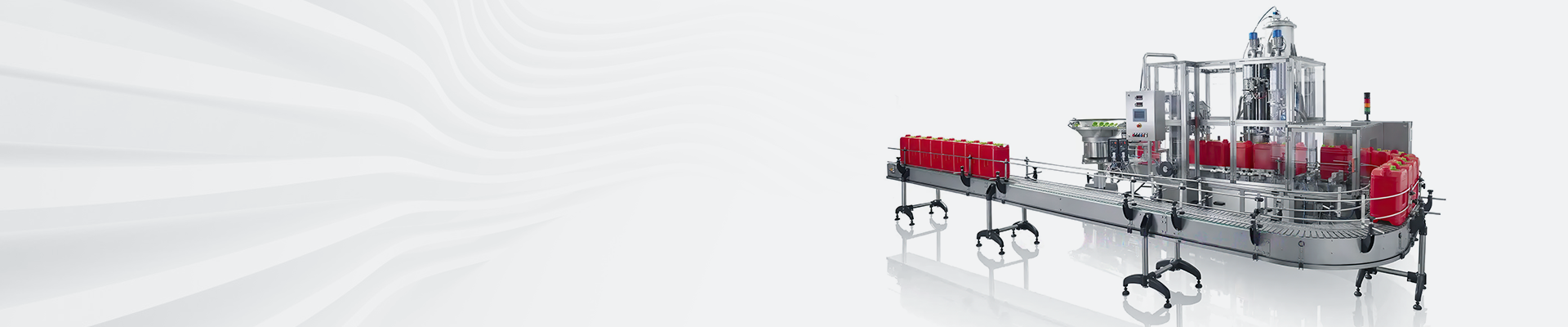
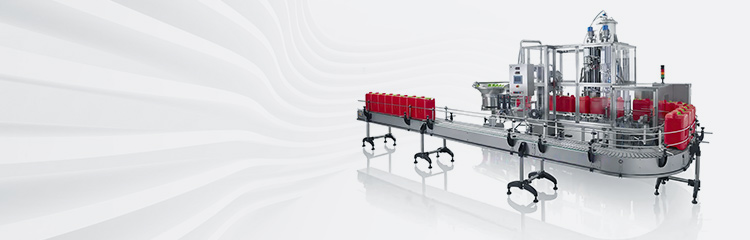

Summary:The vibrating feeder will lower the material into the reversible discharge hopper at the bottom according to the model set weight and actual weighing data. When the weighing weight reaches 80% of the set weight, the vibration of the vibrating feeder will start from The high speed changes to low speed and stops completely after reaching the set weight.
Stainless steel company 1, 2 converter with 6 sets of alloy material feeder, this 6 sets of systems arranged in the converter 7.6 meters platform, after feeding the use of forklift will be required to weigh the alloy material were transported to the converter 12 after the furnace ladle side. The original design is in the 6 sets of alloy silo below the installation of a 15-ton platform electronic scales, a common 3-ton truck (self-weight 9 tons), each time the material to be driven to one of the forklift 15-ton platform on top of the electronic scales, receiving vibrating feeder under the alloy material. According to different process requirements, vibrating feeder each time the material from 0.3 to 2 tons, there is a need to weigh the net weight of alloy material is far less than the forklift and alloy material of the gross weight of the problem, and the forklift each time the material needs to be in the platform scales for starting and stopping, steering and other milling weighing platform action, the impact of these actions is very strong is likely to cause the platform weighing platform shifting, tilting sensors, the weighing accuracy of the deviation of the undesirable consequences, routine maintenance labor strength, the daily maintenance of large deviations in labor intensity. These impactful actions will easily cause the platform to shift, tilt the sensor, and cause large deviation in weighing accuracy, and the daily maintenance is labor-intensive and expensive. The space around these 6 systems is narrow and does not have enough space for installing weighing bins, lowering gates, belts and other equipment. Based on the above reasons, it is imperative to optimize and improve the original feeding system.
2Project Improvement Method
Take one set of alloy material automatic dosage system improvement as an example to illustrate: the original 15-ton platform weigher is changed to 2-ton; in the 2-ton platform weigher is installed on the platform of the reversible unloading hopper, the right side of the reversible unloading hopper is fixed by the top steel bracket with bearings, and the left side is fixed by the lifting cylinder with bearings on the top support bar, so as to make it easier for the flexible reversal of unloading hopper, and the level and the highest level of reversible unloading river is installed with a proximity switch to control the unloading hopper, and a proximity switch is installed to control the unloading hopper. There is a proximity switch installed to control the lifting amplitude of the unloading bucket, the upper and lower part of the lifting cylinder have air inlet for controlling the lifting of the cylinder, the cylinder can be steered left and right in the vertical plane and also can be high and low he shrunk, the forklift trucks do not drive to the platform above the platform to avoid the platform shifting and the damage of the weighing module, the photoelectric transceiver device is installed on both sides of the unloading bucket outlet. The signal of photoelectric device is transmitted to PLC, the unloading bucket can only be lifted up after the weighing value meets the requirement and the forklift truck blocks the photoelectric signal for 5 seconds, in order to prevent the unloading bucket's wrong action, the weighing converter selects the product of Ningbo Galaxy Company, receives the signals of 3 weighing modules and transmits them to PLC, which provides the basis of the weighing measurement; there are 3 metering modules installed in the lower part of the 2-ton platform weighing, and the output of millivolt signals is transmitted to the weighing converter, the touch screen selects Siemens product. The 2-ton platform weigher is equipped with 3 measuring modules at the lower part, which output millivolt signals to the weighing converter. In the touch screen to display the target value of the material and can be issued under the material refers to the signal; air source cylinder air source from the compressed air network, pneumatic reversing valve to receive signals from the PLC digital output template for the control of lifting and lowering the rise or fall of the cylinder; PLC selection of the 300 series of Siemens for the simultaneous manufacture of 6 sets of art of tipping weighing device.
3 work control process
Converter system secondary model will be calculated for each furnace steel need to add the type of alloy material, weight, and the corresponding information will be transmitted to the feeding site touch and on, for example; need to add people in the carbon iron 0.5 tons. And the car driver only need to touch the touch screen on the medium-carbon manganese iron feeder start button, vibrating feeder will be set according to the model weight and the actual weighing data will be under the material located in the lower part of the reversible unloading hopper, when the weighing weight reaches the weight of 80% of the set weight of the vibration of the vibrating feeder vibration will be from the high speed to a low speed, until the set weight is reached and then completely stop. After that, Aizuo driver will drive the car to the front of the unloading hopper, Aizuo hopper will touch the infrared signal installed in the front of the unloading hopper photoelectric switch, after a delay of 5 seconds in the PLC control installed in the unloading let the lower part of the cylinder will unloading hopper side from the top of the horizontal position to the highest position of the material will be poured into the forklift's hopper. The unloading hopper will trigger the high proximity switch in the highest position, and after an automatic delay of 3 seconds, the cylinder will be withdrawn, and the lifted side of the unloading hopper will return to the horizontal position, completing the loading action.
4 Conclusion
The optimization and improvement of the original alloy material feeding system has achieved good results in terms of reducing the amount of routine maintenance and improving economic efficiency, and is worth applying and promoting.