine is mainly composed of PLC, feeding device, weighing device and frequency converter. The operator inputs the chemical composition and proportion of various raw materials through the operator station, and the flow signal is converted into a signal of 4~20mA through the weighing equipment and weighing display, which is input to the function module and compared with the set value. The control word obtained is transmitted to the inverter through the bus, and the inverter controls the speed of the motor of the feeding device according to this signal. The feeding amount of each feeding device fluctuates slightly up and down the set value, and the frequency of batching feeding is controlled by the PLC output and the instrument setting. When the given PC system fails, the instrument output can be switched to ensure the continuity of production at the PLC output. When the operator selects a given rate on the operating screen, the field inverter is controlled in three ways: a given rate, a given flow rate and a given frequency. By entering the total flow of the ingredients and the ratio of each scale, the feeding amount of each scale can be automatically calculated, and the tracking adjustment is made according to this feeding amount. In adjusting the PID parameters of each scale, the flow setting controls the flow of each scale through the flow setting area on the screen.
The feeding system is mainly composed of computer (server, engineer workstation, each production workstation), main module (including digital module and analog module), Electronic scale, control station, field measurement module, field touch screen button box, etc. The equipment is an optimized combination of advanced control concepts that effectively ensure data management by computer, weight marking by dynamometers, control of production modes, management of dosing software using HPS, comprehensive production testing and safety management, and safe operation of the equipment. When starting the ingredients, the ingredients are supplied according to the set formula parameters and production sequence. The host computer displays the status of the ingredients. Multiple interfaces can be viewed on the computer, including the main interface, the main reaction sub-interface, and the temperature curve interface. After operation, the material is supplied according to the target weight and material sequence set on the main computer, and the corresponding valve is automatically opened during measurement. After reaching the set target number, the valve will be automatically closed, in order to better control the measurement accuracy, you can set a low speed rotation value on the computer, and close the discharge valve in advance, thereby reducing the impact of the emission weight on the measurement.