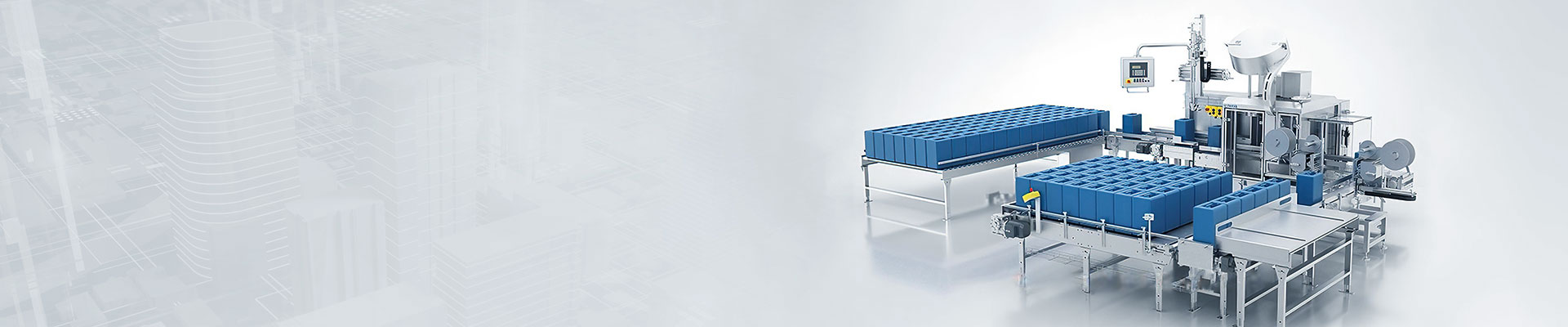
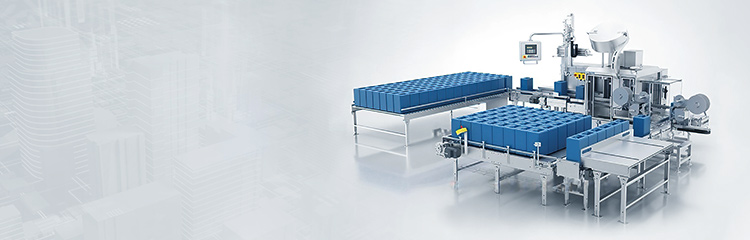
Batching scale to achieve material transfer, batching control, formula design, production data management and other functions. And it can realize the collection control of multiple ingredients through the network. With PLC as the next machine ingredients, once the production plan is completed in the entire production process, the computer will weigh each raw material according to the plan, no longer need manual intervention. In this process, the worker only takes the material, and the computer checks the weight through the data sent by the electronic weighing, which reduces the work burden of the worker and improves the work efficiency.

The dosing system can set, manage and optimize the control of the production line through the process control, realizing the dosage control, mixing control, feeding and spreading base material control, proportion adjustment and so on. The equipment mainly consists of Weighing modules and speed measuring weighing modules, weighing instruments, equipment speed control devices, bin level detection equipment, as well as redundant PLC, host computer and its software. Adopting Siemens S7300 series and ET200 module, the software adopts Siemens STEP7 series and WINCC series. The sintering raw materials are dosed according to a certain proportion according to the process requirements, and the feeding system is given according to the information of the material level of each silo at the same time. The automatic Dosage system control can be based on the weight of raw materials and chemical composition of the proportion control. At present, domestic manufacturers mainly batch according to the weight proportioning method.
The dosing scale is to control the raw material weighing and feeding device, according to the flow of the weighing and feeding device, the PLC system sets up the ratio of raw material and the total feeding quantity, and at the same time arranges the order according to the raw material bin. Through the upper computer communication to set the flow of equipment under each bin, when the system starts the weight signal and speed signal to the secondary weighing instrument, through the amplification of the A/D conversion, calculate the instantaneous flow and cumulative amount, and display in the field weighing instrument. The weighing instrument uploads the signal to the PLC module, the PLC analog input module collects the weight signal and speed signal of the feeding device, and carries out the self-tuning operation according to the parameter set by the user, if there is a deviation between the set value and the current value, then the PLC analog module outputs a standard signal (4-20mA) to the frequency converter for the device to be adjusted, and the frequency converter will change the rotational speed of the device in real time after accepting the PLC signal, for the disc, it will change the speed of the device in real time. After receiving the signal from PLC, the frequency converter will change the rotating speed of the equipment in real time, which will reduce or increase the feeding material for the disk and reduce or increase the material flow for the speed regulating weighing, so as to make the system have a stable state.
When the batching machine normal operation for a certain period of time, the mixing bin material level will fluctuate because of the fabric situation, when the thickness of the material layer of the truck is stabilized, the PLC according to the level of the material in the bin measured by the weighing module of the mixing bin to adjust the flow rate of the material in each of the downstream ports of the batching bin, so as to ensure that the balance of material in and out of the mixing tank. Mainly for the two mixing liquid control and electrical interlocking. As the purpose of the first mix is to mix well, according to the total amount of mixed material before mixing and a certain percentage of liquid addition calculation, through the control of the first mix of electric regulating valve to regulate the flow. The current value of the dosage bin each downstream port cumulative calculation out of the mix, the material flow and shared to the mix automatically add liquid control dosage, according to the total amount of material and material into a mix before the percentage of the liquid content of the material to calculate the need to add a mix of how much liquid for a mix of automatic addition of liquid to provide the basis for the addition of liquid.