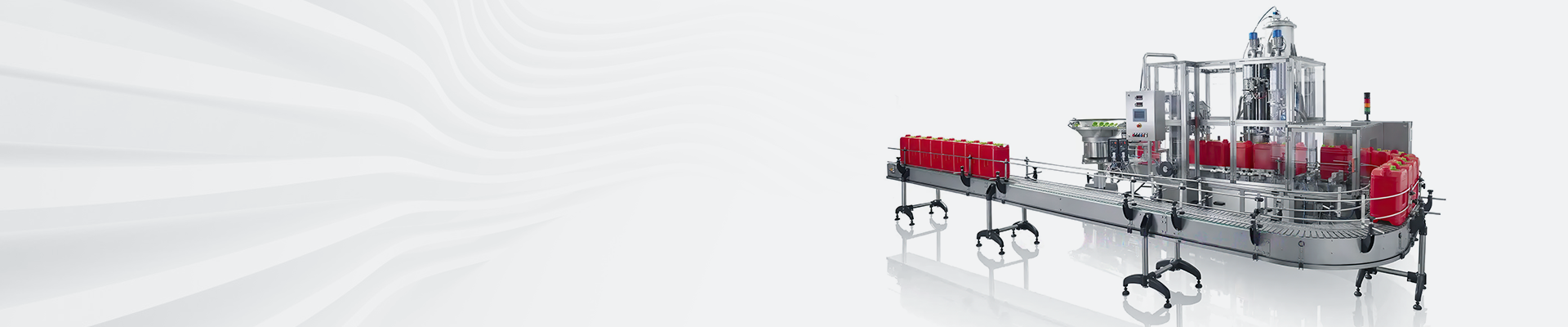
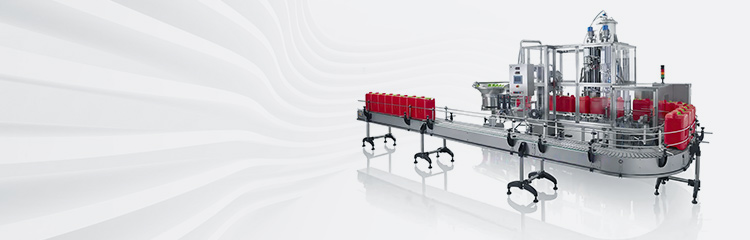

Summary:The liquid filling machine uses PLC as the control center to collect data from the weighing module, and the PLC exchanges information with serial communication.Proximity switches detect critical positions of the spray gun.
The automatic filling machine collects data from the weighing module with the PLC as the control center, and the PLC exchanges information with the serial communication method. Proximity switches detect the key positions of the spray gun, i.e. the highest position of the gun, the gun rising into position, and the gun falling into position in the barrel. The gun lifting speed can be set and modified. PLC controls the driver to drive the stepping motor to run, and the stepping motor drives the ball screw, thus lifting the gun to the precise position. Indicator light is used to indicate filling status and output alarm status, relay is used to indirectly control nitrogen blowing and press platen. Touch screen can set the filling data with recipe function, use the recipe function to parameterize the commonly used filling materials. With manual/automatic/standby selector switch, manual lift gun switch, fast/slow lift gun selector switch, start/stop filling button and other functions.
Weighing and filling machine system industrial control machine using WIN7 system platform, using PLC two-stage size of the material automatic filling method, can store 30 groups of filling value parameters. Filling system hardware module is mainly composed of the main control board, A/D conversion, man-machine exchange, filling valves, pneumatic ball valves, optoelectronic isolation transmission, etc.; the main control board circuit is mainly responsible for the completion of the weighing system control and arithmetic work Signal Acquisition Circuit is mainly responsible for the filling of the corresponding instructions to complete the acquisition of the target value in the filling and in the form of signals will be the pressure value passed on to the next set of A/D conversion circuit is mainly responsible for the upper level of the signal passed to the next level of conversion into a signal that can be stored. A/D conversion circuit is mainly responsible for converting the signals transmitted from the first level into signals that can be effectively processed by the computer, the man-machine exchange circuit is mainly responsible for parameter setting and monitoring the control system operation status, the optoelectronic isolation circuit is mainly responsible for the signal isolation transmission and elimination of the system actuators and hardware circuits with each other in the interference; the output signal amplification circuit is mainly responsible for the output signals in the system for the appropriate amplification process, thereby facilitating the actuator to carry out the next step. The output signal amplifier circuit is mainly responsible for amplifying the output signal in the system to facilitate the actuator to carry out the next step.
Liquid filling machine adopts advanced control, equipment modeling, process optimization technology to realize a variety of network-driven hardware modules, through the open specification of the OPC client and server interfaces, the use of transparent network management technology to achieve data communication with third-party equipment, the construction of a distributed real-time database of engineering objects to achieve the global consistency of the weighing data and data from external equipment and a unified interface, to meet the industrial data of the multi-real-time, multi-semantic, multi-timing To meet the requirements of multi-real-time, multi-semantic, multi-temporal and multi-scale information integration and interface openness of industrial data, and to realize the network interconnection and data interface between the filling system and the intelligent equipment, and to realize a complete set of special weighing system for the filling control process.
The automatic filling machine directly controls the filling process and accomplishes the tasks of data acquisition, processing, storage and display, fault detection and alarm, and data communication. By communicating with the slaves, it completes the required control tasks, with real-time display of working conditions, filling optimization, management consulting and other functions. The data exchange between the host and each slave and the control of each slave is realized through the real-time display module of the working condition. The host issues cycle commands to each slave and enters the filling cycle process; receives the working condition information from each slave in turn. Real-time dynamic display, and according to the corresponding control program to send control commands to the slave.
Explosion-proof filling machine using a PC-based control platform packaging technology, the industry all I / O terminal modules and drive controllers through communication. This includes safety technology, which uses terminal modules. By a stainless steel panel type PC using a processor. the enclosure is seamlessly designed to meet the stringent hygiene requirements in the packaging industry, especially in the paint industry. all functions and operating modes of the explosion-proof filling machine, such as end-point position monitoring or start-up monitoring of the original position, are programmed in the automation software-based application. Special measuring functions are also integrated in the filling machines, such as monitoring for the container filling level, temperature measurement and sensor monitoring for the cleaning process. When using the software for servo technology, the filling machines can perform industry-specific functions such as lifting containers, moving pistons, sealing plastic bottles with aluminum foil or screwing on sealing caps fairly quickly and easily.