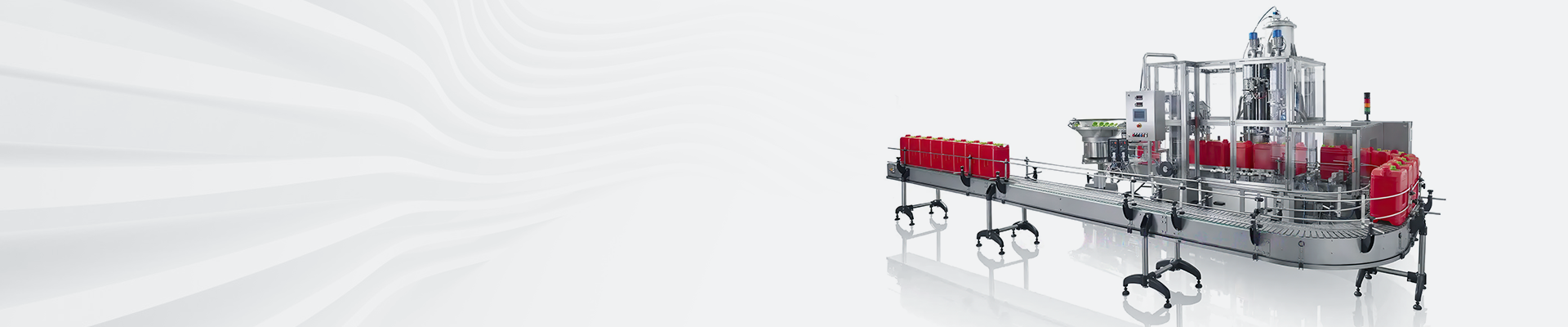
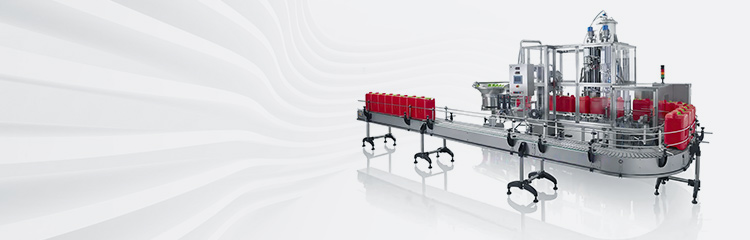

Summary:The preparation of dry mix before extrusion production is an important process, including the preparation of resin and various auxiliaries and the weighing and mixing of raw materials. The preparation of dry mixture is to put all kinds of raw materials into the high-speed mixer for hot mixing after correct calculation and weighing according to the formula requirements, and put them into the cooling mixer for cooling after reaching the specified temperature and time, and configure them into a uniform and loose, non-caking, easy to flow powder mixture. The quality of dry mixture directly affects the efficiency and quality of extrusion production. Therefore, the design and configuration of the equipment system should be reasonable, and the mixing process should be strictly controlled scientifically, including the feeding amount, mixing temperature and mixing time.
At present, most domestic manufacturers still use traditional manual weighing, supplemented by simple mechanical mixing for formula mixing, and it is difficult to control the content of each component, mixing temperature and mixing quality in the mixing process. Therefore, through the analysis and research of PVC production and mixing, this paper proposes that the pneumatic conveying of premix and finished material can be achieved by pipe pressure formed by Roz fan, and the control system is composed of PLC and industrial control computer. The weighing value control technology can realize the accurate weighing of main and auxiliary materials and the accurate temperature control of hot and cold mixer. It achieves the purpose of reducing environmental pollution, improving production conditions, raising work efficiency and controlling product quality.
1 The role of the mixture in the quality control of PVC profile production
Mixing is an important part in the production of PVC profiles, and the quality of dry mix directly affects the physical and chemical properties of profiles. The preparation of dry mix before extrusion production is an important process, including the preparation of resin and various auxiliaries and the weighing and mixing of raw materials. The preparation of dry mixture is to put all kinds of raw materials into the high-speed mixer for hot mixing after correct calculation and weighing according to the formula requirements, and put them into the cooling mixer for cooling after reaching the specified temperature and time, and configure them into a uniform and loose, non-caking, easy to flow powder mixture. The quality of dry mixture directly affects the efficiency and quality of extrusion production. Therefore, the design and configuration of the equipment system should be reasonable, and the mixing process should be strictly controlled scientifically, including the feeding amount, mixing temperature and mixing time.
2 Automatic mixing equipment and mixing process
2.1 Material Collection system
The material collection system is used to collect bulk or bagged raw materials to the storage bin by various means. The bulk materials can be sent directly to the storage bin through the pneumatic conveying device on the tank truck. The bagged materials are collected by the ton bag filling station. The material at the contact point between the box and the material is 1Cr18Ni9Ti stainless steel, the inner surface is polished, and it is a sealed structure. The filling station is composed of gas storage tank, sending tank, hopper scale, dense phase conveying system, dust collector, etc.
2.2 Material handling system
The conveying of materials is the key to realize automatic mixing. The conveying system occupies a large proportion in the PVC automatic mixing system; The transportation of raw materials from the ton packing station to the storage bin, the transportation from the storage bin to the main silo above the electronic scale, the transportation of finished materials from the mixing machine to the finished silo, and the transportation of finished materials from the finished silo extruder. There are two main forms of application here; Screw conveying and pneumatic conveying.
Screw conveyor. Mainly used in electronic weighing feed and extruder feed.
Pneumatic conveying. Mainly used in warehouse and material conveying.
Pneumatic conveying is mainly divided into pneumatic positive pressure conveying and pneumatic negative pressure conveying. Pneumatic positive pressure conveying equipment is generally composed of Roz fan and rotary valve, and Roz fan is responsible for providing low-pressure air required for conveying materials. The rotary valve is responsible for quantitative feeding, which can ensure continuous and uniform feeding. Its advantage is that it does not require a special compressed air source, and the investment is small. The disadvantage is that when the material is wet in spring and autumn, the pipe louie is blocked, and the segregation of the material is easily formed during the transportation process. Pneumatic negative pressure conveying mainly uses the negative pressure vacuum generated by the Roots vacuum pump to absorb the material, and then separates the material from the gas through the filter device. Its advantages and disadvantages are similar to thin phase positive pressure transportation. But it is less likely to cause congestion, and the investment is smaller.
2.3 Automatic weighing system
In the PVC automatic batching system, the weighing batching consists of two sets of independent electronic scales. One set of main material electronic scale and one set of auxiliary material electronic scale. Each set of batching system is composed of the material bin, the corresponding screw conveyor, electronic scale and other parts.
The main problems to be solved in automatic weighing and batching; (1) Selection of feeding device. The main material electronic scale charging auger size is large, the scale rating is large, suitable for weighing PVC main material. The auger size of the auxiliary material electronic scale is small, the rated scale is small, and it is suitable for weighing the auxiliary material with small feed amount. This design facilitates accurate measurement of materials. Main material electronic scale feeding device form for the screw feeder, due to the proportion of the main material is large, in ensuring uniform and accurate feeding at the same time, must consider the weighing time, so in the selection of screw feeder, should first consider the selection of power and feed large model. On the contrary, as an auxiliary electronic scale, the material weighed is mostly micro-material, which requires higher weighing accuracy, so the screw feeder is required to choose a smaller model to meet the requirements of weighing accuracy.
(2) Material flow difficulties. For the automatic weighing control system, it is not only necessary to ensure the accurate weighing of materials, but also to ensure the smooth flow of materials. Including the flow of the auxiliary material from the auxiliary bin to the auxiliary electronic scale, and the flow from the auxiliary electronic scale to the main material electronic scale. PVC main material flow is good, can be natural blanking. Poor flow of accessories, PVC profile formula are added like titanium dioxide, calcium carbonate and other poor flow of accessories, in the automatic weighing process often appear material bridge, and after the completion of the material is still part of the material stuck to the wall phenomenon, weighing accurate but inaccurate situation, seriously affect the quality of dry mix, in view of this situation, It is necessary to add a pneumatic wall vibrator on the outer wall of the auxiliary silo, and it is also possible to install an air cushion or apply a special material coating on the inner wall of the auxiliary silo to promote the smooth flow of materials.
(3) The connection between the main and auxiliary electronic scales and the equipment. Because the electronic scale relies on the sensor for measurement, during use, it is affected by the jitter of the surrounding equipment and the impact of the opening and closing of the pneumatic disc valve. In order to minimize the influence of external factors, cloth soft connections should be used on both the upper and lower parts of the electronic scale to improve the accuracy of the electronic scale in automatic measurement.
(4) Layout and parameter setting of automatic weighing control system. Automatic weighing control system includes gravity sensor, pressure transmitter, metering control instrument and so on. When installing the device, the sensor should be evenly distributed as far as possible, and the sensor should be centered to ensure the sensor accuracy. When setting the sensor parameters, the weighing feed speed should be set, that is, the rough limit value, the fine limit value, and the drop value should be taken into account. Taking into account the deformation of the sensor during use, as well as the influence of voltage and electromagnetic, the electronic scale should be corrected once a week to ensure the accuracy of the electronic scale.
2.4 Mixing equipment
The high and cold mixing unit is the first choice for PVC mixing process, and the high speed mixer is equipped with mixing blade and deflector. The purpose of high-speed mixing is to fully collide, contact and friction the particles of each component in the material under the action of the blade, so that the particles of each component can achieve the maximum distribution, so as to heat up the material and achieve pre-plasticization. Generally, the hot mixing temperature is controlled at about 110~120℃, if the temperature is too high, it will lead to the decomposition of PVC, affecting the production during the extrusion process; If the temperature is too low, it will lead to the material "raw", and the material is not easy to plasticize during production, resulting in a decline in profile performance.
The purpose of cold mixing is to fully cool the material to avoid heat agglomeration. PVC particle decomposition produces redness phenomenon, generally requires cold mixing discharge temperature below 45℃ for good discharge, the temperature is too high, the mixture in the process of placement, can not quickly heat dissipation, resulting in the mixture to absorb moisture in the air and yellow. The mixed dry mix is best stored at room temperature for more than 8 hours, which is conducive to further curing of the material, eliminating static electricity generated during the mixing process, improving the fluidity of the dry mix, and conducive to the implementation of the extrusion process.
In the production process, the key components of the hot mixer are the baffle and the thermoelectric coupling. If the guide plate is loose or in the wrong direction, it will reduce the collision and friction degree of raw materials in the hot mixer, so that the uniformity of the mixture is poor; Thermoelectric coupling is the main component of temperature control, thermocouple damage or head sticky, the reflected temperature is not true, easy to produce raw material, paste pot phenomenon. Therefore, the baffle and thermocouple should be checked regularly. For cold mixer, the key parts are thermocouple and circulating cooling water, thermocouple damage will lead to cold mixing discharge temperature out of control, the material instability. Blockage of circulating waterway or poor water flow will lead to aging of materials due to too long cold mixing time, and affect the mixing yield. Therefore, thermocouples and circulating waterways should be checked regularly.
2.5 Material Storage Devices
Material storage equipment mainly refers to the various silos used for the storage of raw materials and finished materials. The material at the contact between the storage bin and the material is 1Cr18Ni9Ti stainless steel. Inner surface polishing, outer surface pickling passivation treatment. It is composed of silo body, silo top pulse dust collector, steel ladder, protective guardrail, rotary valve and other components. The feed and discharge are automatically controlled by the set high and low level meter.
2.6 Dust Removal System
According to the different occasions, the model of the dust collector is different, it is recommended that the filter material of the dust collector should be anti-stick aluminized film material with a filter core aperture less than 0.5 micron. It is the most advanced filter material in the world. In the process of use, the dust collector should check the pulse solenoid valve in time to prevent the solenoid valve from not working, damaging the filter material, making the work site environment poor, resulting in the loss of materials.
2.7 Extruder feeding system
Extruder material system can be divided into screw feed or spring feed, screw feed is composed of roots fan, pulse filter, rotary valve and storage bin, screw feeder. The spring feeder is actually a rodless screw conveyor, which can achieve a certain degree of bending and is suitable for the feeding of a single extruder.
2.8 PLC automatic control and monitoring system
The electric batching control system connects the whole set of equipment together, which is the guarantee of long-term stable operation of the automatic mixing line. It is suggested to use Siemens S7-300PLC to control the whole system, and use industrial computer to monitor and manage. The designed electronic control system includes field operating cabinet and central control system. To achieve automatic detection function, control function, automatic alarm, interlock function, management function. The whole system is centrally controlled in the monitoring room, and each device component icon is displayed on the display screen of the industrial computer, with related buttons and the automatic manual conversion button of the whole system, combined with the change of color, the operator can be at a glance from the display of the entire system operation system. Mouse click operation is easy to understand.
3 Closing remarks
The automatic feeding system can realize the automatic control of the whole process in the mixing production, which not only reduces the labor force, reduces the labor intensity, improves the production conditions, but also improves the reliability and safety of the mix, ensures the quality of the dry mix, and lays the foundation for the improvement of product quality.