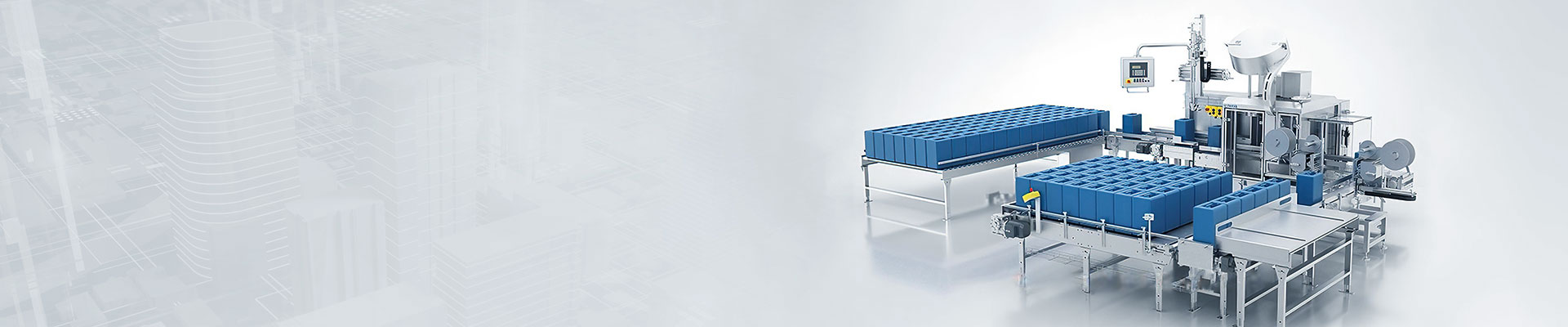
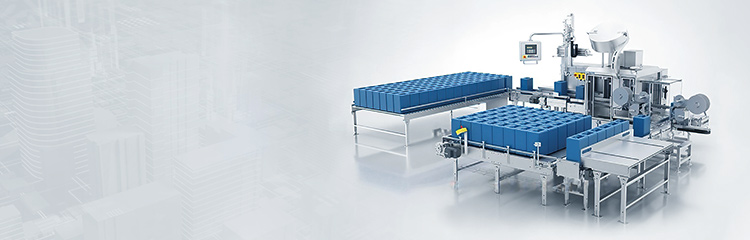
The automatic feeding and unloading system adds the material from each bin to the electronic scale according to the raw material ratio given in the production formula, and then sends it to the hot and cold mixer for mixing and stirring, and correspondingly controls the temperature of the material mixing and stirring, so as to ensure that the material is evenly mixed and the characteristics of the mixture meet the requirements of the production process. Finally, the mixed mixture is used in three production lines of PVC foam board, foam pipe and profiled profile. The upper computer can choose industrial control computer or programmable controller. The industrial control computer can develop practical dosing software package under the WINDOWS system platform to realize real-time dosing control and data management.

The feeding and unloading system connects the 4~20mA signal of the hopper scale to the dual-channel signal transmitter and divides it into two channels, one connected to the control system and the other connected to the new Weighing system. The acquisition and transmission methods of the original PLC control system remain unchanged, but the new weighing acquisition system communicates directly with the weighing equipment by installing RTU equipment in each district and city, reads the data through Modbus/Tcp protocol, and then uses the stability judgment algorithm to get the coke loading amount each time.
The new RTU equipment in each district is connected to the backbone Ethernet through the network interface, and the system communicates with the RTU in each district through the Ethernet, and uses the Modbus protocol format for data interaction with each station. The Modbus protocol defines the information structure that controllers can recognize and use. When communicating over a Modbus network, the protocol enables each controller to know its own device address, identify the data addressed to it, and retrieve the data information contained in the packet. The controller can also organize reply messages and send them out by using the Modbus protocol.
One STC-511RTU is added to each zone, and the device uses the open Modbus/Tcp communication protocol. In order to improve the efficiency of data communication and processing, the software adopts object-oriented multi-threading technology to develop C/S architecture software based on Modbus/Tcp, and uses the relevant digital and analog data to carry out the corresponding logical judgment and data analysis, and saves the result data in the SOLServer database. In order to facilitate users to query and analyze measurement data, the system also adopts B/S architecture design, publishes various accumulated data, analysis data and report data on the Web, and realizes the corresponding functional operation conveniently through the browser.
When the system receives the arrival signal of the material, the algorithm is activated and the collected data is stored in the defined array. When the next cycle comes, the collected data is compared to the first value in the array. If within the defined threshold range, the interpolation sorting algorithm is run and the values are stored in the array. Each time, the collected value is compared with the first value in the array, and the result determines whether to save. If the value of 10 consecutive times (array dimension) meets the conditions, it means that the weight of the object on the hopper scale is in a stable state, and the tare and gross weight can be obtained at this time. The median, cycle period, and array dimension can be adjusted according to the actual application.