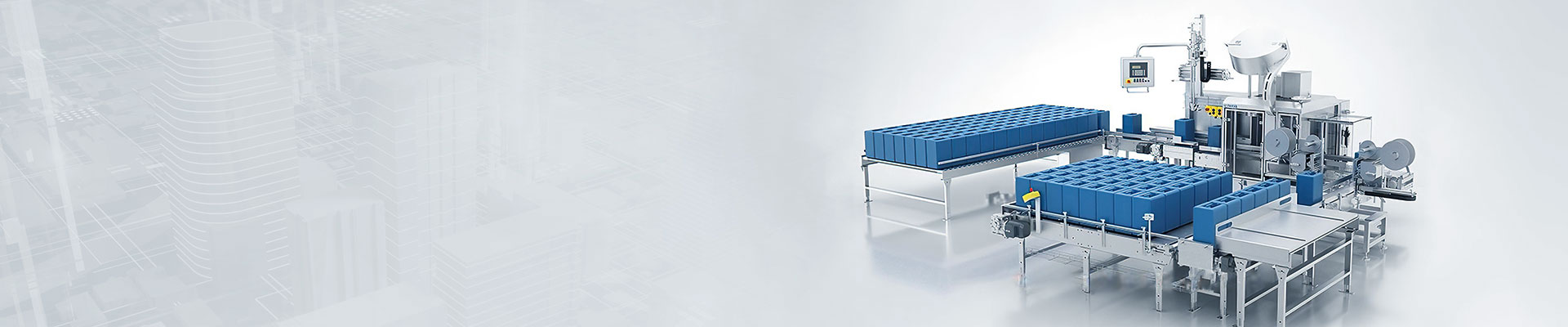
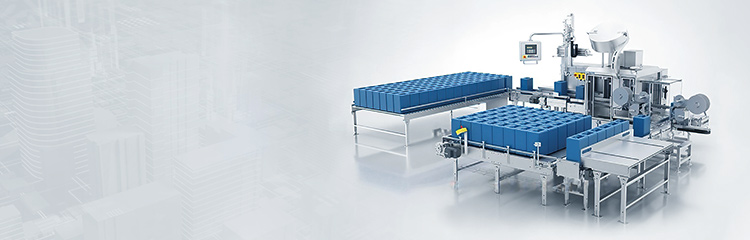
The batching is composed of industrial control computer, OP TO22RTUMUX unit, Windows98, AI MAX control software, system power supply and distribution, field detection, control and so on. After data acquisition, scale transformation, filtering processing, and PID function block operation of the given value, two adjustment values are sent out respectively, and the output is converted by D/A, one way to adjust the frequency converter speed of the feeding screw to control the feeding amount, and one way to adjust the opening of the electric regulating valve to control the flow rate, so as to achieve the purpose of accurate feeding according to the ratio.

The design of the automatic proportioning scale adopts the overall control structure of the combination of industrial control configuration software and PLC. The management and remote monitoring of the mixed proportioning scale are realized by the industrial control machine. The PLC completes the action control and related signal processing at the equipment level, and the connection and communication of the proportioning scale are realized through Ethernet and RS-485 bus. The positioning system of batching truck is improved, and the positioning box is used to realize the position coding scheme, and the positioning accuracy is improved.
The proportioning scale consists of a computer as the human-machine interface of the whole Weighing system. It is set as the main station to complete all automatic batching scale parameter setting, process monitoring and data recording; The other weighing touch control instrument acts as the slave station, relying on the master station, and is in charge of the data setting and process monitoring of the later ingredients. The main station communicates directly with the Siemens S7300PLC system and weighing instruments. The sealed junction box is used on site, which is dustproof and moisture-proof to ensure reliable signal transmission. Weighing instrument adopts special industrial process touch controller. The weighing system communicates with the central control room through RS-485 bus, which can be controlled independently or by PLC.
The silica gel proportioning scale includes the following parts:
1, user management: including adding, deleting, modifying users.
Different users have different operation rights, through the user classification, partition management, you can ensure the safety of the batching scale.
2. Management of scale. The management of the scale mainly realizes the increase, deletion and modification of the scale. For a silica gel proportioning scale, the scale, as a measuring tool, plays a crucial role in product quality. And the balance as a measuring tool, because of its own characteristics, there will be delay error. The user can set its parameters according to the difference in the physical characteristics of the scale, and its setting screen is as follows: As can be seen from the above, including feeding delay, feeding time, emptying limit, closing delay and other parameters can be set. In this way, different control schemes can be implemented according to the different physical characteristics of different scales, so as to improve the control accuracy.
3. Bin management. The bin is a temporary storage place for various raw materials before batching, and the feeding control of the bin also has a great influence on the control accuracy. Silica gel ingredients for the bin management function is also very powerful, in the feeding, the first fast feeding, when the set range is reached, you can reduce the feeding speed, but also provide the drop control. If the above control has not reached the control accuracy, you can also use the point control to precise dosing.
4. Parameter management. Parameter management Provides other auxiliary management functions. Including site, customer information, construction site, transport vehicle number, basic parameter setting, input switch monitoring, output switch monitoring, calibration scale and other functions.
5. Formula management. Silica gel production enterprises can adjust the formula at any time according to the production needs, including adding, deleting and modifying the formula. A recipe management tool with no quantity limit is available in the dosage scale.
6. Plan list. The schedule list is the production of a specified quantity of a specific product in a specified formula according to the production plan. You can specify the formula, customer, loading number, number of production, number of mixing tanks, etc.
7. Real-time monitoring of production process.
Through dynamic graphics real-time monitoring of the production screen, you can automatically or manually control the production process through the computer, and timely understanding of production dynamics.
Silica gel ingredients can automatically manage the production process of silica gel mixing, while greatly improving the control accuracy and ensuring product quality.
8, proportional adjustment (feeding closed-loop control) principle closed-loop control process is mainly through the measurement of the material transported by the disk Feeder, the computer integrator receives the weighing module signal and speed signal, and is converted into the cumulative value and instantaneous flow after processing. And the cumulative and instantaneous flow signal is transmitted to the industrial control machine (upper computer) by the RS-485 port, and the 4~20mA analog current signal is transmitted to the AI regulator, the AI regulator compares the signal with the internal setting value, and sends the output 420mA analog signal to the inverter, and then the inverter adjusts the speed of the disk feeder. When the flow rate increases, the speed of the disk feeder is reduced, and conversely, the speed of the disk feeder is increased, so that the flow rate of the material and the cumulative amount of the stage are maintained within the set range, and then reliable product quality is obtained.
9, centralized monitoring, control management computer as the upper computer, through the RS485 bus interface with the computer integrator and artificial intelligence regulator for two-way communication, and through the RS232 interface with the PLC in the power control cabinet for two-way communication, and to monitor the entire production process, constitute a complete automatic batcher balance. According to the needs of the production process, the user can set parameters, start and stop the equipment in the industrial computer, and manage and control the entire batching scale, and print reports. At the same time, the industrial computer also has an RS485 two-way communication interface for communication with other industrial computers.
10, decentralized control according to the requirements of the production process, directly input parameters to the computer integrator and artificial intelligence regulator, start the button on the panel of the power control cabinet to carry out automatic system work; The system can also be operated manually (on-site or remotely).
11, the reliability of automatic batching scale is high. Distributed control can make the system work as follows: manual work; Work on site; After leaving the industrial computer, it works automatically with the support of intelligent weighing instrument; The upper computer controls the automatic work and the upper computer sends the formula parameters to the downward computer through the serial port to realize the automatic work, and the weighing terminal greatly improves the reliability of the system.
12, good product quality and production efficiency in the production process, according to the characteristics of the production process and process requirements, through the automatic batching scale and automatic metering equipment, can ensure that each material is operated under high precision (single machine accuracy up to 0.5%), and then ensure the accuracy of the mixed material (system accuracy up to 1.0%), so as to ensure the quality of the product. Increase production efficiency.
13, the processing capacity of the production process is strong according to the needs of the production process, modify the corresponding parameters in the industrial computer, which can meet the needs of different industries and mines, and greatly improve the ability of the system to adapt to the production process.