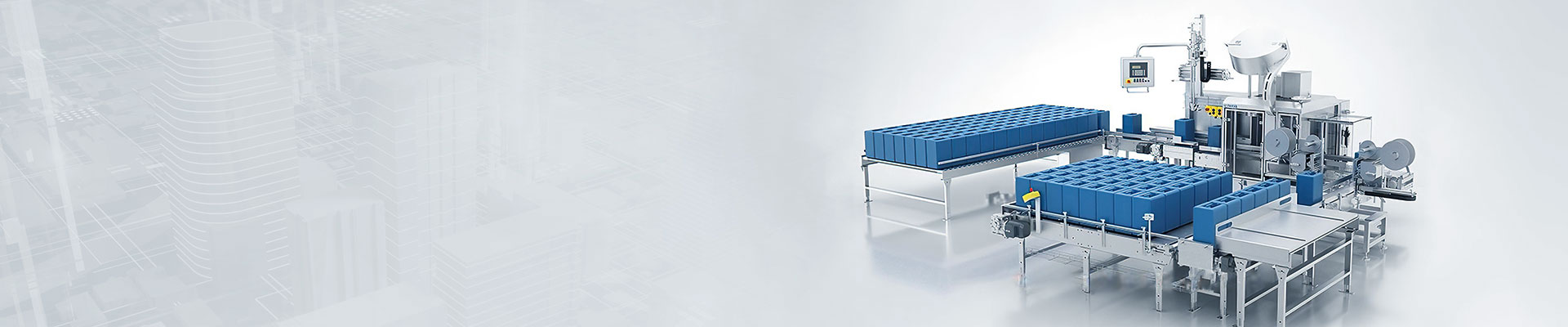
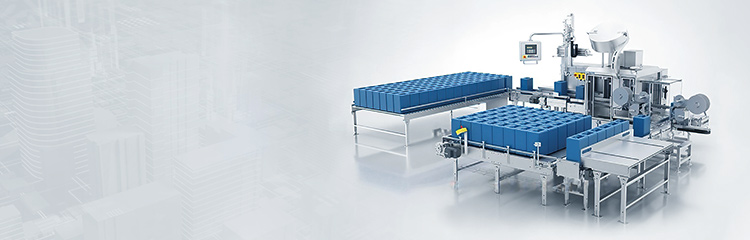
Automatic feeding machine is mainly composed of PLC, feeding device, weighing device, frequency converter and so on. The operator input the chemical composition and ratio of various raw materials through the operator station, the flow signal is converted into a signal of 4 ~ 20mA by the weighing equipment and weighing display and input to the function module. Compared with the set value, the PID operation of the continuous control block transmits the obtained control word through the bus to the frequency converter, and the frequency converter controls the speed of the motor of the feeding device according to this signal. Thus, the feeding amount of each feeding device fluctuates slightly above and below the set value to realize the automatic dosing function.

The main control functions of the charging machine include main process parameter setting, equipment chain start and stop, main process parameter browsing and query, etc. PLC will collect the equipment status, material flow, storage quantity through Ethernet to the industrial computer display, easy to control the production process. At the same time, the data of the actual speed of each motor, current signal, the amount of material in the distribution bin, and the warehouse signal are stored in historical records, which is conducive to the query of the cause of equipment and production faults.
The Feeder is the core part of the production of ingredients, which requires high accuracy, reliability and confidentiality of ingredients. The automatic feeder adopts the mass batching method, where various powder, particles and flakes are batching by the weighing equipment according to the ratio input by the operator. The accuracy of the ingredients directly affects the stability of the ingredients content, so higher requirements are put forward for the control system.
Automatic Feeding machine is mainly composed of PLC, feeding device, weighing device, frequency converter and so on. The operator input the chemical composition and ratio of various raw materials through the operator station, the flow signal is converted into a signal of 4 ~ 20mA by the weighing equipment and weighing display and input to the function module. Compared with the set value, the PID operation of the continuous control block transmits the obtained control word through the bus to the frequency converter, and the frequency converter controls the speed of the motor of the feeding device according to this signal. Thus, the feeding amount of each feeding device fluctuates slightly above and below the set value to realize the automatic dosing function. The control output can be changed by adjusting the proportional coefficient, integral time constant and differential time constant respectively, and better control effect can be obtained.
In the first and second mixing, it is necessary to add the appropriate amount of liquid to ensure the permeability of the ingredients and improve the yield and quality. The amount of liquid added to a mixture is related to the original liquid content of the raw material. Adding liquid twice makes the liquid content of the mixture reach the target value set by adding liquid twice to improve the air permeability; The primary liquid addition is controlled by a rough percentage of liquid addition, and the secondary liquid addition is controlled by PID. The daily standard liquid content is set, and the measured current liquid content is compared with the target liquid content, and the feedback correction with the given deviation is carried out to realize the automatic control of liquid content.
The batching heating tank control system mainly completes the detection and control of the relevant parameters of the batching heating tank, such as the pressure of the heating tank, the temperature of the heating tank ignition section, the temperature of the heating tank preheating section, the tank pressure, the material flow rate, and other parameters of the manual automatic control. And through the data display screen and historical trend screen to achieve jl cup control, and alarm/history record and other functions.
In the above automatic adjustment, manual/PID undisturbed fast switching can be achieved, requiring that the average value of the control quantity or the controlled quantity before and after the switching is equal, so it is necessary to calculate the average value of the control quantity or the controlled quantity before the switching, and then switch, in order to achieve the minimum impact on the process and truly realize the undisturbed switching. First, the average value of the controlled quantity per minute was tracked and calculated on the host computer. Take this value as the given value for automatic initialization; When switching from automatic to manual, the average value of control quantity per minute at that time is tracked and calculated on the upper computer, and this value is used as the control value at the initial manual time. PID control can be switched between manual control and automatic control without disturbance.