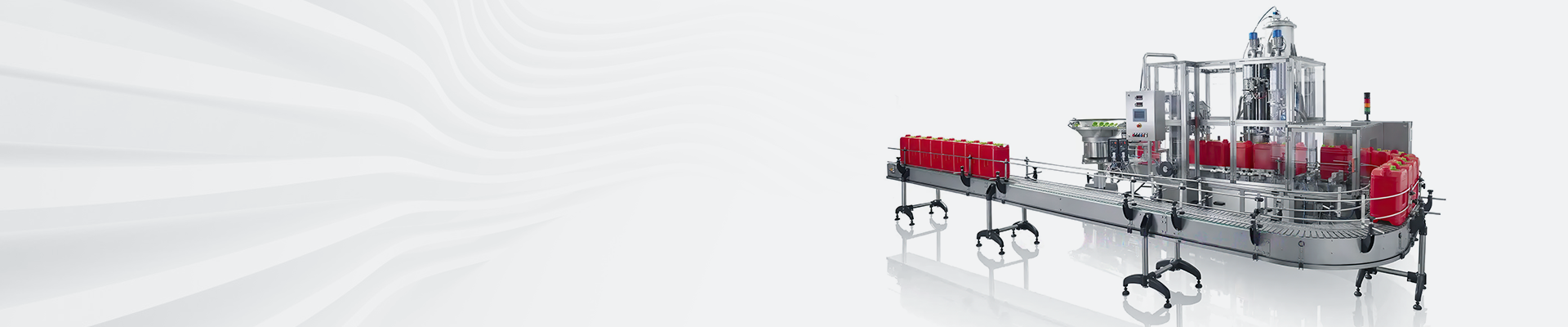
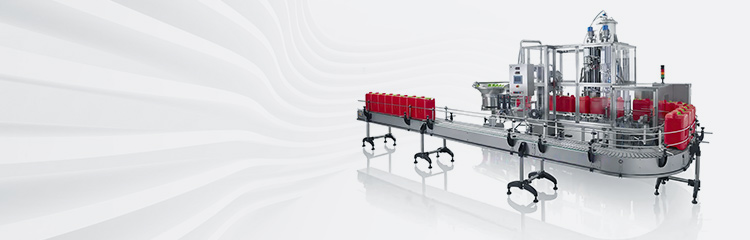

Summary:The drum transmission line is mainly composed of load bearing scale frame, weighing module, scale body support mechanism, swinging connecting rod lifting mechanism, electrohydraulic driving mechanism and installation support seat. The hydraulic swinging arm connecting rod device is installed on the cement concrete foundation of the foundation pit under the drum, the lower weighing body (weighing body support frame) is installed on the connecting swing block of the hydraulic connecting rod device, the weighing module is placed between the lower weighing body and the upper weighing body, and the weighing module adopts the self-limiting disc type weighing module structure.
1. High-speed quantitative batching system
This weighing and dosing system is controlled by microcomputer to weigh and compare the weighing module, and output control signal to execute fixed value weighing, control the operation of external feeding system, and implement the tasks of automatic weighing and fast dispensing.
The feeding system adopts MCS-51 microcontroller and V/F voltage and frequency converter and other electronic devices, its hardware circuit uses 8031 as the central processor, BCD dial as the fixed value setting input, the material is loaded in the hopper, the weight of which deforms the sensor elastomer and outputs the electrical signal which is directly proportional to the weight, the sensor's output signal is amplified by the amplifier and then inputted into the V/F converter to carry out A/D conversion, and the converted frequency signal is directly converted into the frequency signal, which is directly converted into the frequency signal. The sensor output signal is amplified by the amplifier and input into the V/F converter for A/D conversion, and the converted frequency signal is directly sent into the 8031 microprocessor, and its digital quantity is processed by the microcomputer. The digital quantity is processed by the microcomputer. On the one hand, the microcomputer sends the instantaneous digital quantity of the weight into the display circuit to show the instantaneous weight, on the other hand, it carries out a series of weighing fixed-value control such as comparing, opening and closing the feeding port and discharging the material into the box.
The working principle of the weighing module is to paste the resistance strain gauge on the elastic sensitive element, and then, in an appropriate way to form a bridge, so as to convert the mass of the object into an electrical signal. Silo weighing module is mainly composed of two parts, the first part is the elastic sensitive element, he will be measured by the mass of the object pressure into the strain value of the elastomer; the second part of the sensing element is the resistance strain gauge, he will be synchronized with the strain of the elastomer into the change of the resistance value.
In the whole fixed value sub-loading control system, the kettle weighing module is the key component affecting the measurement accuracy, and GYL-3 strain load cell is selected. Four pieces of resistance strain gauges constitute the full bridge bridge circuit, in the case of the added bridge pressure U is unchanged, the output signal of the sensor is proportional to the gravity acting on the sensor and the bridge pressure for the bridge, and, the bridge pressure for the bridge U change directly affects the measurement accuracy of the electronic weighing, so it is required that the bridge pressure is very stable. Millivolt-level sensor output is amplified into a 0-10V voltage signal output, sent to the V / F converter for A/D conversion, the frequency signal output from its output is added to the microcontroller 8031 timer 1 counting, input T1. In the microcomputer by the timer 0 for counting timing, timer 0 timing time set by the required A/D conversion resolution.
The counting value of timer 1 reflects the size of the measured voltage, i.e. the weight of the material. At the same time as the display, the computer is also based on the set value and the measured value of the fixed value judgment. The measured value is compared with the given value, the difference is taken to provide PID operation, and when the weight is insufficient, the material continues to be fed and the measured value is displayed. Once the weight is equal or greater than the given value, the control interface outputs a control signal to control the external feeding device to stop feeding, display the measured final value, and then issue an answer command to indicate that the bag is finished and the next bag can be loaded and weighed.
Each loaded box or bag moves along the conveyor belt until the loaded electronic weighing below, the conveyor belt stops moving, the electromagnetic coil 2 is energized, the electronic weighing hopper turns over, so that all the material is poured into the box or bag, when the material is poured out, the conveyor belt motor is energized again, the loaded box or bag is moved out, and the protection conveyor belt continues to run until the next empty bag or box cuts off the light source of the photoelectric sensor, and at the same time At the same time, the electronic weighing box is reset, the electromagnetic coil 1 is energized, and the funnel is fed to the electronic scale automatically, the weight is controlled by the microcomputer, when the material in the electronic scale is equal to the given value, the electromagnetic coil 1 is de-energized, and the spring force closes the funnel door. The loading system starts the next loading cycle. When there is enough material in the hopper and boxes on the conveyor belt, the process can continue continuously. If necessary, the * operator can stop the conveyor at any time and change the weight in the boxes or bags by entering a different given value via the draw dial and then starting it again.
This system uses different sensors, change the weighing range, then can be used in cement, sugar, flour processing and other industries in the automatic packaging.
2. Sensors in the application of industrial electronic scales
At present, the use of industrial electronic weighing scales is very popular, and will gradually replace the traditional pole weighing and mechanical weighing. Electronic weighing scales in the weighing platform structure has a significant feature: a fairly large weighing platform, only in the middle of the device a specially designed sensor to bear all the weight of the material.
Commonly used electronic weighing scales sensor structure, for the double elliptical holes elastomer, weighing pan with a cantilever beam end on the plane of the two screw holes fastened; for the plum blossom-type four consecutive holes elastomer, weighing pan with a cantilever beam end of the side of the three screw holes solid, the middle of the support rod on the strain gauges affixed to the compensation. These two forms of sensors, the most used in the weighing scale. Three-beam bending elastomers, sampling bending stress, sensitive to weight response, suitable for making small weighing scales. Three-beam shear elastomers, sampling the shear stresses in the middle sensitive beam, are suitable for making weighing scales with a weighing range of several hundred kilograms.
Counting scales with elastomer structure with these compound beam type high-precision sensor to support a large weighing platform, the weighed weight and may be placed in any weighing platform in any position, will inevitably produce four corners of the value error, (b) two forms of structure of the sensor, can be filed in the form of angular difference correction. It has upper and lower two locally weakened flexible auxiliary beam, so that the sensor has a strong resistance to lateral force, lateral force and torsional moment, can be adjusted by filing the flexible parts of the auxiliary beam to adjust the sensor's sensitivity coefficient and four-corner error. The sensor adopts the plum blossom type four consecutive holes structure, the scale has the functions of zero setting, automatic clearing of unit price, automatic zero tracking, automatic tare, the number of times and the amount of totalization, printout, etc., and the 7-segment green fluorescent digital tube display, which is very convenient to use.
The circuit block diagram of electronic weighing scale adopts the principle of portable household electronic portable scale made by CHBL3 model S double-connected hole elastomer dynamic load weighing module, which consists of four parts, namely, static weighing module, amplification circuit, A/D conversion and liquid crystal display. In the figure, E is a 9V stacked battery, R1-R4 are four resistance strain gauges of the weighing module, and R5, R6 and W1 form a zero adjustment circuit. When the load is zero, adjust RW1 so that the liquid crystal display shows zero. A1, A2 for the dual operational amplifier integrated circuit LM358 in the two units of the circuit, composed of a symmetrical in-phase amplifier, A/D converter using ICL7106 double integral type A/D converter, the liquid crystal display using 31/2 liquid crystal display chip. The electronic scale is highly accurate, simple, practical and easy to carry.
The weighing module is a high-precision sensor that must be used according to the specified specifications. If it is not used according to the specified specifications, not only can it not play the role of weighing, but also easy to be damaged, especially it is absolutely not allowed to exceed the load safety value to use.
For the temperature change on the bridge zero and output, the impact of sensitivity, even with the same batch of strain gauges, but also due to the temperature characteristics of the difference between the strain gauges will be slightly caused by the error, so the requirements of higher precision sensors, temperature compensation must be carried out to solve the problem of the substrate being pasted on the use of appropriate temperature coefficients on the auto-compensation piece, and from the outside to it to be appropriately compensated.
Nonlinear error is the most important point in the sensor characteristics. Generate non-linear error for many reasons, generally speaking, mainly by the structural design decision, through the linear compensation, can also be improved.