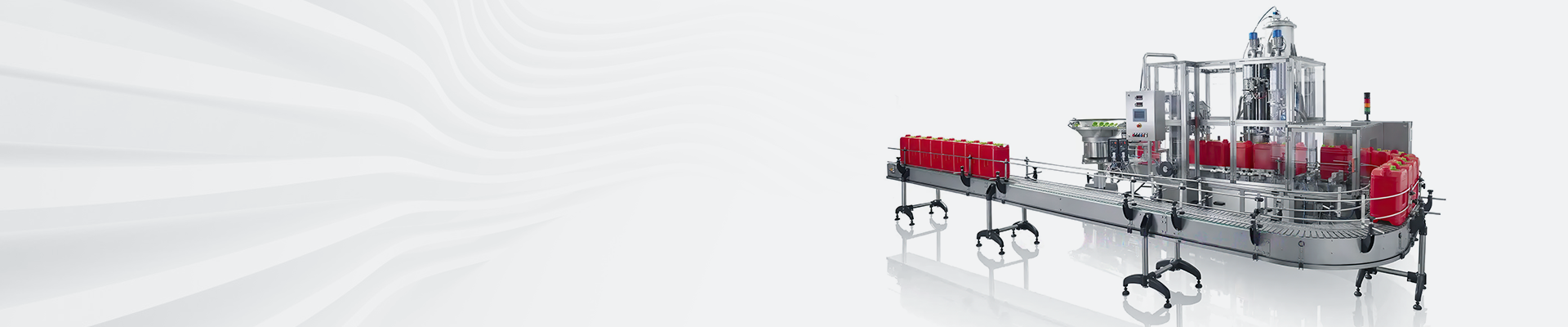
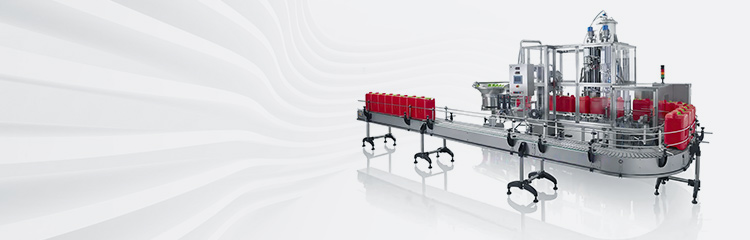

Summary:The liquid filling machine is mainly composed of a weighing module, a frequency converter, a servo drive motor and low-voltage electrical appliances.The main task is to compare the deviation between the set value and the actual weight and change the output signal through PID adjustment to control the speed adjustment of the servo drive motor by the frequency converter, thereby achieving constant weight control.
The whole set of system of automatic filling machine adopts explosion-proof standard manufacture, fast and slow two-stage or fast, or slow, slower three-stage filling mode, the target amount is set freely. Selection of high-precision, reasonable range weighing module and filling actuator, start/stop control of discharging, through the weighing instrument TR700 into the PLC, through the PLC and TR700 cooperation, the servo controller controls the stepping motor to run accurately to the designated station and accurate unloading, filling production line in the program set interlock to ensure that the moving/unloading mechanism during the filling operation in an orderly and reliable manner. For the convenience of actual operation and maintenance, under the manual operation mode, the personnel can operate the various institutions on the site through the lighted operation buttons on the stainless steel analog screen on the surface of the controller cabinet, and observe the equipment operation intuitively.
The weighing and filling machine realizes communication with the central control room through RS485 bus, which can be controlled independently as well as realize PLC on-line control. Equipped with monitoring system, it has the functions of human-computer interaction, communication, display and storage, printing, etc. It also has data and graphic display, status monitoring, data input, information storage, and other functional screens related to operation. It can realize real-time process data monitoring, simulation display of process flow, real-time data record checking, operator privilege setting, process parameter setting, setting alarm for running process events and switching between manual and automatic control. The computer downloads the program and monitors the operation of the equipment through the Ethernet PLC on-line. The touch screen communicates with the PLC through Modbus 485 communication protocol, displaying the operating status of the equipment and setting the operating parameters for starting and stopping the equipment. The actuator is responsible for executing the instructions from PLC and performing the corresponding actions.
The filling system is mainly composed of filling management, metering and delivery control modules. The central control and management system is connected to the industrial Ethernet to obtain the filling request of the workshop filling, optimize the scheduling, and send the filling instruction to the metering and delivery control system. After receiving the instruction, the corresponding pipeline valves are opened and centrifugal pumps and robots are used to carry out transfer and gripping, and the product is automatically transported to the corresponding position. Profibus system configuration, PLC controller as the master station, ET200 distributed I / 0 for the slave station, to realize the electronic scale, frequency converter and centrifugal pump control and monitoring of the liquid level of each barrel and manipulator. Complete the metering and conveying process status monitoring, alarm display and manual operation and other functions. According to the requirements of the filling system, choose inverter + PLC + touch screen + weighing module control program to design, this control mode has the following advantages:
Flexible and convenient control mode;
With good communication interface, it can be convenient to exchange data with other dosage systems, and has strong versatility;
Due to the serialization and modularization of PLC products, the user can flexibly compose a variety of scales and requirements of different control batching. In the hardware design, only need to determine the PLC hardware configuration and external wiring of I/O terminals, when the control requirements change, it is convenient to change the control program in the memory through the computer, convenient for on-site debugging;
Due to the strong anti-interference ability and high reliability of PLC;
PLC-based control system is mainly composed of weighing instrument (PLC), frequency converter, weighing module, servo-driven motor, and the system can be divided into three major parts, namely, actuator, signal detecting mechanism, and control mechanism, as follows:
Actuator: servo drive motor. The servo drive motor drives the servo scale to run, controlled by the frequency converter according to the set flow rate and real-time flow rate deviation of frequency conversion speed regulation, change the motor speed, so as to realize the constant flow rate control.
Signal detection mechanism: In the system control, the signals to be detected include weight signal, material level signal and alarm signal. The weight signal reflects the main feedback signal of the weight value on the servo. Weight signal is an analog signal, need to A/D conversion; material level signal reflects whether the material is sufficient, this signal comes from the hopper level; alarm signal reflects whether the dosage system is running normally, whether the motor is overloaded, the frequency converter is by there is anomalies, the signal for the switching signal;
Control mechanism: the control mechanism for the weighing instrument, frequency converter, PLC is the core of the whole control system. The PLC is the core of the whole control system. It directly collects the material level, weight and alarm signals in the system, analyzes and implements the control algorithms of the data information from the man-machine interface and the communication interface, and comes up with the control scheme of the actuator, and controls the actuator through the frequency inverter and the contactor; the frequency inverter is the unit of speed control of servo-driven motor, and it can change the motor's running frequency according to the PLC's control signals, and completes the speed control of the motor. The frequency converter is the unit to control the rotational speed of the servo-driven motor, changing the frequency of the motor according to the PLC control signal to complete the control of the motor's speed.